导读
随着国内炼油企业加工高硫原油比例的增加以及油品质量控制标准的提升,炼油企业面临的污染物排放压力越来越大。尤其是各装置在停工检修过程中,受原料及加工方案的影响,装置产生大量的气体、油品和污水,如果处理不当,大量油气排放至大气,造成环境污染。因此,如何实现绿色停工检修是当前大型炼油企业亟待解决的问题。
以国内某大型炼厂为例,该厂项目以“常减压-渣油加氢-催化裂化-加氢裂化-延迟焦化”为加工工艺路线,设计加工科威特高硫原油。针对首次绿色停工检修过程存在的难点,制定专项风险控制实施方案,做到油气全部密闭环保处理,保证了停工检修过程环保达标,实现“气不上天,油不落地”,为同类大型炼油企业提供了技术借鉴。
技术难点分析
01 硫磺回收装置二氧化硫排放超标
380kt/a硫磺回收装置是炼油项目的配套项目,采用两级克劳斯(Claus)转化+无在线炉尾气还原吸收(SSR)工艺,由四个系列的制硫单元和两个系列尾气处理单元组成。硫磺回收装置在停工吹硫过程中,不论采用传统的瓦斯吹硫,还是采用新兴的酸性气完全燃烧吹硫,烟气中二氧化硫浓度均严重超标,同时燃料气吹硫易析炭污染催化剂。酸性气完全燃烧吹硫易导致反应器床层严重超温,造成催化剂失活。保证吹硫期间烟气达标排放,同时保证系统吹硫效果,是此次硫磺回收装置停工检修过程主要难点之一。
02 新时期环保要求
随着炼油企业大型化、集约化,装置间相互关联度增加。炼油装置停工吹扫会夹带大量含硫、含氨的废气、污水和污油,污染环境。为符合环保标准,停工检修过程的“密闭吹扫”面临更大的挑战,尤其是塔器,经过多年运行,即使停工过程将存油退干净,其器壁及内构件上仍会附着少量存油及硫化物,传统的煮塔是采用底部给蒸汽,顶部放空。虽然器壁及内构件上的残油被吹扫蒸汽携带至大气,但现场排放会产生大量有味道的油气,导致大气污染。
03 系统高温重污油管线密闭吹扫
炼油企业加工原油日益重质化、劣质化,装置停工检修难度增加,尤其是重油装置,如常减压、渣油加氢、延迟焦化以及加氢裂化装置,停工吹扫难度大、蒸汽耗量大,而且污染物不易处理。对于重油系统管线,常规做法是在吹扫前通过从罐区引入柴油或是返回自产柴油进行置换,当重油管线出装置处出现柴油后,改为装置闭路循环,但在最后重油管线吹扫过程中,大量携带油气的蒸汽进入罐区,高温重污油系统面临负荷过大和罐区出现异味等问题。另外,系统高温重污油管线是全厂所有含重油装置退油和吹扫的后路,使用频繁,任务重,管理难度大。
04 硫化亚铁自燃风险
油品中的硫对管壁发生腐蚀,生成硫化亚铁。在设备停工检修阶段,若不采取有效预防措施,硫化亚铁与空气中的氧气会迅速发生氧化反应,释放出大量热量,并形成连锁反应,使温度迅速上升,引发自燃,进而引起火灾和爆炸等事故。传统的预防硫化亚铁自燃的措施主要有:隔离法、清洗法以及钝化法等。该炼油厂设计原料为科威特原油,硫质量分数高达2.75%。生产过程中,加氢反应产物富含硫化氢,硫化氢和装置塔容器及管线接触后易反应生成硫化亚铁,消除塔容器硫化亚铁是绿色停工检修难点之一。
05 胺液系统回收储存难度大
全厂胺液系统按富液来源分为非加氢型、加氢型及硫磺尾气胺液系统等3个系统,并对应其配套的溶剂再生系统。正常运行期间,全厂胺液系统总量约4000t,而溶剂再生系统贫液储罐的有效罐容仅3000t,还要考虑停工期间胺液系统将产生大量的高浓度冲洗液必须进行回收、储罐储存胺液时的安全高度要求、硫磺尾气的胺液不能与其他两个系统的胺液互混互用等因素,因此在当前胺液浓度下,溶剂再生系统现有的罐容不能满足停工检修期间胺液储存要求。
解决措施及效果
1 硫磺回收装置“热氮吹硫”
借鉴同类装置成功应用经验,硫磺回收装置停工期间采用“热氮吹硫”方案:以氮气为主吹硫,将系统的硫磺携带至液硫池和加氢反应器,同时配以合适的风量使反应器床层及系统管线积存的FeS自燃,吹扫过程气按正常流程,经尾气系统加氢反应并胺液吸收后,净化尾气经焚烧炉焚烧达标排放。
参照类似规模硫磺回收装置吹硫期间的氮气量及实际吹硫效果,停工检修前,保留原有氮气线流程,同步实施“自硫磺回收装置制硫单元管廊氮气总管新接管线至各列制硫炉前蒸汽线”的技改措施。在热氮吹硫过程中,所需氮气量按传统“燃料气当量燃烧吹硫”产生的过程气量折算,少量燃料气当量燃烧用于维持系统吹硫温度。
全厂停工期间加工低硫原油,同时四列硫磺回收装置错开停工,辅以“热氮吹硫”流程,装置停工吹硫过程中,烟气中二氧化硫质量浓度平均在260mg/m3,低于排放新标准400mg/m3,避免了大量高浓度酸性气长时间排放,保护了环境。
2 “密闭煮塔”
装置停工处理过程中,先进行系统水洗,再用蒸汽吹扫贯通,减少蒸汽吹扫过程产生的油气量。
如上图所示,煮塔时,各系统放空全部关闭,在设备和管线底部接蒸汽,吹扫蒸汽经塔顶空冷器和水冷器冷却后进入分液罐,分离出来的水排入污水系统,油进入污油回收系统,不凝气排入低压瓦斯管网。
各装置吹扫结束前对排放气体进行检测,检测项目包括烃、H2S等主要污染物含量,检测结果经生产人员、技术人员及HSE人员三方共同确认后方能停止吹扫,对外排放泄压。吹扫期间全厂设置200多处监测点,随时监控厂区大气状况,保证吹扫过程不扰民。停工吹扫期间下风向厂界监测点分析结果见下表。
3 延迟焦化装置放空系统增设接收全厂吹扫
污油线此次停工过程实施“放空系统增设接收全厂吹扫污油线”技改技措项目,即:延迟焦化装置放空系统增设接收全厂吹扫污油线及退油线,使延迟焦化装置放空塔系统满足接收全厂吹扫重污油并冷却条件,同时将各冷却物料送至相应的罐区或下游装置。
系统高温重污油管线增加至延迟焦化装置放空塔入口管线,停工期间各装置吹扫污油自柴油以下组分进行切割,直接吹扫至放空塔内,经过放空系统冷却,分别将塔顶冷凝的污水送至硫磺酸性水汽提装置,燃料气和其他不凝气气体送至低压火炬系统,塔底冷却的重污油送至低温重污油罐,实现吹扫介质全密闭排放。
停工吹扫期间,延迟焦化装置放空系统回收吹扫污油约1000t,接收吹扫蒸汽约2000t,燃料气气体约30dam3,成功避免了重污油吹扫至储罐内冒罐及设备损坏等风险,将全厂异味气体排放降至最低,实现了吹扫介质全密闭排放。
4 钝化清洗
全厂炼油装置高硫部位(涉及200多台设备)全部进行钝化清洗,钝化清洗剂均为弱碱性螯合剂,确认没有产生硫化氢风险;同时全厂塔顶增上了淋水线作为预防措施。
为确保钝化清洗效果,又要降低成本费用,需反复确认清洗部位、清洗介质,实现化学清洗一装置一方案,并尽量做到循环利用,发挥化学清洗的有效作用。另外,为防止FeS发生自燃,潜在FeS自燃装置均编制防FeS自燃预案。
本次停工检修过程中催化裂化、延迟焦化、加氢裂化和渣油加氢等装置重油系统采用柴油清洗,常减压装置采用化学清洗方式。从停工后设备打开情况来看,分馏塔内构件清洁干净,换热器清洁易抽芯,同时设备没有发生较大FeS自燃现象,表明设备清洗、钝化效果良好。
5 胺液提浓
为解决停工检修期间的胺液储存问题,保证全厂停工检修按计划进行,停工前将各系统的胺液送至溶剂再生单元提高胺液浓度。
提浓的胺液送至贫胺液罐,冲洗水送至酸性水罐。为保证停工检修期间胺液与冲洗液分类储存,提前完成溶剂再生单元贫液罐(4×1000m3)清罐,用于储存胺液;完成一列汽提单元原料水罐(5000m3)清罐,用于储存冲洗水。
停工期间,根据原制定的退胺方案及冲洗方法,严格控制冲洗水量;按照停工统筹安排,同一胺液系统内不同脱硫装置间的停工退胺及冲洗时间尽量同步或间隔应尽可能短,同时退胺及冲洗过程上下游装置加强联系沟通,按照操作步骤和时间要求严格执行。通过上述系列措施,最终顺利完成全厂胺液系统的转移储存及正常停工。
免责声明:本网站所转载的文字、图片与视频资料版权归原创作者所有,如果涉及侵权,请第一时间联系本网删除。
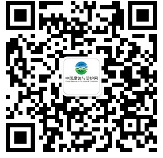
官方微信
《中国腐蚀与防护网电子期刊》征订启事
- 投稿联系:编辑部
- 电话:010-62316606-806
- 邮箱:fsfhzy666@163.com
- 中国腐蚀与防护网官方QQ群:140808414