涂层技术作为航空发动机的核心技术,发挥着隔热、防护、抗磨、抗冲击、减震等等不同的作用,从而提高了航空发动机的最高工作温度,减少燃油消耗,降低与空气的摩擦,延长航空发动机的使用寿命,保障航空发动机的安全可靠运行。
涂层厚度不均匀、黏接质量、厚度超标都将影响涂层的性能。在制作过程中,涂层和基体材料黏接不牢甚至脱黏;在使用过程中,涂层产生裂纹或者涂层与基体脱黏分离,都将严重影响航空发动机的运行安全,因此对涂层缺陷的检测十分重要。
航空发动机涂层缺陷的检测技术主要有红外热波无损检测、激光散斑技术、微波技术等。
散斑技术的加载方式分为机械加载与热源方式加载两种,一般用于脱黏缺陷的检测,不适合于涂层内部细微裂纹的检测。
红外热波无损检测技术是一种数字化新型无损检测技术,具有非接触、非破坏、检测面积大、检测速度快、便于在线在役检测、结果直观易懂等优点,受到越来越多研究人员的关注。
红外热波成像技术属于主动红外热成像技术,与被动红外热成像的区别在于其是主动施加热激励。目前,国际上主流采用高功率闪光灯进行热激励,但是闪光灯电源体积庞大而且笨重,闪光灯热均匀性差,只能近距离进行热激励。为此,南京诺威尔光电系统有限公司和中国南方航空工业有限公司的研究人员们采用激光扫描红外热波技术,利用线状连续激光束在试件表面进行扫描,形成高功率密度的脉冲热激励,实现试件表面的热激励。
激光扫描热波成像基本原理
红外热波无损检测技术主动采用热激励源对材料表面进行加热,形成的热波向材料内部进行传播,材料内部的缺陷如裂纹、脱黏、损伤等会形成热阻而影响热波的传播,从而引起材料表面温度场的变化。利用红外热像仪记录材料表面的温度变化,从而可以检测到材料内部的缺陷信息。
红外热波无损检测技术的必要条件是材料内部的温度梯度,而脉冲热激励则是产生这种温度梯度的有效方法。脉冲热激励主要包括闪光灯和激光。
近年来,半导体激光器的发展非常迅速,由于其功率高、价格低、体积小,在工业领域得到了广泛的应用。半导体激光器功率可以达到很高,但半导体激光器的输出一般是点光源,功率密度很高,容易损伤材料表面,不适合直接作为红外热波无损检测技术的热激励源。为此,研究人员提出采用线型激光束扫描方式,其激光器功率很高,功率密度低,可在材料表面形成短周期的脉冲加热,而不会损伤材料表面。
激光扫描红外热波成像无损检测技术示意
如上图所示,高功率激光器的光束经透镜整形,形成一均匀线型光斑照射在试件表面上,数据采集处理系统通过扫描控制装置,根据试件的特性来调节振镜和热像仪的扫描时序关系,从而实现对试件内部缺陷的检测。
激光扫描热波成像检测系统
激光扫描热波无损检测设备主要由计算机、扫描控制单元、测试平台等部分组成。测试平台包括激光器及冷却系统、扫描振镜、热像仪及光路系统等,其采用激光对试件表面进行扫描与采集红外图像。扫描控制单元用于控制热像仪和激光扫描振镜之间的同步。计算机系统用于硬件控制、系统监测、图像分析与处理等。
激光扫描红外热波无损检测设备外观
激光扫描热波无损检测系统中的关键技术在于激光扫描与采集之间的同步关系,确保激光一进入到红外热像仪视场就开始同步采集,对于后续图像处理是非常有好处的。激光扫描的快慢根据试件导热率决定,一般扫描速度在6~30mm/s之间。
检测效果验证
通常工件表面的涂层越厚,其温度梯度就越大,可以有效保护基体;涂层越薄,温度梯度越小,隔热效果越差。但随着涂层厚度的增加,涂层和基体界面的弹性应变能也会增加,从而导致界面裂纹扩展或者涂层与基体黏接。为此,研究人员制作了不同厚度的涂层试件,进行了两组试验。
人工试件
在一块尺寸(长×宽×厚,mm)为70×30×2的不锈钢板上制作了厚度约为0.5mm的特殊涂层,其中包括了一些人工缺陷。在制作涂层时,试件表面仅喷涂了2/3区域。
涂层试件1外观
检测时,热波图像的采集帧频为50Hz,采集时间为10s,激光扫描时间为6s。
试件1的热波检测结果
在检测图像中可以明显看到一个点状缺陷和一块状缺陷。块状缺陷为人为制作而成,制作时对该区域的表面进行了特别的处理,而亮点(点状缺陷)则是喷涂过程中产生的气孔。其点状缺陷水平方向长度约为0.8mm,块状缺陷水平方向长度约为26.8mm。右边近1/3的黑色代表无涂层区,此处激光吸收小,温升低。
试件1的金相检测结果
为了验证上述检测结果的准确性,对该涂层试件进行了金相分析。当涂层经打磨后,可以清晰地看到块状及气孔缺陷的存在。
试件1影像部位涂层与基体的结合情况
由金相剖面检测结果可看到点状影像部位无底层形貌,点状长度为0.75mm,且该部位面层涂层与基体存在分离现象;块状影像部位整个截面层涂层与基体之间均未见底层形貌,且该部位面层涂层与基体之间存在不连续的分离现象,块状影像部位水平方向长度约为26mm。
激光扫描热波无损检测技术采用激光扫描对试件进行热激励,产生的热波向试件内部传播,然后用红外热像仪采集试件表面热波信号。热波在试件内部传播时,由于三维热扩散作用,会逐渐发生衰减且扩散,从而使得缺陷尺寸测量结果偏大,偏差误差在2%~5%之间。所以,从金相检测的验证结果来看,激光扫描热波无损检测技术能对涂层缺陷进行可靠检测。
真实试件
某航空发动机的真实部件为一直径约150mm,宽度约30mm的环形金属件,基体为合金钢,外表面的涂层厚度为1mm。为了进行对比,分别制作了含分层缺陷和无缺陷的两个试件,外表看起来没有任何区别。
环形金属试件的光学图像
检测时,采集帧频为50Hz,采集时间为10s,激光扫描时间为6s,试件距离热像仪约为500mm。
环形金属试件热波检测结果
测量上图(a)所示缺陷水平方向的长度约为24.6mm,热波图像中可看到的一个红色区域为脱黏区域,说明此区域无缺陷涂层和基体材料结合差,热阻抗大,热波信号发生反射而反射回表面,使得该区域表面温度较高,属隔热性缺陷。
而上图(b)所示的无缺陷涂层试件的检测结果中,此时试件各点的热波在涂层内部正常传播,表面温度大体无差异。
缺陷试件的金相检测结果
为了确认上述热波检测结论的正确性,对这两个试件进行了金相解剖以验证试验结果。对缺陷试件的涂层进行打磨,可以看到一个方形块状缺陷的存在,形状与热波图像完全吻合。如上图所示,涂层与基体存在长度约23.7mm的分离,无底层涂层。
含缺陷涂层试件与无缺陷涂层试件的剖面形貌
对缺陷试件的该分层区域进行剖面形貌分析,可以清晰看到在涂层和基材结合部位有一个明显的裂隙,如上图(a)所示。同样对无缺陷试件进行了剖面形貌分析,如上图(b)所示,其涂层和基材结合部位界面光滑,没有任何裂隙存在。
结 论
采用激光扫描进行热激励,对多个航空发动机涂层试件进行红外热波检测,成功检测出涂层试件中的多种人工缺陷,包括块状缺陷与气孔,显示了该技术对涂层缺陷的检测能力。采用金相技术对试件进行了解剖分析,验证了激光扫描热波无损检测的结果,表明该技术可对航空发动机涂层缺陷进行可靠地检测。
免责声明:本网站所转载的文字、图片与视频资料版权归原创作者所有,如果涉及侵权,请第一时间联系本网删除。
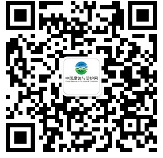
官方微信
《中国腐蚀与防护网电子期刊》征订启事
- 投稿联系:编辑部
- 电话:010-62316606-806
- 邮箱:fsfhzy666@163.com
- 中国腐蚀与防护网官方QQ群:140808414