深海环境下金属材料的主要防护手段就是有机涂层保护[1,2]。有机涂层在服役环境下随服役时间延长而逐步失效,但这些失效行为难以被及时发现,从而导致涂层下服役金属材料发生严重腐蚀问题,影响深海环境下服役金属构件的使用寿命及设备的安全性。为及时发现这些腐蚀问题,开发原位测试技术显得尤为必要,因此对深海环境下服役的有机涂层进行原位电化学评价是目前的热点课题之一。本课题组[3-6]前期对深海环境下有机涂层的失效问题,尤其是失效机制开展了大量的研究。结果表明:在深海压力作用下,海水溶液首先会快速渗入涂层内部,深海的交变压力通过“拉拔”作用来破坏体系中的涂层/金属界面的结构,导致涂层从基体表面快速剥离;其次,反复的压力交变循环致使涂层中填料/基料树脂界面发生开裂,水等腐蚀介质由开裂处快速向涂层内部渗透,破坏涂层致密性,最终导致大量水在金属/涂层界面水平扩展,引发基体金属腐蚀,致使有机防护涂层提前失效。可见,在整个过程中,金属/涂层界面以及填料/基料树脂界面是涂层体系在深海环境下服役的薄弱环节,它们直接影响着涂层的防护性能。因此,采用电化学方法获取金属与有机涂层体系的界面状态随服役时间的演化规律,可以实现对涂层服役性能的评价,其中电化学阻抗谱 (EIS) 测试技术就是有效的电化学测试方法之一[7,8]。
然而,实验室内的传统电化学测试装置却无法直接应用在现场检测中。这主要是因为,一方面,传统的电化学测量体系需设置电解池,引入外置电极及溶液等,而这明显不符合深海环境下现场应用的需求;另一方面,涂料的较大厚度严重影响了金属基体电化学信号的准确采集。一般应用于海洋设施通用部位的重防腐涂料,其防护期效应至少达到10 a;对于重点部位则要求防护期效达到15 a以上,因此施加的防腐蚀涂层的厚度则应达到300 μm以上[9]。此时,涂层下金属基体反馈的电化学信号将变得非常微弱,给电化学信息的采集带来很大困难。因此,如果要实现深海环境下有机涂层性能的原位电化学准确评价,就需要针对性地开展更有效的原位测试装置设计的研究。
近年来,研究人员应用微电极技术开展了许多原位电化学测量或局部电化学反应的研究。Simpson等[10]采用电子束沉积法将贵金属沉积在涂层表面形成薄片状微电极。这种微电极制备方法相对复杂,且微电极本身容易受到外界环境的破坏,在测量较厚涂层下的金属腐蚀时灵敏度较低。Courioni等[11]采用微阵列电极研究了不同材料间的电偶电流对电化学噪声信号的影响,虽然装置稳定,但仍未解决需要外置装备辅助测量的问题。还有一些学者采用局部pH值或电流探针的测试微电极[12,13]来测量涂层体系的电化学参数,但这些研究并没有针对涂层体系的防护性能做出有效评价。总之,涂层研究现有的微电极方法无法适用于深海环境的原位测量,同时针对深海环境下涂层原位电化学测量装置的研究也鲜有报道。
为了解决深海环境下涂层原位电化学测量的问题,本文首先设计了一种圆环状预埋微电极。微电极预先植入有机涂层内部,避免了采用外置电极及厚涂层信号检测困难的问题。圆环状的传感器设计方案使系统电位分布均匀,保证了电化学测试结果的准确性。微电极的几何尺寸微小,不会对涂层的防护性能产生明显影响。其次,基于研制的预埋微电极,设计了相应的EIS原位测试装置。最后,通过交变压力加速实验及与传统测量方式结果对比等方法检验了微电极原位测试的准确性和可靠性。
1 实验方法
1.1 样品制备及电化学测试
采用环氧清漆涂层体系作为研究对象,环氧树脂、固化剂及有机溶剂的质量比为1∶0.8∶0.4。制备过程为:将溶剂二甲苯加入环氧树脂E-44并磁力搅拌0.5 h,待E-44充分溶解后加入固化剂TY-650继续搅拌0.5 h,最后在常温环境中静置0.5 h令其充分熟化,以待涂刷。金属基体材料为10Ni5CrMoV低合金高强度钢,其主要化学成分 (质量分数,%) 为:Ni 4.67,Cr 0.60,Mo 0.46,V 0.065,Mn 0.54,C 0.076,Fe余量。基体尺寸为40 mm×40 mm×2 mm。涂层/金属电极工作面积为16 cm2,涂层平均厚度为(200±10) µm。
通过Autolab PGSTAT302型电化学工作站进行EIS测量。采用传统的三电极体系,以涂层/金属电极试样作为工作电极,Pt电极作为辅助电极 (CE),固态Ag/AgCl电极为参比电极 (RE)。EIS测试在开路电位下进行,待开路电位稳定后开始测量。测试频率范围为105~10-2 Hz。浸泡初期施加50 mV (rms) 振幅的正弦扰动以保证一定的信噪比,后期振幅调整为20 mV (rms)。文中涉及的交变压力实验均在实验室自制的深海环境模拟装置中进行[4]。选取3组不同幅度的交变压力条件进行实验室加速实验,分别为:0.1~6.0 MPa,0.1~8.0 MPa以及 0.1~10.0 MPa。每一个交变周期包括12 h的常压阶段和12 h的高静水压阶段,每组实验至少持续10个周期共240 h。
1.2 预埋微电极
为了避免在原位测量中使用外置电极,采用了分层刷涂涂层的方法将微电极预先植入涂层内部,使整个环氧清漆分为内、外两层,微电极则水平置于涂层内层和外层之间,其示意图如图1所示。首先,将直径为50 μm的铂丝制成圆环状的微电极,以保证电势的均匀分布。然后涂覆一层环氧清漆于基体金属表面,待其接近完全固化后将微电极固定于涂层表面。为了使微电极与涂层表面完全贴合并黏附牢固,配制少量的环氧清漆并涂覆于二者之间。接着在整个试样表面刷涂外层清漆并完全覆盖微电极,两层清漆的干膜厚度均为 (100±10) μm。为了与外部的电化学测量仪器连接,微电极还需连接一段铂丝制成的电极引线,引线接头的一端位于涂层内部,另一端延伸至涂层外并与Cu导线相连接,其连接处采用环氧树脂封装,保护接口并与外界环境绝缘。最后将整个试样在40 ℃条件下固化4 h,60 ℃固化20 h,再在室温条件下 (25 ℃,RH 30%) 放置7 d,以确保涂料的固化完全及溶剂的完全挥发。
图1 装有预埋微电极的涂层/金属电极试样示意图
2 结果与讨论
2.1 针对电化学阻抗谱测试的原位测试装置设计
为了验证上述预埋微电极的有效性,将制成的微电极试样直接用于EIS的测试。根据阻抗测量原理,将直径为2 cm的圆环状铂微电极作为参比电极,基体金属作为工作电极,另加一个外置的Pt电极作为辅助电极。同时制备一组普通的传统三电极装置在相同条件下进行阻抗测试。表1为常规的及预埋微电极的涂层/金属电极试样在浸泡不同时间后所测得的低频阻抗模值|Z |0.01 Hz。可以看出,装有预埋微电极的清漆涂层试样与传统装置的试样测试结果非常接近,说明此涂层体系中采用电位较为稳定的Pt微电极作为微参比电极是可行的。
然而,这种预埋微电极试样并没有完全避免外置电极的使用,尚不能在现场进行原位的EIS测量。为此,本文首先考虑采用两电极体系进行EIS测试,即金属基体作为工作电极,预埋的Pt微电极同时作为辅助和参比电极。事实上,当工作电极的面积较小时,极化回路中的电流不能引起辅助电极的极化,因此辅助电极的电位在测量中可保持稳定,此时可将辅助电极作为测量电路中的电位基准,即参比电极。电沉积、电致变色等研究常常采用两电极体系,许多特殊环境下的电化学阻抗测量也是采用两电极体系完成的[14,15]。但是,本实验采用两电极方法并没有获得正常、有效的阻抗数据。主要的原因可能是微电极的面积微小,作为辅助电极时其自身电位在回路中并不能保持稳定,微电极同时做参比、辅助电极的方法不可行。
为了将微电极技术应用于EIS的测试,本实验对装置模型进行了改进,设计了适用于EIS的双微电极装置,如图2所示。两个圆环状Pt微电极分别作为RE与CE预先植入有机涂层内部并处于同一平面,使其不易受到交变压力环境的影响。微电极之间相对距离比较接近但各自的引线部分避免了直接接触,测量时金属基体作为工作电极。
图2 适用于电化学阻抗测试的双微电极装置示意图
为验证双微电极装置测试的准确性,待其阻抗测量完毕后即置换外置参比和辅助电极再一次进行测量。这种传统测量装置与双微电极装置的EIS结果如图3所示。图3a为浸泡2 h的Nyquist图,其中传统电极试样所测得的曲线呈单容抗弧特征,而微电极试样的结果为近乎直线且无法采用有效的等效电路进行拟合,二者有着明显的差别;浸泡26 h后 (图3b),二者的谱图形状逐渐接近,此时采用具有两个时间常数的等效电路可以得到较好的拟合结果;浸泡到第136 h (图3c),两种电极试样的测试结果均又呈现为单容抗的特征,微电极试样的容抗弧半径较小,考虑到坐标比例的关系,二者结果的差别并不明显。两种电极试样测试的低频阻抗模值|Z |0.01 Hz拟合结果见表2。其中微电极试样浸泡2 h的数据因没有拟合而无法获得具体数值。通过分析可知,作为参比电极的微电极埋在涂层内部,当没有水渗透到达其表面时处于绝缘状态,此时测得的阻抗数据与真实结果偏差较大。以此特征可用来判断水向涂层内渗透的程度。随浸泡时间延长,水进入涂层内部,此时微电极试样的测量阻抗模值出现明显信息,并且结果与传统试样的测试结果相吻合,说明采用双微电极试样可以获得准确的EIS结果。
图3 通过传统测量方式与双微电极试样测试的浸泡不同时间涂层的EIS
2.2 交变压力环境下阻抗微电极装置的可靠性
前期研究[3-5]结果表明,深海交变压力能够使有机涂层快速失效。随着交变压力幅度的增大,涂层失效的速度加快,且不同交变压力下涂层的失效形式不发生改变。因此,交变压力是深海环境下对有机涂层防护性能影响最为显著的环境因素。针对这一深海环境的特点,以交变压力为主要变量的实验室加速实验可对有机涂层服役性能进行快速、有效的评价。因此,为了验证上述研制的涂层微电极装置应用于阻抗测试的可靠性,在一系列不同强度的交变压力加速实验下进行了涂层的EIS测试。图4为各压力加速实验下微电极装置测得的涂层阻抗模值结果。可以看出,0.1~3.5 MPa交变压力下,涂层的阻抗模值随浸泡时间延长而逐渐下降,浸泡240 h后|Z |从1010 Ωcm2以下降到约3×108 Ωcm2。0.1~6.0 MPa条件下,|Z |值在相同浸泡时间内下降到1×108 Ωcm2。0.1~8.1和0.1~10.0 MPa下,|Z |值分别下降到107和106数量级。结果表明,相同时间内交变压力幅值越大,涂层防护性能下降越明显。从图5中可以看出,交变压力幅值越大,基体金属腐蚀越明显。因此,测试的阻抗模值变化趋势与加速实验后金属基体的宏观表面形貌变化趋势相一致。加速实验下的EIS测试结果稳定,与前期的研究结果吻合,在量值上与前期测试结果也相同[4-6],这表明新研制的阻抗微电极测试装置不仅在普通水溶液中,而且在深海环境下,尤其是压力交变环境下,可以准确、可靠的进行原位电化学阻抗测试,其具有良好的可靠性。
图5 不同幅值交变压力加速实验240 h后金属基体的宏观表面形貌
3 结论
(1) 设计了一种预先植入涂层内部的圆环状Pt微电极,解决了原位测试电极在使用过程中外置电极不易安装以及有机涂层本身厚度对电化学测试信号的影响等缺点。
(2) 根据电化学阻抗谱的测量原理设计了双微电极装置,采用两个Pt微电极分别作为参比电极和辅助电极。其阻抗测量结果与传统测量装置结果有较好的一致性,证明了微电极装置测试的准确性。
(3) 深海交变压力加速实验下,预埋微电极装置测得的涂层阻抗模值随浸泡时间延长而逐渐下降;相同时间内交变压力幅值越大,涂层防护性能下降越明显。测试结果与传统装置测试结果一致,证明了预埋微电极在深海环境下应用的可靠性。
免责声明:本网站所转载的文字、图片与视频资料版权归原创作者所有,如果涉及侵权,请第一时间联系本网删除。
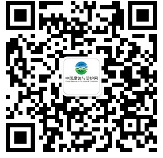
官方微信
《中国腐蚀与防护网电子期刊》征订启事
- 投稿联系:编辑部
- 电话:010-62313558-806
- 邮箱:fsfhzy666@163.com
- 中国腐蚀与防护网官方QQ群:140808414