编者按: 非晶合金(BMG)由于其独特的短程有序、长程无序的结构,具有高强度、高硬度、高耐磨耐蚀性等特点,被认为是极具工程应用前景的结构材料。然而由于非晶合金存在剪切局域化和应变软化这两个本质上的缺陷,严重制约着BMG作为先进结构材料在工程中的大规模应用。因此,开发室温塑韧性良好的BMG成为当前研究的热点。《Ti基非晶复合材料的强韧化机理》一文选择具有形状记忆效应与较强非晶形成能力的(Ti0.5Ni0.5)80Cu20合金,通过微量添加Fe、Ce、Zr元素,研究了微合金化对合金凝固组织中形状记忆晶相析出的变化规律的影响,分析了其室温力学性能与强韧化机理。本文的作者为兰州理工大学的赵燕春副教授。
1 实 验
采用水冷铜坩埚磁悬浮熔炼-铜模吸铸法在真空及高纯氩气保护条件下制备了直径3mm的(Ti0.5Ni0.48M0.02)80Cu20(M=Fe,Ce,Zr)合金,研究了Fe、Ce、Zr对合金凝固组织中形状记忆晶相析出的变化规律的影响,分析了该合金的室温力学行为与强韧化机理。
2 结果与讨论
2.1 (Ti0.5Ni0.48M0.02)80Cu20(M=Fe,Ce,Zr)合金XRD与力学性能分析
从图1与图2的可知,M=Fe,Ce合金铸态组织中B2相体积分数较多,而M=Zr合金铸态组织中B19‘相体积分数较多。合金内部在应力加载下发生B2-Ti(Ni,Cu)向B19'-Ti(Ni,Cu)的相转变(即TRIP效应),因此奥氏体相越多,对非晶基体的增强增韧越明显。另一方面,Fe元素在合金组元中与Ti、Ni的原子对混合热为负值(–17和–2),而Fe与Cu的原子对混合热为正(13),因此非晶基体中能够形成富Cu和富Fe相的原子团簇,即相分离,其中富Fe相结构的原子结合力较大,结构密堆性高,为硬相,而富Cu相为软相。软相的存在使非晶基体周围环境复杂,容易形成位错,这必然降低应力诱发马氏体相变时所需的形核阻力,使奥氏体发生向马氏体的相转变变得更加容易,TRIP效应容易进行。从而使得M=Fe的合金塑性最好,相比于M=Ce,Zr合金屈服强度最低。同时Ce与Zr元素添加都可稳定非晶基体组织,因而使得M=Ce合金综合力学性能最为优异,M=Zr合金屈服强度最高。
图3和表1为(Ti0.5Ni0.48M0.02)80Cu20(M=Fe,Ce,Zr)合金的室温压缩力学性能。较之单一的BMG合金,材料具有更为优异的综合力学性能,尤其在塑韧性方面。在合金体系中,M=Fe的合金塑韧性最好,塑性应变为13.1%,但屈服强度(980MPa)和断裂强度(2050MPa)较低;M=Ce时,合金具有最高的断裂强度(2645MPa),屈服强度达到1150MPa,并且塑性变形能力也达到12.2%;M=Zr时,合金的屈服强度最高(1300MPa),塑性最小(7.5%)。3种合金试样的断裂强度远高于屈服强度,没有出现应力诱发相变平台,以连续屈服和强烈的加工硬化为主要特征。
表1 (Ti0.5Ni0.48M0.02)80Cu20(M=Fe,Ce,Zr)合金的室温压缩力学性能
2.2 (Ti0.5Ni0.48M0.02)80Cu20(M=Fe,Ce,Zr)合金加工硬化行为分析
图4为(Ti0.5Ni0.48M0.02)80Cu20(M=Fe,Ce,Zr)合金试样的加工硬化速率与真应变关系。从图中可知,(Ti0.5Ni0.48M0.02)80Cu20(M=Fe,Ce,Zr)合金系中,M=Fe的合金加工硬化速率最大,M=Zr的合金加工硬化速率最小,并且加工硬化速率随着应变变化过程可以从加工硬化开始阶段大致分为加工硬化初始阶段、合金强韧化阶段、线性硬化阶段3个阶段。第I阶段为加工硬化初始阶段。第II阶段为合金强韧化的主要阶段,表现为加工硬化速率随着应变的增加开始逐渐下降。第III阶段为线性硬化阶段,表现为加工硬化速率随着应变的增加开始单调下降,加工硬化速率变化最慢。
图4 (Ti0.5Ni0.48M0.02)80Cu20(M=Fe,Ce,Zr)合金试样加工硬化速率-真应变曲线
图5为直径3mm(Ti0.5Ni0.48M0.02)80Cu20(M=Fe,Ce,Zr)合金试样的真应力-真应变曲线。对真应力-真应变方程两边取对数可得到Hollomon关系:lnσ=lnk+nlnε。
在双对数的坐标系下,曲线的斜率n为材料的平均加工硬化指数。由此得出M=Fe,Ce,Zr合金的平均加工硬化指数(n)分别为0.32、0.26和0.22。总体来看,M=Fe,Ce,Zr合金的平均加工硬化指数都较大,说明复合材料都有较强的加工硬化能力。M=Fe的合金平均加工硬化指数最大,材料的加工硬化能力最强,这与前述分析结果相符。
平均加工硬化指数n反映了材料开始屈服以后,继续变形时材料总体的应变硬化行为。并不能说明加工硬化每一阶段的硬化行为。而在加工硬化的每一阶段材料的硬化行为都不尽相同,因此,引入瞬时加工硬化指数来具体分析复合材料在加工硬化每一阶段的硬化行为,如图6所示。
由图6可知,M=Fe,Ce,Zr合金的瞬时加工硬化指数(n*)的变化规律为:n*(Fe)>n*(Ce)>n*(Zr)。总体来看,3种不同成分合金的瞬时加工硬化指数都是先增大后减小,其变化趋势可以分为3个阶段。第I阶段,随着真应变ε0从0%增加到2.3%左右,n*也随ε0的增加而快速增大。在n*-真应变关系曲线中,瞬时加工硬化指数反映了材料在每一瞬时的加工硬化能力,因此在图6中,这一阶段曲线的斜率越大、趋势越陡,复合材料的瞬时加工硬化指数越大,合金的加工硬化能力越强。图4中,此阶段与加工硬化速率随真应变变化的第I阶段一致。合金化元素的不同影响了合金组织内部相转变的难易和位错的生成,因此,与前述分析一致,M=Fe的合金加工硬化能力最大,这一阶段完成最快。在第II阶段,n*随ε0的逐渐增加而缓慢下降,复合材料的加工硬化能力逐渐减小,是合金完成强韧化的主要阶段,此阶段越长,合金的强韧化效果越明显。第III阶段,n*随ε0的逐渐增加而迅速下降,合金完成最后阶段硬化直至断裂。3种复合材料在屈服阶段之后的瞬时加工硬化指数随真应变变化趋势和加工硬化速率随真应变变化的3个阶段一一对应。合金在受压应力变形时,其内部发生的B2-Ti(Ni,Cu)→B19'-Ti(Ni,Cu)的相转变(TRIP效应)和位错增殖是合金产生加工硬化行为并完成强韧化的主要原因。
2.3 (Ti0.5Ni0.48M0.02)80Cu20(M=Fe,Ce,Zr)合金断口形貌分析
由图7可知,3种合金边缘断口均呈现为明显的脆断形貌组织。较之M=Fe的合金,M=Ce,Zr的合金断面更加平整光滑。这是由于Zr、Ce的存在使得边缘区域的非晶组织更加稳定,不易发生剪切滑移而产生塑性变形。在断裂中心区域,3种合金的断口形貌以脉络纹、韧窝形貌为主。较之M=Zr,Ce的合金,在断裂中心处M=Fe的合金脉络纹分布更加密集,并且合金断裂方向扩展延伸,占据了整个中心区域,而M=Ce的合金出现的韧窝形貌较为稀少且分布疏松,与脆性形貌交替相存。对于M=Zr的合金,中心处的塑性脉络纹形貌最为稀少,分布较M=Ce的合金疏松。因此M=Fe,Ce的合金塑性均优于M=Zr的合金,这与前述分析结果相符。
3 结 论
1) (Ti0.5Ni0.48M0.02)80Cu20(M=Fe,Ce,Zr)合金的铸态组织均为非晶+形状记忆晶相的复合结构,其中形状记忆晶相主要为B2-Ti(Ni,Cu)过冷奥氏体相和B19'-Ti(Ni,Cu)热诱发马氏体相。M=Fe,Ce合金的铸态组织中B2相析出体积分数较多。M=Zr合金的铸态组织中B19’相析出体积分数较多。
2) (Ti0.5Ni0.48M0.02)80Cu20(M=Fe,Ce,Zr)合金在室温压缩过程中均表现出优异的综合力学性能,其中以M=Ce合金综合性能最优,断裂强度,屈服强度,塑性应变分别达到2645MPa,1150MPa和12.2%。合金在受压应力断裂后,组织中奥氏体相体积分数减小,马氏体相体积分数增加,同时在屈服后均表现出强烈的加工硬化行为。合金内部在压应力作用下B2相向B19‘相转变是合金强韧化的主要动力。M=Fe合金加工硬化速率、平均加工硬化指数、瞬时加工硬化指数最大,加工硬化能力最强。M=Ce的合金次之,M=Zr合金最弱。
免责声明:本网站所转载的文字、图片与视频资料版权归原创作者所有,如果涉及侵权,请第一时间联系本网删除。
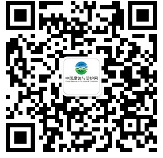
官方微信
《中国腐蚀与防护网电子期刊》征订启事
- 投稿联系:编辑部
- 电话:010-62313558-806
- 邮箱:fsfhzy666@163.com
- 中国腐蚀与防护网官方QQ群:140808414