1 引言
伴随着高速动车组综合技术性能的提高,对列车的美观性、防腐性也提出了更高的要求,涂料体系的性能将迎接新的挑战。目前高速动车组的涂装多为国外公司的涂料,其成功经验是基于特定的运营环境,由于国内运行区间的温湿跨度大,环境、气候条件复杂,为了适应国内高速动车组发展的需要,与之相配套的高性能涂料须尽快技术自主。高速动车组涂料体系除了保证与铝合金良好的附着力和防腐性外,其硬度、光泽、耐介质性、防污性、装饰性、高速下的减震和耐候性必须具有优于常规涂料的性能,而涂料的耐风沙、耐污染和修补性能将接受更严峻的考验。
2 涂料体系的设计
涂料体系:环保环氧防腐底漆+聚氨酯中涂漆+聚氨酯面漆
2.1 环保环氧防腐底漆
2.1.1 主要成膜物
动车组在高速行驶中,所处环境温度在短时间内发生急剧变化,防腐底漆必须具有与底材更好的附着力和韧性,否则温度变化引起的底材热胀冷缩将使涂层韧性变差,发生脆化或出现裂纹,最终导致涂层脱落和剥离,失去防腐作用。环氧防腐底漆通常采用采用双组分环氧体系,广泛应用于飞机、列车、工程机械等重防腐领域。主剂A采用两种双酚A类环氧树脂为主要成膜物,加入带有脂肪直链的活性稀释剂以提高环氧底漆的韧性;B组分为采用进口腰果壳提取的酚醛改性胺环氧固化剂。这类固化剂不但固化速度快,防腐性能也明显优于常用的聚酰胺类环氧固化剂。
环氧防腐类漆的漆膜固化时体积收缩小,因此与各种基材的附着力优异,但存在漆膜韧性差、易脆等缺点。开发一种具有一定韧性、耐冲击性能优异的环保环氧防腐底漆,是底漆需要解决的另一技术关键。采用添加带有直链碳链的活性稀释剂和德固萨LTW附着力促进剂聚酯树脂,以解决漆膜易脆问题。通过试验,确定出添加剂的最佳用量。
本次研制的防腐底漆在气候急剧变化的环境条件下也能够保持对底材良好的附着力和韧性,从而为底材提供了良好的防护性能。
采用同一树脂体系,固化剂不同,添加活性稀释剂不同,对比试验结果见表1。
表1数据表明:加入活性稀释剂、附着力促进剂后,耐冲击性能、硬度明显提高;另外,腰果壳改性酚醛胺固化剂的干燥速度明显快于300#聚酰胺固化剂。
2.1.2 防锈颜填料
锌黄、铬黄、锶铬黄等作为其防锈颜料来提高防腐性能。金属铬对人体有害,尤其是六价铬具有致癌性。底漆中含有铬等重金属颜料会在涂料的制备、施工以及成膜后的使用中对施工人员造成严重危害,而对环境的危害甚至是永久性的。为使环氧底漆体系达到环保标准,即不含铬等重金属,又能达到防腐性能要求,通过反复试验、耐盐雾检测等筛选出的复合金属络合物防锈颜料性能完全可以替代含铬金属防锈颜料。
树脂、固化剂、活性稀释剂等成膜物相同,颜填料不同进行对比试验,试验结果见表2。
表2的数据表明:采用不含铬金属的防锈颜料完全可替代含铬防锈颜料制备的防腐底漆。
2.2 聚氨酯中涂漆
中涂漆作为腻子和面漆的过渡层,它必须与腻子、面漆均具有良好的层间附着力,并具有易打磨性。为了满足体系抗冲击性能要求,中涂漆的主剂A中以羟基丙烯酸树脂为主要树脂,添加一定量带有轻微支链的聚酯树脂,增加漆膜的柔韧性,固化剂采用Bayer公司线性多异氰酸酯缩二脲即DesmodurN75,主剂A:固化剂B=4:1(质量比),性能对比试验结果见表3。
表3的数据表明:加入轻微支链聚酯树脂的聚氨酯中涂漆柔韧性明显提高,能够通过50cm耐冲击测试。
2.3 聚氨酯面漆
2.3.1 主要成膜确定
聚氨酯面漆作为涂层体系最上层漆是装饰性、防护性最关键的一层,采用双组份丙烯酸聚氨酯路线。主剂A选用综合性能好的羟基丙烯酸树脂,加入一定量与丙烯酸相容性好的柔性聚酯树脂以提高漆膜的韧性;此外为提高漆膜的耐候性,加入了一定量的氟碳树脂。为满足产品最终的综合性能,固化剂组份选用两种脂肪族聚异氰酸酯,经多次试验最终确定了两种固化剂的最佳用量,施工配比:主剂A:固化剂B=4:1。
2.3.2 耐磨性
高速列车运行时速为(200~400)Km/h,运行区间跨度广,温度、湿度等环境因素复杂,部分地区风沙污染严重,需要考虑高速运行时漆膜的耐磨强度。这不仅仅是提高漆膜硬度的问题,涂料体系必须要有足够的韧性。高速列车在隧道入口和出口处,由于气压变化而导致车辆形变,因此研制的涂料必须要适应这一变化。面漆配方设计时软、硬树脂合理搭配是基础,固化剂的筛选也是保证面漆质量的关键技术之一。此外助剂作用也是不可忽视的,加入含硅类流平剂,不但可提高漆膜流平性能、增加光泽,还能增加漆膜表面的光滑性,提高了漆膜抗划伤性能。
进行以下一组试验对比,(1~3)#羟基组分中:1#只含有羟基丙烯酸树脂,2#、3#加入与羟基丙烯酸树脂相容性好的聚酯树脂;固化剂都采用拜耳脂肪族聚异氰酸酯固化剂,即DesmodurN3390BA。1#、2#加入丙烯酸类流平剂,3#加入了带有硅类的流平剂。其他相同。
从表4可以看到2#、3#加入带有轻微支化度的聚酯树脂明显提高了漆膜的抗冲击性能和光泽;加入含有机硅类的流平剂,不但提高了漆膜的耐磨性,光泽也提高了。
2.3.3 耐候性及综合性能
聚氨酯面漆除了要满足高速列车在高速行驶中的耐磨、耐形变外,耐候性能也是保证面漆不被大气腐蚀破坏的一个重要指标。羟基组分(主剂A)中加入聚酯提高了漆膜的韧性和光泽,但聚酯树脂中的酯键在大气环境下易断裂,因此耐候性也相应降低了。为了弥补这一缺陷,在羟基组分的树脂中,添加与体系相容性好的氟碳树脂以及少量的紫外光吸收剂和光稳定剂,通过试验确定了其用量,试验结果对比见表5。
在这组实验中,1#和2#羟基丙烯酸树脂、聚酯、颜填料、助剂、固化剂相同,只是1#主剂A中未加氟碳树脂,2#加氟碳树脂。
从表5可以看到,在其他性能保持的同时,加入氟碳树脂的聚氨酯面漆耐候性能有显着提高。为达到较好的耐磨性、耐候性,以及优异的物理机械性和耐化学性等综合性能,在双组份配比中,高的交联密度是必要的,不同NCO/OH的当量比试验对比见表6。
从表6可见,随着NCO/OH的增大,交联密度增大,涂层硬度增大,耐腐蚀性提高;若NCO/OH大于1.2,在潮湿空气中提供大量的交联点,使漆膜固化时产生的二氧化碳较多,引起涂层表面起泡,脆性提高,耐冲击性变差,层间附着力降低。反之NCO/OH小于等于1,-NCO基团减少,干性变差,硬度降低,耐腐蚀性变差,层间附着力也降低。因此确定聚氨酯面漆的NCO/OH当量比为1.2。
2.3.4 助剂筛选
面漆是高速列车涂料中对装饰作用要求最高的涂层,而助剂是帮助油漆达到预期装饰目的重要因素。流平剂的加入可使漆膜表面提高光滑度、平整度,减少橘皮、缩孔等现象。聚氨酯涂料易产生气泡,消泡剂是必选助剂,含硅类消泡剂消泡效果明显,但易产生波纹影响漆膜外观,选择丙烯酸类消泡剂可避免此类弊病。防沉剂主要解决面漆中颜料沉淀问题,尤其是钛白粉易产生沉淀,沉淀剂选择不好,会影响面漆的光泽。因此需要选择既不影响光泽,又能防止颜料沉淀的防沉剂。分散剂帮助颜填料更好的分散,使涂料达到长期储存,提高涂膜外观等性能指标[3]。
2.3.5 溶剂筛选
采用混合溶剂体系,快、中、慢混合溶剂合理搭配以保证漆膜在干燥过程中的流平性。为确保人身健康安全,涂料用溶剂必须是无毒或低毒。在常用的溶剂中,乙二醇乙醚醋酸酯(CAC)虽然溶解能力强,挥发适中,但其具有生育致畸的负面作用。因此面漆采用丙二醇甲醚醋酸酯替代CAC,最终确定二甲苯:丙二醇甲醚醋酸酯:醋酸丁酯3:2:2混合比例。
3 涂料体系应用
3.1 涂装环境
涂装环境直接影响涂装质量,为保证涂装施工的温度、湿度、清洁度,所有的喷涂均在喷烘漆房内进行,室内和工件的温度不低于18°C,相对湿度不应大于75%。喷漆工作区域采用上送风、下排风形式,通过送风系统的加热、去湿和过滤得到干净的空气,保证室内有适宜的温、湿度,同时在车体周围形成层流空气,成包裹状,将过喷漆雾下压,避免在被涂表面形成小的颗粒。待喷涂工作结束以后,漆房进行全室送风,送风温度为(60~70)℃。
3.2 表面处理
涂料附着在基材表面主要依靠涂料中的极性分子与底材表面分子间的相互吸引。车体在喷砂处理后,提高了基材表面粗糙度和表面积。随着粗糙度和表面积的增大,单位面积上的涂层与基材表面的引力也成倍增大,同时还为涂层附着提供了合适的表面形状,增加了机械齿合作用,有利于提高涂层附着力;涂层在固化过程中会产生很大的内应力,粗糙度的存在可以有效消除涂层中的应力集中,防止涂层开裂;表面粗糙度的存在可以支承一部分涂料的质量,有利于消除流挂现象,对于垂直涂装的表面,作用尤为明显。但表面如果过于粗糙,也会带来不利影响。与光滑表面相比,使用相同的涂料量,其涂层厚度降低,尤其是在波峰处,涂层厚度往往不足,造成涂层过早破坏。此外,粗糙度过大还会在涂装时截留空气,造成涂层过早起泡、脱落。所以粗糙度直接影响涂层与底材的附着力和涂层厚度分布。选用(24~40)目棕刚玉进行喷砂处理,粗糙度范围为(6.5~20)μm。
3.3 涂料喷涂
3.3.1 底漆
高压无气喷涂效率高、漆雾飞散少,涂料中不混有压缩空气、油水等杂质,被喷涂的涂料渗透性强,一次喷涂可得到较厚的漆膜[4]。底漆喷涂要求一次成膜厚,因此采用40:1的高压无气喷涂机喷涂工艺,涂料粘度控制在(40~50)s,干膜厚度达到60μm以上。
3.3.2 中涂漆
中涂漆要求成膜厚,漆膜外观高于底漆,采用30:1空气辅助高压无气喷涂工艺,“湿碰湿”喷涂2道,干膜厚度达到50μm以上。
3.3.3 面漆
面漆需具有最佳的涂膜外观,表面丰满、平整、光滑,空气喷涂可以获得平整光滑的漆膜,达到最好的装饰效果。结合动车组车体喷涂面积较大,一次用漆量大的特点,采用隔膜泵喷涂工艺,“湿碰湿”喷涂2道,干膜厚度达到30μm以上。为获更好的外观效果,每遍油漆干燥后均进行打磨处理。
4 结语
研发的涂料体系于2009年11月进行了试生产,该批产品经检测达到了预期目的。涂料已于2010年6月喷涂了1列高速动车组,在武汉-广州区间使用,到目前已运用2年,涂料状态良好,该涂料体系能够达到高速动车组使用要求,为实现涂料国产化提供技术基础。
免责声明:本网站所转载的文字、图片与视频资料版权归原创作者所有,如果涉及侵权,请第一时间联系本网删除。
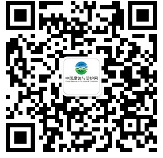
官方微信
《中国腐蚀与防护网电子期刊》征订启事
- 投稿联系:编辑部
- 电话:010-62316606-806
- 邮箱:fsfhzy666@163.com
- 中国腐蚀与防护网官方QQ群:140808414