A283GRC钢(ASTM)的综合力学性能优异、价格低廉,是应用广泛的工程结构材料[1, 2]。但是A283GRC钢的耐磨性较差,限制了在关键零部件摩擦副中的应用[3]。为此,人们采用表面工程技术在A283GRC钢表面制备高耐磨复合涂层,实现了传统材料和高性能材料的组合式应用,充分发挥了各种材料的使用潜能,提高了装备的使用寿命,降低了制造成本[4, 5]。
目前常用的表面工程技术,有渗碳、复合镀、气相沉积和激光处理等方法。材料渗碳后在表面形成了碳含量高的硬化层,具有良好的耐磨性。但是渗碳层的脆性较大,承受冲击能力弱,且渗碳层厚度薄,在渗碳过程中易变形,限制了使用范围[6]。复合镀技术,是在工件表面形成一层复合镀层。这种镀层的性能优异、界面结合好,但是镀液易对环境造成污染[7]。用气相沉积技术制备的复合膜致密、性能稳定,但是制备时需要真空环境,效率低而成本较高[8]。随着高功率激光器的发展,激光熔覆技术已经受到人们的青睐[9]。
激光熔覆技术是利用高能量密度激光束辐照熔覆层粉末和基板,形成界面冶金结合的熔覆层[10]。该技术的热源作用区域小、冷却快,可以实现精准定点强化,降低了原材料消耗,是一种绿色环保的表面强化技术[11]。因此,该方法广泛应用于航空航天、汽车工业、石油勘探和矿产机械强化等领域。目前熔覆层材料多为陶瓷(TiC、TiB2)增强金属基复合涂层,耐磨性良好,但是耐腐蚀性较差[11, 12]。因此,耐腐蚀性良好的金属间化合物涂层受到了人们的关注。Fe-Al金属间化合物具有良好的耐腐蚀性能,有望成为激光熔覆涂层的理想材料,但是耐磨性不高,降低了使用寿命[13]。陶瓷增强金属间化合物涂层兼有陶瓷的耐磨和金属间化物的耐腐蚀性,是激光熔覆涂层的理想材料之一[14-16]。本文以Fe-Al-Ti-C混合粉末为原料在A283GRC钢铁材料表面直接制备出原位TiC/FeAl复合涂层,研究其微观结构和耐磨性。
1 实验方法
实验用激光熔覆基板,是尺寸为100 mm×80 mm×10 mm的经正火处理的A283GRC钢,其化学成分列于表1。熔覆前对基板进行喷砂处理以除掉表面的氧化皮,粗化钢的表面,增加基板对激光的吸收。熔覆层材料选用Fe-Al-Ti-C混合粉末,其中Fe粉(纯度≥96.8%,200目)、Al粉(纯度≥99%,200目)、Ti粉(纯度≥99.9%,100目)、C粉(纯度≥99.9%,100目)。Ti粉、C粉的总质量分数为30%,摩尔比为1:1,Al粉与Fe粉摩尔比为3:1。
实验中使用型号为LDM-2500-60的半导体激光器,光斑直径为3 mm。用氩气同轴送粉,气流量为10 L/min。熔覆层为6道多层,试样的尺寸为70 mm×24 mm×10 mm,试验用激光功率为2.2 kW,熔覆层搭接率为40%,扫描速度5 mm/s。
用线切割法切取金相试样,然后进行金相研磨、抛光和金相腐蚀。金相腐蚀剂选用5%的硝酸酒精,样品在腐蚀液浸泡30-60 s后清洗、吹干。用BX41M-LED金相显微镜、Tescan VEGAII-LMH扫描电子显微镜(SEM)观察熔覆层的形貌,使用扫描电镜附带的能谱仪(EDS)和Max-2000 X射线衍射仪(XRD)分析涂层的物相组成,CuKα辐射,衍射束石墨单色器单色化,管压40 kV,管流100 mA。根据ISO6507标准[17]使用XHV-1000Z显微硬度计测试涂层的硬度,所加载荷为0.2 kg,加载时间为15 s。为了减小测量误差,测量硬度时在同一区域测量10次取其平均值。根据ASTM:G77-05(2010)标准使用M-2000型磨损试验机测定熔覆层的耐磨性,压力选用800 N,试样先预磨损5 min,然后持续磨损30 min后将试样取下进行超声清洗称重,计算磨损失重与原始重量的比值以表征其磨损率。
2 结果和讨论
2.1 微观结构
图1给出了激光熔覆TiC/FeAl复合涂层的宏观形貌,图2给出了涂层横截面的宏观形貌。可以看出,涂层主要由熔覆层、界面熔合区、热影响区、搭接区和基板构成,且各区域间结合良好,没有气孔、裂纹、夹杂等缺陷。在基板与熔覆层之间有一条细窄的熔合线,称为界面熔合区。界面熔合区清晰明显,且宽度较窄。其原因是,在高能量密度激光的瞬间作用下在基板表面快速形成熔池,熔池与母材之间元素含量的差异造成很大的浓度梯度,合金元素强烈扩散。在快速冷却过程中,作为传递热量的过渡层形成了一层化学成分既不同于基板又不同于熔覆层的过渡区域。熔合区的存在确保了涂层与基板形成良好的冶金结合,提高了界面结合强度。在基板和熔合区之间区域为热影响区,相邻两道熔覆层叠加的热影响区比非叠加区域宽。这主要与激光熔覆的热循环有关。上一道激光熔覆后基板的温度升高,相当于提高了下一道激光熔覆基板的初始温度,对基板进行了预热。随着基板初始温度升高,基板材料对激光的吸收率也逐渐增加。因此,在相同能量密度的激光作用下基板可以吸收更多的激光能量,基板表面的温度更高,使基板的热影响区域增大。
图1 熔覆层的宏观形貌
图3给出了涂层的微观结构。由图3可见,熔池界面附近的白色粗大FeAl树枝晶垂直于界面择优生长(图3a)。在高能量密度激光束的辐照下穿过激光束焦点附近的复合粉末吸收了激光大部分能量,产生了瞬间高温,发生原位反应,生成TiC/FeAl复合材料;高温熔融的原位产物沉积在基板表面,形成瞬间熔池。基板温度低,熔池温度高,在熔池和基板之间形成垂直于界面的巨大温度梯度。熔池液体沿垂直于界面的最大散热方向快速生长,形成了明显的树枝晶。该区域只能依靠基板本身的热传导散热,因此冷却速度较小,树枝晶生长较慢且粗大。沿着熔池深度方向从熔池底部到熔池中间,树枝晶渐渐转变为等轴晶(图3b, c),熔覆层顶部为晶粒细小的等轴晶。在熔池顶部,熔池大部分高于基板表面,熔池的热量既可以通过熔池内部的强对流散发又可通过周围空气辐射散热,熔池在三维方向上受到周围气体的均匀冷却[18]。另外,保护气体定向喷到熔池表面可实现熔池快速冷却,加快熔池顶部的凝固速度,因此熔池顶部形成了细小的等轴晶。熔池中部的熔体主要依靠对流散热,在三维方向上散热均匀,冷却速度小于熔池顶部,因此该区域生成晶粒稍大的等轴晶。
图2 熔覆层的横截面宏观形貌
图3 熔覆层微观结构 (a)界面熔合区 (b)熔池底部 (c)中部 (d)顶部涂层的微观结构
原位TiC越过熔池界面进入基板表层,涂层中TiC颗粒大部分存在FeAl晶粒内部,成为FeAl基体的形核中心,熔池顶部的TiC含量较多(图3d)。通过激光束时复合粉末吸收激光束的高密度能量,瞬间达到高温并熔化。同时,对应区域的基板表层产生微熔化,然后熔融的复合熔体沉积到温度较低基板表面,与基板表层微熔区域共同形成熔池。根据Fe-Al-Ti-C体系主要产物的吉布斯自由能变化曲线(图4),当温度高于400 K时TiC的生成吉布斯自由能明显比Al3Ti与Al4C3的低,Al4C3的最高,因此TiC增强体颗粒优先生成,然后生成FeAl相[19]。TiC的熔点高达3360 K,是涂层中熔点最高的相,因此在复合熔体的沉积过程中随着激光束的偏移熔体温度逐渐降低,先达到固态TiC颗粒增强液态FeAl半固态状态。半固态复合熔体沉积在基板表面时,在初始冲量和重力作用下固态的TiC颗粒穿过基板表面微熔层进入到基板表层,而处于液态的FeAl在表面张力的作用下没有进入基板表层(图3a)。TiC为面心立方结构,晶格常数a=0.4327nm,FeAl晶体结构为简单的CsCl结构,Fe作为α子晶格位于体心立方的顶角,Al作为β子晶格位于体心立方的中心,两个子晶格相互嵌套成一个完整的晶体结构,晶格常数a=0.2909 nm。TiC与FeAl的晶体结构不同,两者的晶格匹配需通过二维错配度进行准确表征。采用bramfitt的方法计算出TiC与FeAl二维点阵错配度δ=5.18%[20-21]。因此,当激光束偏离熔池区域后熔池温度逐渐降低,高熔点的TiC颗粒为FeAl熔体的凝固提供形核中心,实现了熔体的非均匀形核,最后分布在FeAl晶粒内部,细化了晶粒(图3c)。TiC颗粒在熔池中的运动机制有两种:一方面,表面张力梯度差引起的熔池表面的强制对流张力,以及熔池内部温度梯度产生的自然对流浮力,在两者共同作用下熔池内部形成对流环[22]。熔池底部的TiC颗粒受到基板的冷却作用使对流环对其影响较小,而熔池中部半固态复合熔体中的TiC颗粒随着对流环向熔池顶部移动,并在快速冷却条件下于顶部汇聚。另一方面,由于TiC的密度(4.93×103 kg·m-3)小于FeAl(6.72×103 kg·m-3),密度小的TiC易聚集在熔池顶部(图3d)。
图4Fe-Al-Ti-C体系中主要反应产物的吉布斯自由能随温度变化关系曲线
为了进一步确定熔覆涂层的相组成,对图3中A、B、C点,进行EDS点扫描,谱图如图5所示。柱状晶(A点)主要含有Fe、Al两种元素,原子含量百分比为94:6。由于该区域为界面附近的组织,主要由部分熔化的基板和熔覆层共同构成。熔覆时熔池底部局部熔化的基板垂直于基板择优生长定向凝固(图5a),因此该部分以α-Fe固溶体为主。黑色颗粒状相(B点)主要含有Ti、C元素,Ti的原子百分数为52.37%,C的原子百分数为47.63%,原子百分比接近1:1,该新相为原位合成TiC增强颗粒(图5b),与XRD (图6)结果一致;涂层中C点的主要元素组成为Fe、Al,其中Fe原子百分数为52.22%,Al的原子百分数为45.08%,原子百分比接近1:1(图5c),说明基体组织主要为金属间化合物FeAl相。XRD图谱显示,熔覆涂层中还存在Al、Fe、Ti单质。其原因是,激光能量的分布属于高斯分布,激光束中心的能量很高,周边的能量很低,当粉末通过激光束外围时粉末吸收的能量达不到反应所需的温度,该部分粉末之间没有发生原位反应。
图5激光熔覆制备TiC/FeAl复合涂层EDS能谱分析
图6 熔覆层的XRD图谱
2.2 显微硬度
图7给出了涂层的显微硬度。从图7可以看出,熔覆层的硬度最高,平均硬度为HV1896,熔池顶部的熔覆层硬度超过HV2000;在界面熔合区的平均硬度为HV1013,比熔覆层硬度明显下降;热影响区的硬度分布稳定,最高值与最低值相差不大,平均硬度为HV469;基板硬度为HV316,熔覆层的硬度约是基板的6倍。涂层硬度的梯形分布主要由其微观结构决定,熔覆层顶部的FeAl基体晶粒细小,且TiC颗粒增强体含量较高,因此该区域的硬度最高。沿着熔池的深度方向从涂层顶部到熔池底部,FeAl的晶粒尺寸逐渐增大,在接近于熔池底部的界面区域FeAl晶粒转变为晶粒较大的树枝晶,且TiC含量相对较少,局部熔化的基板对界面周围区域产生稀释作用,降低了该区域金属间化合物含量,增大了金属Fe的比例,因此界面区域涂层硬度明显降低。热影响区的显微组织,是固态基板在高温下快速冷却形成的。快速的冷却相当于淬火过程,因此该区域的硬度比基板的高。
图7 熔覆层熔池深度方向的显微硬度分布
2.3 耐磨性
图8给出了在相同磨损条件下基板和熔覆层的磨损率。本文用相对体积减少量的百分比表征磨损率,即磨损体积的减少量除以原始样品的体积再乘以百分之百。耐磨性与磨损率呈倒数关系,即磨损率越高耐磨性越差。从图8可以看出,基板的磨损率为0.53%,熔覆层的磨损率为0.01%,熔覆层的耐磨性比基板提高53倍,熔覆层的耐磨性远高于基板。这主要与涂层的微观结构有关,磨损试验前将涂层打磨使其具有一定的表面平整度,但磨去的只是涂层表面较薄的一部分。实验中与磨轮接触的是涂层的上部区域,熔覆层上部由颗粒细小的TiC陶瓷和FeAl金属间化合物构成,TiC颗粒作为FeAl的形核中心,实现了非均匀形核,细化了FeAl晶粒。同时,TiC颗粒具有高的耐磨性,增加了涂层的耐磨性,所以熔覆层的耐磨性远高于基板。图9给出了熔覆层的磨损形貌,可见基板表面有细长的划痕和显微切削而造成的不规则塑性撕裂口(图9a),摩擦面呈典型的磨粒磨损形貌。其原因是,对磨副具有较高的硬度,磨轮上密布的硬质点反复刮擦基板表面,造成大量划痕,形成磨粒磨损。图9b给出了熔覆层磨损表面形貌,可见磨损面呈典型的磨粒磨损沟痕,磨损面较平整,且摩擦沟痕深度和宽度都明显减小,没有发现磨屑粘着和塑性断裂现象,呈现典型的磨粒磨损特征。熔覆层由原位合成的FeAl金属间化合物基体和TiC陶瓷增强体组成,涂层具有很高的硬度。在摩擦过程中对磨副很难压入高硬度的熔覆层中,只能通过划擦的方式作用在熔覆层表面。原位生成的TiC增强颗粒与FeAl基体界面结合强度高,且可作为强化相对基体产生钉扎强化作用,大大提高熔覆层的抗微切削能力,因此磨损面摩擦痕较小,熔覆层耐磨性能好。
图8基板和熔覆层的磨损率
图9 涂层磨损表面形貌
3 结论
采用激光熔覆法制备的TiCp/FeAl原位复合涂层,沿着熔池深度方向从熔池底部到熔池顶部FeAl基体从树枝晶渐渐转变为细小的等轴晶。原位TiC越过熔池界面进入基板表层,大部分TiC颗粒存在FeAl晶粒内部,熔池顶部的TiC含量较多。沿着熔池的深度方向从涂层顶部到基板,涂层硬度呈梯形分布,熔池顶部涂层硬度最高,涂层硬度是基板6倍,涂层的耐磨性是基板的53倍。TiCp/FeAl原位复合涂层的磨损机理,为典型的磨粒磨损。
免责声明:本网站所转载的文字、图片与视频资料版权归原创作者所有,如果涉及侵权,请第一时间联系本网删除。
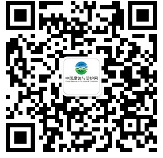
官方微信
《中国腐蚀与防护网电子期刊》征订启事
- 投稿联系:编辑部
- 电话:010-62313558-806
- 邮箱:fsfhzy666@163.com
- 中国腐蚀与防护网官方QQ群:140808414