一、引言
环境保护、节能减排、高性能以及特定功能化是未来防腐涂料的发展趋势。国际著名涂料公司正在把开发具有环境友好型的重防腐涂料作为重要研发项目,国内涂料市场也在朝着环保节能的方向转变。随着国际上对环境保护的重视以及国内各种法规政策的要求,符合涂料工业的“4E 原则”(环保、经济、节能、高效)成为整个涂料工业发展的新方向。我国重防腐涂料也在发生着转变:油性涂料的水性化;单一低性能涂料的高性能化及多功能化;高 VOC 涂料的高固体化/无溶剂化;含铅等重金属有毒涂料的低污染、无公害化; 复杂表面处理涂料的低表面处理化;传统涂料的粉末化等。
图 1 2009 年我国重防腐涂料组成[1]
二、研究进展
1.高固体化
通常情况下,质量固体含量在 60%~80%之间的、满足一次性成膜干膜的厚度大于 80 微米的溶剂型涂料被称为高固体分涂料。随着国内外对环境保护的越发重视,VOC(挥 发性有机化合物)含量低的高固体分涂料的需求量逐年飙升。高固体分涂料由于可挥发溶剂含量少,环境危害小并且具有一次性成膜厚等优点,在钢结构等重防腐领域被广泛应用。与传统溶剂型涂料相比,高固体分涂料具有相同的施工条件, 在工业防腐领域占有重要位置。继续降低 VOC 含量,不断提高体积固含量是高固体分涂料未来的研究方向。
国家财政部、国家税务总局在 2015 年 1 月 26 日联合发文:“关于对电池、涂料征收消费税的通知”,通知包括:自 2015 年 2 月 1 日,开始对涂料征收消费税,本次消费税
征收的对象为涂料生产企业,消费税税率为 4%(按出厂价计算),涂料的 VOC 含量在 420g/L 以上的需要交纳消费税,高固体分涂料得以豁免。这一政策的出台,使高固体分涂料以及无溶剂涂料再度成为热点。
1.无溶剂化
无溶剂涂料又被称为活性溶剂涂料,在涂料固化成膜的过程中,溶剂作为涂膜成分,不向大气中排放对环境有害的有机化合物。随着环保意识的不断加强,国际上一些发达国家相应作出对涂料 VOC 含量的严格限制,无溶剂涂料由于能够减少可挥发溶剂对环境的危害而备受关注。
与传统溶剂型涂料相比,无溶剂涂料具备以下优点:有机物挥发少、涂层干膜内应力小不易开裂、一次性成膜厚、涂层固化过程收缩小、涂层边缘覆盖性能优异等。无溶剂涂料由于无挥发有机溶剂,在固化过程中无损耗,故可以在满足相同膜厚度的要求下比传统溶剂型涂料用量小,可降低成本。相比传统溶剂型涂料,无溶剂涂料一次性成膜度高,可避免反复施工,提高了施工效率,减少了涂装周期。有机挥发物的减少使得无溶剂涂料在涂装施工过程中的安全问题比如个人防护、防火、防爆等方面得到了有效解决,例如,油漆工人在密闭仓室内施工,空气中不含有机挥发物就会大大降低爆炸的可能性,大大提高了涂装过程中的安全性[2]。
目前市场上常见的双液型无溶剂涂料主要有:有机硅涂料、环氧树脂及其改性涂料、聚脲涂料以及 100%固体聚氨酯涂料。无溶剂涂料的特点:(1)物理性能优异。无溶剂涂料因为有机溶剂含量少或不含有机溶剂,在漆膜固化的过程中不会残存有机溶剂而降低涂层的物理性能。并且树脂反应均一且充分,分子排列紧密,无溶剂涂料因而具有良好的物理性能。(2)耐化学药品性。目前涂料市场常用的无溶剂涂料多为双组份涂料,A、B 双组份涂料的配比可以根据各种化学药品的特殊需求而改变。(3)涂装施工灵活方便。双组份无溶剂涂料反应迅速,固化时间只有几秒时间,因而可以节省施工时间,在短时间内根据涂层厚度需要反复施工,可满
足高涂膜厚度的需求。虽然无溶剂涂料在涂装过程中需要特殊的喷涂设备,但是因为其固化时间短且可在室温下固化, 因而可在现场进行涂装。另外,无溶剂涂料对气候条件要求较低,在低温或潮湿的环境中也可以直接施工,所以,施工操作是非常灵活方便的[3]。
1.低表面处理
在涂装施工之前,为了达到更好的防腐效果,需要对涂覆对象做一定的表面处理。研究表明,表面处理在影响涂层寿命的各种因素中占比 49.5%,明显影响涂层的使用寿命[4]。并且,涂料涂装前期对底材的表面处理所需费用占整个涂装工程费用的 60%,因而,如何降低表面处理费用以及研发低表面处理涂料成为涂料研究的重点。目前,主要的低表面处理涂料主要有:可直接喷涂在其他种类旧涂层表面的涂料、可带湿涂装、带锈涂装的涂料等[5]。
通常在对钢结构进行涂装前,需要对钢材进行喷砂前处理,表面处理的等级需要达到Sa2.5 级。这就对喷涂工程的整个施工过程有较高的要求:(1)喷砂处理会耗费大量的磨料并且需要专业的设备,大大的增加了工程造价;(2)对于那些含有复杂结构且含有复杂工作面的钢结构工程,喷砂工人很难对结构死角做到彻底处理;(3)对钢结构采用喷砂处理,会导致钢板变薄,结构强度相应降低,特别是在对已发生腐蚀的钢结构进行防腐处理时;(4)在喷砂过程中会产生大量粉尘也会带来一定噪声污染。
另外,国内外前期大量建造的钢结构设施,比如港口起重设施、海上钻井平台、桥梁和电塔等正逐步进入防腐维修期,需要对这些设施进行重新涂装。然而在这些已建设施上进行喷砂处理,会产生很多不可避免的问题涉及工程造价、环保以及施工困难等方面,存在非常大的困难。鉴于以上原因,国内外开始采用手工打磨的方式代替以往的喷砂处理。在船舶维修领域,也逐步采用湿喷砂和高压水除锈的方式代替以往的传统喷砂处理来减少对环境的危害。然而,手工打磨、高压水除锈以及湿喷砂等表面处理方式却很难达到Sa2.5 级的要求。因此,开发对喷涂前处理要求低的低表面处理涂料成为国内外涂料研发的热点。
低表面处理涂料的作用机理:从结构上看,附着在钢结构外的铁锈是与钢铁底材附着不牢固的浮锈和与钢铁底材附着牢固的牢锈的疏松多孔的含水混合物;从成分上看,铁锈是一种包含活泼有害铁化物(? - FeOOH ,Fe(OH)2 ,Fe(OH )3 )和稳定无害的铁氧化物(? - FeOOH , Fe 2O 3 , Fe3O4 )的混合物。这就要求低表面处理涂料除了具备普通防腐涂料的性能还需要具备足够的渗透性和足够的反应性:这种渗透性使得树脂可以充分浸润锈层并且能够渗透到疏松多孔的锈层的各个角落,并最终使得锈层结合树脂后成为一个完全封闭的涂层来屏蔽腐蚀介质进入钢铁表面;这种反应性能够把铁锈中存在的活泼有害的铁化物转化为稳定的、无害的涂料填料。只有具备以上条件的涂料,才能适应低表面处理的底材,并最终将整个锈层转化为稳定的保护膜[6]。
2.水性化
近年来,国内外工业所用涂料绝大多数为溶剂型涂料, 然而溶剂型涂料存在固化过程产生大量有毒挥发物污染环境以及造成经济浪费等缺点,而且多数挥发物为易燃易爆的有机物给施工安全带来极大威胁。为消除溶剂型涂料挥发物带来的危害,许多国家相继出台环境保护法来限制VOC 含量, 号召社会积极发展“环境友好型”涂料(水性涂料、高固体分涂料、粉末涂料以及UV 辐射固化涂料等)。
据统计,美国在 1999 年所生产的涂料中,“环境友好型”涂料占 80%,其中水性涂料为 62%。水性涂料是以水为溶剂且主要挥发产物为水的涂料,具有低毒、可燃性低、VOC 含量低、低粘度、使用方便等优点。然而由于水的比热较大, 不易挥发,导致水性涂料更依赖施工环境,固化速度很大程度上受限于施工环境的温度和湿度。并且,水性涂料的涂装对基材表面处理要求较高,表面不能含有凝结水和油污。近几年,一些新型的水性树脂相继出现,应用于重防腐涂料中的水性涂料再度成为研发热点。如 Rohm&Hass 公司(美国),研发出性能优于溶剂型环氧/聚氨酯涂料的双组份水性丙烯酸/环氧树脂涂料。我国从二十世纪九十年代开始发展水 性涂料,水性涂料作为未来重防腐涂料的重要发展方向,虽然目前市场占有率较低,但是在未来具有广阔前景[7]。
目前,随着新型水性树脂以及防锈颜料的出现,水性防腐涂料不断发展,性能不断提高,并且开始应用于航空航天、汽车、桥梁、铁路机车以及船舶与海洋工程等领域。目前的水性防腐涂料主要有水性聚氨酯涂料、水性环氧树脂涂料、水性丙烯酸涂料、水性无机富锌底漆等。
三、结论及展望
目前来看,船舶用防腐涂料依然是以溶剂型防腐涂料为主。新型的船舶防腐涂料由于研发制造成本以及性能的认可度问题还没有在船舶涂料行业得到真正的普及应用,主要是以各大高校以及研究院作为科研课题在进行研究。但是,随着后期海洋环保要求的进一步提高,以及新型防腐涂料的成本下降,未来船舶防腐涂料的研究方向势必会朝着环境保护、节能减排、高性能以及特定功能化的大趋势发展。
参考文献
[1]范国栋.我国重防腐涂料发展特点的分析[J].上海涂料, 2012,(7):51-57.
[2]朱则刚.深度透析几种绿色环保的无溶剂涂料及其未来发展[J].行业应用研究,2014,(12):60-67.
[3]李海燕.无溶剂涂料[J].环境友好型涂料与涂装特刊, 2006,(11):25-30.
[4]杨万国.低表面处理涂料的研究现状与发展前景[J].现代涂料与涂装,2011,(2):24-27.
[5]黄红雨.海洋工程重防腐涂料的应用技术现状及发展分析[J].涂料工业,2012,(8):77-80.
[6]杨振波.低表面处理涂料技术现状及发展趋势[J].电镀与涂饰,2009,(1):61-63.
[7]龚涛.水性重防腐涂料的研究进展[J].广州化工,2010,
(8):32-34.
免责声明:本网站所转载的文字、图片与视频资料版权归原创作者所有,如果涉及侵权,请第一时间联系本网删除。
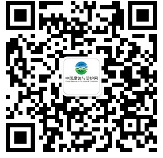
官方微信
《中国腐蚀与防护网电子期刊》征订启事
- 投稿联系:编辑部
- 电话:010-62316606-806
- 邮箱:fsfhzy666@163.com
- 中国腐蚀与防护网官方QQ群:140808414