近年来渤海某油田平台上生产水处理系统的管线发生多次刺漏,尤其是2015年上半年基本上每个月都会发生一次管线的腐蚀刺漏,严重影响了生产水处理系统的稳定运行。且这些管线刺漏点大都无法在线隔离补焊,只能采取打卡固定、玻璃胶带缠绕堵漏等临时措施,大大增加了生产水处理系统运行的安全、环保风险。因此,针对现场工况,查找管线刺漏原因并提出解决方案及预防措施意义重大。
现场油田群中,采取的是在某平台上加注缓蚀剂A和防垢剂A,注入浓度均为18×10-6,流经13.5Km的海管到达下游生产水系统中。添加缓蚀剂是油田常用的控制腐蚀的措施,加入微量或少量缓蚀剂可显着降低金属材料在该介质中的腐蚀速率,还可保持金属材料原来的物理机械性能不变。因此,该平台上生产水处理系统腐蚀刺漏的原因需要通过室内模拟实验,研究该系统中现场工况下的腐蚀情况,并推测系统中残留缓蚀剂A和防垢剂A的缓蚀及防垢效果,以此得到现场药剂的性能及注入浓度是否满足性能需求的结论。
本研究分别采用高温高压釜动态模拟评价实验装置以及EDTA滴定法测定钙离子,参考一系列行业标准规范分别进行缓蚀剂评价和防垢剂评价。并另外选取缓蚀剂B和防垢剂B作为对比药剂,进行现场在用防腐防垢化学药剂性能评价。
1 实验内容
1.1 腐蚀产物分析
对现场水处理系统中腐蚀挂片上取得的腐蚀产物开展X射线衍射(XRD)分析,以此得到主要腐蚀产物种类及含量,并确定现场腐蚀机理。
1.2 药剂性能评价
1.2.1实验原料
化学试剂:Na2SO4、NaCl、NaHCO3、FeCl3?6H2O、KCl、MgCl2?6H2O、无水CaCl2、浓盐酸、无水乙醇、石油醚:以上均为分析纯;油田现场在用缓蚀剂A、对比缓蚀剂B、油田现场在用防垢药剂A、对比防垢剂B、EDTA标准液(浓度为0.02mol/L)、NaOH溶液(浓度为2mol/L)、羧酸钙指示剂(根据标准自配)、高纯CO2气瓶、高纯N2气瓶。
1.2.2 实验过程
缓蚀剂评价实验过程中,实验条件根据现场工况制定,现场水处理系统温度为65℃,压力为常压,CO2含量为4%,H2S含量为200×10-6。首先取现场水样或按实验要求配制实验模拟水样2L,倒入高温高压釜内。利用N2对釜内进行除氧10min,抽真空合格,按实验要求向釜内通入CO2和N2调节釜内压力,并设置高压釜控制柜上的实验温度及实验转速。实验完成后将已达到实验周期的试片取出,观察、记录表面腐蚀状态及腐蚀产物粘附情况后,按要求进行挂片清洗工作,然后用滤纸将试片包好,贮于干燥器中,放置4h后称量,精确至0.lmg。观察并记录试片表面的腐蚀状况,若有点蚀,记录单位面积的点蚀个数,并用点蚀测深仪测量出最深的点蚀深度。
防垢剂评价实验首先要按照该油田斜板除油器出口的现场条件和水质分析结果配制模拟水溶液,成垢阳离子MgCl2.6H2O、CaCl2、NaCl、KCl配成阳离子溶液500mL;成垢阴离子Na2SO4、 NaHCO3配成阴离子溶液500mL,分别放入广口玻璃瓶中,在恒温水浴中通CO2 0.5h后塞紧瓶塞减少空气接触。按次序量取阳离子溶液50ml、一定浓度的待评防垢剂、阴离子溶液50ml置于100mL具塞比色管中,加塞密封,并分别标记为A-0、A-1、A-2,B-0、B-1、B-2、KB。其中A-0、A-1、A-2分别代表防垢剂A添加浓度为0、18×10-6、36×10-6;B-0、B-1、B-2分别代表防垢剂B添加浓度为0、18×10-6、36×10-6;KB为空白溶液。将7个比色管放入烘箱中,65℃,恒温24h。从烘箱取出后观察比色管内介质结垢情况并拍照记录,待温度降至室温后过滤留待滴定。
1.2.3 实验条件
根据水质分析结果,配制某油田斜板除油器出口模拟水,配方如表1。
表1 渤海某油田模拟生产水水样配方表
根据该油田取样现场工况,确定实验条件如表2所示。
表2 缓蚀剂和防垢剂评价实验条件
2 结果与讨论
由于本研究中现场设备的斜板除油器和预过滤罐处腐蚀挂片的腐蚀程度都较为严重,表面附着厚厚一层腐蚀产物(或混杂有油泥),因此对腐蚀产物开展XRD分析,得到腐蚀产物主要为SiO2、CaCO3、MgCO3、FeCO3,未发现FeS等含硫化合物,由此确定现场环境中H2S气体对腐蚀影响不大,腐蚀机理主要为CO2腐蚀。
采用动态高温高压釜进行腐蚀模拟评价实验,实验所用水样为现场水和模拟水,模拟水配方表如表1所示。经过对实验后挂片进行观察,并结合腐蚀实验数据进行分析得到均匀腐蚀速率和缓蚀率,参照海油企业标准Q/HS2064-2011《海上油气田生产工艺系统内腐蚀控制及效果评价要求》对生产设备及管道的内腐蚀程度进行划分:平均腐蚀速率CR<0.025mm/a的为低度腐蚀,0.025≤CR<0.125mm/a的为中度腐蚀,0.125≤CR<0.250mm/a的为高度腐蚀,CR≥0.250mm/a的为严重腐蚀。
对现场3处取样位置(分别为气浮选器A、气浮选器B、斜板除油器处)取得水样进行同样工况条件下的腐蚀对比实验,结果如表3、表4所示。由结果得知在其他相同工况条件下,由于斜板除油器处水体流速最大,导致腐蚀速率最高,因此后续的缓蚀剂和防垢剂的评价实验围绕斜板除油器水质展开。
表3 空白条件下气浮选器A、气浮选器B、斜板水质腐蚀评价实验
表4 斜板除油器处水质腐蚀评价对比
根据表4得到在斜板除油器处无论是现场水质还是模拟水质,挂片的腐蚀速率均很高,分别为0.9336mm/a和0.7114mm/a,均达到了严重腐蚀程度,因此排除了水质组分差异的问题,推测现场设备管道穿孔的主要原因是现场水缓蚀剂有效成分不足或缓蚀剂性能方面存在问题。
图1 模拟水加入现场缓蚀剂A腐蚀评价实验
图1为向模拟水中加入不同浓度的现场缓蚀剂A后的腐蚀评价结果。从图中可以看出,随着现场缓蚀剂A的加注以及加注浓度的升高(从18×10-6提高到36×10-6),腐蚀速率分别降至0.4585mm/a和0.3443mm/a。腐蚀速率虽有所下降,但缓蚀效果较差,分别为35.56%和51.60%。由于挂片腐蚀速率仍然较高,属于严重腐蚀,因此排除缓蚀剂加注浓度不足导致缓蚀率较低的因素,基本确定现场缓蚀剂A性能存在一定问题,需要使用对比药剂进行进一步验证。
图2 现场水中不同缓蚀剂的腐蚀评价
如图2为在现场水质中进行现场缓蚀剂A和缓蚀剂B的对比效果评价。加注18×10-6的现场药缓蚀剂A时,腐蚀速率为0.2619mm/a,缓蚀率仅为71.94%,属于严重腐蚀;而加注18×10-6的缓蚀剂B后,腐蚀速率大幅下降,腐蚀速率降至0.0871mm/a,为中度腐蚀,缓蚀率达到90.67%。验证了现场缓蚀剂A的性能存在问题。
为了确定现场水样中防垢剂的含量与种类是否符合现场防垢需求,选取现场所用防垢剂A和对比防垢剂B进行防垢剂评价实验,防垢率计算结果如表5所示。通过实验结果可以看出,当加注现场防垢剂A 18×10-6的情况下,防垢率为23.3%,即使将防垢剂浓度提高一倍至36×10-6时,防垢率也仅为56.7%;而对比相同条件下的防垢剂B,发现防垢剂B的防垢效果要远远好于现场防垢剂A,可以判断现场防垢剂存在一定的性能问题,而并非防垢浓度加注不足。
表5 防垢剂A与防垢剂B的防垢率
3 结语
通过对某油田水处理管线的腐蚀产物的某RD表征结果可知,管道内的腐蚀产物主要为SiO2、CaCO3、MgCO3、FeCO3,未发现FeS等H2S腐蚀产物,说明现场的腐蚀形式以CO2腐蚀为主。
通过动态高温高压釜实验对缓蚀剂性能进行评价,随着现场药剂的加注以及加注量从18×10-6升高到36×10-6,腐蚀速率分别降至0.4585mm/a和0.2619mm/a,缓蚀率仅为35.56%和51.60%,仍然属于严重腐蚀,因此造成现场刺漏的主要原因是现场药剂性能本身存在问题,无法满足平台设备、管线的防腐、防垢需求。
针对现场腐蚀产物中发现CaCO3、MgCO3等结垢产物,通过EDTA钙离子滴定法防垢剂性能评价实验发现,现场浓度防垢剂A防垢率仅为23.3%,将浓度增加一倍至36×10-6后防垢率也仅提高到56.7%,对比防垢剂B则防垢率分别提升至73.4%和86.7%,因此得出现场防垢剂性能不足,存在垢下腐蚀的风险,建议现场优化防腐防垢药剂,改善腐蚀刺漏现状。
更多关于材料方面、材料腐蚀控制、材料科普等方面的国内外最新动态,我们网站会不断更新。希望大家一直关注中国腐蚀与防护网http://www.ecorr.org
责任编辑:王元
《中国腐蚀与防护网电子期刊》征订启事
投稿联系:编辑部
电话:010-62313558-806
邮箱:fsfhzy666@163.com
中国腐蚀与防护网官方 QQ群:140808414
免责声明:本网站所转载的文字、图片与视频资料版权归原创作者所有,如果涉及侵权,请第一时间联系本网删除。
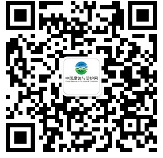
官方微信
《中国腐蚀与防护网电子期刊》征订启事
- 投稿联系:编辑部
- 电话:010-62313558-806
- 邮箱:fsfhzy666@163.com
- 中国腐蚀与防护网官方QQ群:140808414