作为航空航天装备的关键部件,航空发动机是飞机的“心脏”,其性能的好坏直接影响着飞机的性能。而影响航空发动机质量的关键因素之一就是叶片的质量。
航空发动机叶片按其在发动机上的部位分为风扇叶片、压气机叶片和涡轮叶片;按功能分为导向叶片和工作叶片,如下图所示:
图1 航空发动机的导向叶片与工作叶片外观
航空发动机叶片的主要作用是将燃气的热能转化为旋转的机械动能,工作时要承受交变拉应力、扭转应力的作用,以及机械磨损、热腐蚀的损害,极容易产生裂纹缺陷。叶片裂纹是危害飞行安全的重要因素,在大应力作用下裂纹扩展速度很快,即使是微小裂纹也易扩展成大裂纹从而影响飞机的飞行安全。
准确地检测航空发动机叶片结构的完整性及其状态,及时、可靠地发现叶片裂纹并预防危害,提高发动机工作的安全性,已成为航空无损检测领域的一个研究热点。
目前,针对航空发动机叶片裂纹,常用的无损检测技术有内窥检测,以及磁粉、渗透、射线、涡流检测等方法。其中内窥检测是叶片表面裂纹外场检测中应用较广的一项技术,但该技术依赖人工经验,检测周期长,操作过程复杂,同时叶片表面通常要进行喷涂处理,金属基体表面就变成了次表面,从而给内窥检测带来较大的困难。有报道采用内窥镜涡流集成化检测,结合内窥镜和涡流检测技术的优势,实现了对航空发动机叶片缺陷的检测。由于航空发动机叶片属于曲面结构零件,传统的无损检测方法对复杂曲面结构缺陷的检测都有各自的局限性。
超声热波成像技术利用红外热像仪采集试件表面热量并分析热量的变化情况来进行检测,因而对试件曲面结构没有要求,可以检测复杂曲面结构的缺陷。国内,装甲兵工程学院、中国空气动力研究与发展中心、火箭军工程大学、首都师范大学等科研院所与高校的研究人员对超声红外热像技术进行了深入研究,在理论研究、数据仿真、生热特性、裂纹识别、系统设计、参数调节等方面获得了丰硕的研究成果。西方先进工业国家已成功地将超声红外热像技术应用于航天航空领域的关键金属部件的检测中,包括航空发动机叶片裂纹的缺陷检测。
今天我们来介绍一下中国南方航空工业有限公司和南京诺威尔光电系统有限公司的研究人员采用超声热波成像技术对航空发动机叶片裂纹进行检测的成果。
1 超声红外热像技术
超声红外热像技术又称为超声红外热成像技术,结合了超声技术和热成像技术的特点,属于主动热激励红外成像技术。
与光激励热波成像技术相比,超声热波成像技术属于机械热激励,其特点在于仅对试件浅表面或者内部裂纹缺陷加热,对无裂纹的正常区域不加热,即属于选择性加热。有裂纹缺陷区域和正常区域的红外图像对比度更高,有利于裂纹缺陷的识别和判定,缺陷的检出可靠性增加。
2 技术方案
图2 超声热波成像检测系统框图
超声热波成像检测系统主要由超声激励装置、超声波发生器、红外热像仪、计算机等组成。其中,超声波发生器包括激励电源,超声激励装置包括激励头、换能器、变幅杆等。计算机主要用于超声激励控制和红外图像同步采集以及后期的红外图像处理。
3 系统集成
超声热波成像系统不仅要能改变热红外像仪采集位置与角度,而且还要能较好地固定被测试件。因而红外热像仪安装在一个可以调节角度与位置的平台上,便于采集红外图像;超声激励系统放置在平台底座上,可更好地旋转与固定试件,底座上可对工件进行一定的夹持,防止测试时的移动;同时需要配备压力传感器,以实时测量超声激励头与试件之间的预紧力,合适的预紧力有助于提升超声激励头与试件的耦合效率。计算机主要用于系统控制、红外图像采集以及后期红外图像处理。
超声热波成像设备型号为Acou Therm EB250;系统超声激励功率为1000W,激励频率为20kHz,单次激励时间为0.1~10s可调;红外热像仪为制冷型热像仪,探测波段为3~5μm,分辨率为320×256像素/640×512像素,等效噪声温差小于20mK,采集帧频为60Hz。
图3 超声热波成像设备外观
4 试验结果
采用Acou Therm EB250设备对航空发动机叶片进行裂纹检测,红外热像仪分辨率为320×256像素,超声激励时间选为1s。试验用的试件包括导向叶片1块和工作叶片2块(长度为75mm的短工作叶片1和长度为110mm的长工作叶片2)。
检测过程中,采集一张激励前的背景图像和激励后的红外图像,以便于裂纹缺陷的判断;要保证超声波的有效耦合,需要有恒定的预紧力,通过多次试验,确定预紧力约为200N时,超声耦合到试件中的效率最高,试件中的超声能量达到最大值,裂纹处温升最高。
图4 导向叶片的光学图像与超声激励前、后的红外图像
图5 工作叶片1的光学图像与超声激励前、后的红外图像
图6 工作叶片2的光学图像与超声激励前、后的红外图像
叶片中的裂纹处于表面或浅表面位置,属于细微裂纹,长度约为0.5~1.0mm,不属于长条形裂纹。超声激励后,裂纹处温度升高,在超声激励时间内裂纹位置处的温度持续升高且热量向周围扩散,从而形成亮光斑区域,实际裂纹尺寸比亮光斑区域要小得多,图中红色虚线圈中所示位置为裂纹位置。
对超声激励前后红外图像采用背景差分法进行分析,可以很好地识别出裂纹位置。在实际检测过程中,预紧力大小和超声激励位置对检测结果的影响比较大,需要通过多次试验来确定预紧力的大小和超声激励位置;超声激励头与工件接触时,如果耦合不好则超声波不能有效传递,同时对一些表面有要求的工件直接接触可能造成损伤,所以需要在超声激励头与工件之间使用耦合材料,这些材料需要有一定的柔性,以及很强的韧性。
结语
采用超声红外热像技术对航空发动机叶片裂纹进行检测,超声激励仅对裂纹处产生加热,从而实现对航空发动机叶片裂纹的检测。采用自主研发的超声红外热像系统对导向叶片和工作叶片进行了裂纹检测,成功检测出导向叶片和工作叶片试件中的细微裂纹(长度为0.5~1.0mm)。
作者:苏清风1,习小文1,袁雅妮1,江海军2,陈力2,魏益兵2
(1.中国南方航空工业有限公司;2.南京诺威尔光电系统有限公司)
苏清风,研究员级高工,主要从事无损检测技术研究工作。
通信作者:江海军
来源:《无损检测》2019年4期
免责声明:本网站所转载的文字、图片与视频资料版权归原创作者所有,如果涉及侵权,请第一时间联系本网删除。
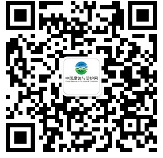
官方微信
《中国腐蚀与防护网电子期刊》征订启事
- 投稿联系:编辑部
- 电话:010-62313558-806
- 邮箱:fsfhzy666@163.com
- 中国腐蚀与防护网官方QQ群:140808414