露点腐蚀是由于工业气体在金属表面温度低于露点而凝聚所导致的腐蚀过程,在锅炉和各种燃气炉中,现场取样、切管,观察腐蚀产物后发现[1]:其横截面呈明显的分层结构,大致为3层:外层疏松、多孔,呈灰黑色,由大量灰颗粒和熔状物质堆积而成;中间层为灰沉积层,分布大量黑点和高亮条带状物质;内层为腐蚀反应层,致密,呈白亮色。
国内外学者对燃煤电厂的露点腐蚀研究结果表明[2,3,4,5,6,7,8,9]:燃料中的S在燃烧后绝大部分生成SO2,其中有一部分在Fe2O3或V2O5 (烟气或受热面金属表面中含有此成分) 的催化作用下转化成SO3,SO3与水汽结合而在温度低于硫酸露点的构件表面凝结成H2SO4,造成设备严重腐蚀。在省煤器、空气预热器、烟囱[10,11,12,13,14,15,16,17]等所有与含S气体接触的低温设备中,都有可能发生硫酸露点腐蚀,将导致大量管道和烟道的更换,造成经济上的巨大损失。
近年来,我国燃气-蒸汽联合循环发电技术 (以下简称燃机电站)[18,19,20,21,22,23,24]发展迅速,它具有效率高、安全可靠、单位千瓦造价低及低排放等特点,预计到2020年,我国燃气-蒸汽联合循环装机容量将达到5.5×107 kW,是1951~2000年已建成的同类机组装机容量的25倍;余热锅炉是燃机电站的重要组成部分,起着承上启下的作用,其性能对发电效率影响甚大;目前全国各地余热锅炉事故频发,表现为管壁减薄甚至爆管泄露,位置多发于低温蒸发段,现场取管切割后显示壁面为均匀腐蚀,腐蚀产物表征表明,S含量增加,推测管壁减薄的主要原因是硫腐蚀,即露点腐蚀。
对国内部分地区燃煤与燃气进行元素分析的结果表明,燃机电站与燃煤电站中露点腐蚀有所差别:(1) 燃料中元素量的差别,燃煤比燃气的S含量高,燃料中的硫分越多,则烟气中所产生的SO3含量也就越高,SO3的存在使烟气的露点显著升高,影响电厂设置排烟温度;(2) 灰分的差别,燃煤燃烧后排气含有更多的粉尘 (含未燃烧碳等),粉尘对于露点有两方面的影响,一是对SO2转变为SO3有催化效果,二是对SO3具有物理吸附和化学吸附作用,粉尘中的碱性氧化物可以和SO3反应生成盐,另外,含尘浓度高、吸附表面积大,也为SO3的凝结和吸附创造条件。
随着清洁能源的发展,越来越多的燃气-蒸汽联合循环机组建成投产,由金属腐蚀造成的受热面金属失效现象也越来越多,对燃机电站的露点腐蚀研究已经刻不容缓。
1 硫酸露点腐蚀模拟试验的研究现状
国外早在20世纪40年代就发现了低温露点腐蚀,并进行了大量研究,主要研究方法有3种:酸浸泡实验、实验室模拟实验以及现场腐蚀实验。露点腐蚀的本质是材料在酸性液膜下的电化学腐蚀[5,9],与酸浸泡实验的腐蚀机理显然不同,导致酸浸泡实验的结果遭受质疑。现场腐蚀试验的机会比较少,如果没有大量平行实验作为基础,将导致实验结论出现偏差。因此,人们把精力转向实验室模拟实验中,实验的难度在于如何获得模拟气体。
文献[25]公开了一种模拟硫酸露点腐蚀的实验装置及测试方法,该装置模拟气体产生特征在于把H2SO4溶液装入蒸发瓶,启动电加热套对蒸发瓶加热,电加热套的控制温度为60~200 ℃,在液体沸腾后产生腐蚀气体,该发明认为所产生的腐蚀气体为SO3,并以此模拟气体来研究硫酸露点腐蚀。由文献[17]可知,该发明的主要问题在于:稀H2SO4溶液在200 ℃以下沸腾蒸发所产生的主要气体为水蒸气,而腐蚀气体SO3极少,如表1,因此,该项研究效率较低,需要耗费大量的人力和物力。
表1 硫酸的沸腾温度-蒸汽相成分
文献[26]公开了一种测试材料耐硫酸露点腐蚀的试验装置,该装置模拟气体产生特征在于通过分液器加入一定量浓H2SO4溶液进入试验腔体底部,使其与NaHSO3溶液反应生成SO2气体,随后通过调节分液器控制硫酸溶液,持续产生SO2。该发明产生SO2作为腐蚀介质,而实际工况中是SO3与水蒸气凝结成硫酸的腐蚀介质,显然用SO2来模拟硫酸露点腐蚀是不准确的,专利文献[27]也出现了类似的问题。
陈华等[28]设计了一种高温露点实验装置,其中提到了从发烟硫酸中获取SO3的方法;Thibault等[29]在研究钙镁氧化物对SO3的吸附性能时,也采用了往恒温起泡器中加入发烟硫酸获取SO3的方式。发烟硫酸是一种含有过量SO3的硫酸,化学式:H2SO4·xSO3,无色至浅棕色粘稠发烟液体,其密度、熔点、沸点因SO3含量不同而异,当它暴露于空气中时,挥发出来的SO3与空气中的水蒸气形成硫酸的细小雾滴,所以称为发烟硫酸。大量证据显示可以通过发烟硫酸的挥发制取模拟气体,但因为发烟硫酸是一种危险物品,气密性要求高,此外生成的SO3量难以控制,所以实际运用难度很大。
赵瀚辰等[30]设计并搭建了小型低温烟气冷凝试验台,其中一部分功能是实现SO3的制取,SO3制取系统特征在于将SO2与O2气体通入550 ℃的电加热炉中,以铂金属丝作为催化剂反应生成SO3,SO3转化率可保持在40%。该发明不足之处在于实验设备价格昂贵,气密性要求高,高温危险,不适合装配在一般的实验室里。
赵钦新等[31]搭建了一套实验系统,各种气体经过质量流量计后在混合器内混合,在高温管式炉中被加热后腐蚀金属试样,其中O2、N2、CO2以及SO2均采用标准气体配置,而SO3和水蒸气是根据稀溶液成分等于其饱和蒸汽成分的原理,采用稀H2SO4溶液在一定温度下蒸发,通过N2为载气带出得到的,根据实际烟气中的比例,配置质量分数为0.856%的稀硫酸溶液,设置电热恒温箱的温度为58.6 ℃。实际上稀硫酸溶液的蒸发得到SO3的量极少,即使在N2为载气的带动下,硫酸蒸汽的产量依旧很少,不符合实验预期效果,如表2所示,而且在如此低的温度下,实验难度更加巨大。
表2 硫酸溶液蒸汽中的H2SO4含量 (mass fraction / %)
闫君等[32]对SO3酸雾发生方法进行了探讨。选用超声波雾化器作为SO3酸雾的发生方法,并辅助以高压射流喷雾器作为比较,制取特征在于:可以通过控制调节所使用的稀硫酸浓度来控制混入烟气中有效的SO3。硫酸露点腐蚀[33]是分阶段性的,腐蚀过程是一个变温变浓度的复杂的大气腐蚀过程。这种通过雾化的方式得到的酸雾粒径不均匀,并且酸雾表征的是小液滴的腐蚀,最终将导致实验结果与现场真实的气体腐蚀情况相违背,应用于硫酸露点腐蚀的机理研究将会导致结论出现偏差。
根据电厂实测数据,不同类型的电厂酸露点温度不同,普遍在100 ℃左右[19]。文献[34,35,36]表明:当温度低于200 ℃时,烟气中的SO3明显地转变成硫酸蒸汽,而且温度越低转化率越大。当温度低于110 ℃时,SO3转变为硫酸蒸汽的转化率接近100%,如图1所示。本文通过对硫酸蒸发特性进行系统研究,利用浓硫酸蒸发气体作为模拟气体,从而提供一种硫酸露点腐蚀模拟气体产生方法。
图1 SO3转变为H2SO4蒸汽的转化率与温度的关系
2 实验方法
主要试剂为浓硫酸 (AR),硫酸钠 (AR),氯化钠 (AR)、碳酸钠 (AR)、碳酸氢钠 (AR),实验用水为高纯水 (电阻率为18.25 MΩ·cm)。
图2为模拟气体产生装置示意图,工作流程:把浓硫酸装入特制蒸发瓶,打开油浴锅对蒸发瓶进行加热,浓硫酸在高温下蒸发,但由于其在这种蒸发情况下产生的硫酸蒸汽量少,所以设置通入N2为载气,N2将蒸发出来的硫酸蒸汽带出,在稳定的N2流速下,硫酸蒸汽的产生保持稳定和持续,保证了后续硫酸露点腐蚀模拟气体的用量,考虑到硫酸蒸汽遇冷极易凝结,所以设置输送玻璃管道外壁包覆绝热层,并严格控制玻璃输送管路的长度,降低硫酸蒸汽在输送过程中因凝结所产生的损失。
图2 模拟气体产生装置示意图
在包覆绝热层的玻璃导管后设置吸收瓶,吸收瓶内装有250 mL的高纯水,取出部分吸收液用883 Basic IC plus型离子色谱仪 (配Metrosep A Supp 4-250/4.0阴离子交换分析柱) 检测后,吸收液的电导率数值可以间接反映瓶内单一阴离子浓度,并做不同浓度硫酸溶液对应的电导率曲线,通过比对,研究硫酸溶液的蒸发特性。
3 结果与讨论
3.1 结果分析
3.1.1 离子色谱的测定结果
图3为高纯水和蒸发实验后吸收液的离子色谱图,通过混标绘制标准曲线,得出常规阴离子的定性方法,平行实验结果表明:吸收液里仅存的特征阴离子是硫酸根离子,从而证明高浓度硫酸在通入载气的情况下,可以得到硫酸蒸汽。
图3 高纯水和蒸发实验后吸收液的离子色谱图
3.1.2 不同浓度硫酸溶液的电导率结果
通过离子色谱结果得知,吸收液的特征阴离子是硫酸根,实验可以通过电导率的变化来表征吸收液单一阴离子的离子浓度,从而表征硫酸的蒸发效果,如表3所示,电导率-浓度对应曲线离子浓度的检测范围:10-6~10-2 mol/L。
表3 不同浓度硫酸溶液对应的电导率数据
3.2 影响因素分析
3.2.1 体积的影响
实验采用质量浓度为98.3%的浓硫酸溶液,并通入流速为200 mL/min的N2,蒸发瓶体积为250 mL,温度为140 ℃。由图4可知,当硫酸溶液体积为5~30 mL时,硫酸蒸汽的蒸发效果随着浓硫酸用量增加而增加,当硫酸溶液体积为30~40 mL时,蒸发效果的增加已经不明显了,即当硫酸溶液的体积与容器体积比为325以上时,再加溶液,蒸发效果变化不大,考虑到硫酸蒸发实验的危险性,建议溶液的体积与容器体积比在225~325。
图4 不同体积硫酸溶液,吸收液的电导率数据
3.2.2 浓度的影响
实验采用体积为20 mL的硫酸溶液,硫酸的浓度梯度为0.1,1,10和18.4 mol/L,并通入流速为200 mL/min的氮气,蒸发瓶体积为250 mL,温度为140 ℃。由图5可知,低浓度硫酸的蒸发难以获取硫酸蒸汽,实际蒸发的气体大多为水蒸气。由参考文献[17]可知:蒸发质量分数低于85%的液体,取得的主要成分为水蒸气,在85%~100%的质量浓度硫酸溶液,得到的是水蒸气与硫酸蒸汽的混合物,与本文的实验结果相一致。
图5 不同浓度硫酸溶液下吸收液的电导率数据
3.2.3 温度的影响
实验采用体积为20 mL的硫酸溶液,质量浓度为98.3%,在N2流速为0、200和300 mL/min时,分别设置实验温度为140、160和180 ℃,蒸发瓶体积为250 mL。由图6可知:随着温度的升高,产生硫酸蒸汽的量增大,这是因为温度升高加快了液体表面的剧烈相变反应,促进了硫酸从液相到气相的转变,以此提高了硫酸蒸汽产生效率,由图6c可知:在该流速下,温度的改变对实验效果的影响不大,这是因为相变反应在此时的环境中 (溶液的体积、压力等条件下) 已经达到极限,载气带动硫酸蒸汽流出的过程已然成为此时的主要影响因素。
图6 不同流速时吸收液的电导率数据
3.2.4 流速的影响
实验采用体积为20 mL的硫酸溶液,质量浓度为98.3%,在140、160和180 ℃时,分别通入流速为0、200和300 mL/min的氮气,蒸发瓶体积为250 mL。由图7可知高浓度硫酸溶液在不通载气的情况下,难以获取稳定、持续流动的硫酸蒸汽,在通入载气后,随着流速的加快,产生硫酸蒸汽的量越多,这是因为高流速载气加快带动硫酸蒸汽的流出,推动了蒸发反应由液相向气相的转变,以此提高硫酸蒸汽产生效率,建议可以根据实验需要,改变发生装置玻璃管路口径的大小,来设置合适的流速获取模拟气体。
图7 不同温度下吸收液的电导率数据
4 硫酸露点腐蚀验证实验
以燃机电站余热锅炉硫酸露点腐蚀为例,收集了国内某两个燃机电站现场监测数据,获得的排气成分数据列于下表4。
表4 燃机电站排气成分表 (volume fraction / %)
硫酸露点腐蚀验证实验主要研究在H2O、N2和H2SO4蒸汽的气体环境下,ND钢和20G钢的抗腐蚀性能。通过质量流量计控制气体的流速,混合后通过含有目标材质的试验箱,并通过失重法和XRD进行评价。表4中的数据显示实际环境中氮气和水蒸气体积比约为73∶9,因此设置混合气体对应的流速 (mL·min-1) 为VN2+H2SO4∶VH2O=200∶25,以12和24 h为时间梯度,并控制模拟气体产生装置的温度为160 ℃,试验箱温度为室温。
如图8所示,结果表明ND钢的耐硫酸露点腐蚀性能明显强于20G钢,另外,随着时间的增长,两种钢片的腐蚀速率都出现了一定程度的降低。图9为试片表面的XRD图谱,分析结果表明:试片表面形成了FeSO4·5H2O等晶体,这些晶体易吸附在试片表面,会一定程度减缓了硫酸溶液的侵蚀过程,进而影响试片的腐蚀速率,实验结果与张知翔等[11]一致。
图8 ND和20G钢的腐蚀速率
图9 试片表面的XRD谱
5 结论
比对了国内外硫酸露点腐蚀模拟气体的产生方法,分析其产生特征和不足。通过对硫酸蒸发特性进行研究,探讨出一种硫酸露点腐蚀模拟气体产生的新方法,结果表明:
(1) 硫酸溶液的体积和浓度对硫酸蒸汽的产生效果有影响,其中溶液的体积与容器体积比在225~325最佳,低浓度硫酸蒸发得到的主要气体为水蒸气,高浓度硫酸蒸发才能得到硫酸蒸汽,其中硫酸蒸发效果最佳的质量浓度为98.3%。
(2) 加热温度对硫酸蒸汽的产生效果有影响:温度越高,相变反应越剧烈,硫酸蒸汽产生的效率越高。
(3) N2的流速对硫酸蒸汽的产生效果有影响:不通载气不能获取流动的硫酸蒸汽,N2的流速越快,带动了硫酸蒸汽的流出,加快了硫酸溶液的蒸发速率。在高浓度硫酸+载气 (N2) 的情况下,才能获取稳定、持续流动的硫酸蒸汽,这种模拟气体产生的新方法有助于硫酸露点腐蚀的研究。
(4) 以实际燃机电站余热锅炉排气成分为例,验证了载流法用于硫酸露点腐蚀的研究是可行的。
免责声明:本网站所转载的文字、图片与视频资料版权归原创作者所有,如果涉及侵权,请第一时间联系本网删除。
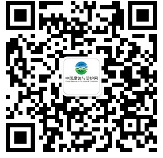
官方微信
《中国腐蚀与防护网电子期刊》征订启事
- 投稿联系:编辑部
- 电话:010-62316606-806
- 邮箱:fsfhzy666@163.com
- 中国腐蚀与防护网官方QQ群:140808414