1引言
铝合金具有密度小、比强度高、加工性好等优点,而被广泛应用于制造业的各个领域[1]。5083铝合金属于铝镁系,在舰船制造中得到大量的应用[2-4]。但在苛刻的海洋腐蚀环境中服役时,氯离子易沿着铝合金表面的活性点进入铝合金内部,加速铝合金腐蚀。因此需要对铝合金进行表面处理,提高铝合金的耐蚀性能[5-6]。
常用的铝合金表面处理方法有阳极氧化、微弧氧化、电泳、电镀等[7]。微弧氧化是利用阳极弧光放电产生瞬时高温,将表面金属融化,生成陶瓷质氧化膜的方法[8-10]。由于其具有工艺简单、所需设备少、膜层厚度均匀、硬度高等优点,在铝合金防腐中得到广泛的应用[11]。
传统的微弧氧化表面较为粗糙,且存在大量的孔洞结构,使得腐蚀介质很容易通过膜层,侵入到基体表面[12-13]。本文通过在电解液中添加纳米TiO2颗粒,设计三因素三水平的正交试验,优化了微弧氧化的工艺参数,有效改善了膜层的表面质量,提高了铝合金的耐蚀性能。
2正交试验设计
试验所用的材料为5083铝合金,试样规格为20mm×10mm×3mm,其化学成分见表1。锐钛矿纳米 TiO2(上海阿拉丁生化科技股份有限公司产),硅酸钠 Na2SiO3·9H2O(天津市风船化学试剂有限公司产)和氢氧化钾 KOH(天津市风船化学试剂有限公司产)。以上化学试剂均为分析纯。
表1 5083铝合金的化学成分
成分 |
Mg |
Mn |
Si |
Cu |
Zn |
Ti |
Cr |
Fe |
Al |
含量 |
4.0-4.9 |
0.4-1.0 |
≤0.4 |
≤0.1 |
≤0.25 |
≤0.15 |
0.05~0.25 |
0~0.4 |
余量 |
电流密度、氧化时间、TiO2浓度等是微弧氧化过程中的重要参数[14-15]。本次试验将电流密度、氧化时间、TiO2浓度作为三个因素,设计了三因素三水平的正交试验。表2为微弧氧化各个因素及其水平。电解液组成为10g/L NaSiO3、1g/L KOH以及不同浓度的纳米TiO2。
表2 微弧氧化工艺因素/水平
水平 因素 |
1 |
2 |
3 |
电流密度(A) A |
10 |
15 |
20 |
氧化时间(min)B |
10 |
20 |
30 |
TiO2浓度(g/L)C |
2 |
4 |
6 |
2.1微弧氧化薄膜的表面形貌分析
试验所用金属基体为20mm×10mm×3mm的5083铝合金,对于微弧氧化的试样,在进行扫描之前先要喷金处理,喷金时间为17s。将喷金处理后的铝合金试样放置在电解液中作为阳极,通电生成氧化膜后采用美国FEI公司的Nova Nano SEM50场发射扫描电镜对如表3不同工艺参数下得到的微弧氧化膜层进行表面观察。图1(a)-图(i)分别为试样1#-试样9#膜层放大500倍后的形貌图。
表3 不同工艺参数的试样编号
工艺参数 试样编号 |
电流密度(A) |
氧化时间(min) |
TiO2浓度(g/L) |
1# |
10 |
10 |
2 |
2# |
10 |
20 |
4 |
3# |
10 |
30 |
6 |
4# |
15 |
10 |
4 |
5# |
15 |
20 |
6 |
6# |
15 |
30 |
2 |
7# |
20 |
10 |
6 |
8# |
20 |
20 |
2 |
9# |
20 |
30 |
4 |
图1 不同工艺参数下放大500倍形貌图
从图1中可以看出,电流密度较小时,微弧氧化的表面较为平整,随着电流密度的增大,膜层表面变得粗糙不平。在图1(g)中看到表面起伏明显要比图1(a)、图1(d)大,图1(h)中还存在熔融物堆积,导致微弧氧化膜层与基体的结合力较差,在清洗过程中常常出现氧化层脱落现象,因此电流密度不宜过大。当氧化时间为10min时,膜层表面比较平整,但存在较多孔洞,如图1(a)、图1(d)、图1(g)。当铝合金在腐蚀介质中服役时,这些微小的孔洞会成为腐蚀介质进入基体的通道,使得膜层的耐蚀性能降低。随着氧化时间的增加,表面孔洞逐渐减少。
TiO2的浓度的变化对表面膜层的形貌影响从图1中无法直观的看出。因此在电流密度15A/dm2和氧化时间30min条件下,研究了纳米TiO2添加量对薄膜表面形貌的影响,如图2所示。添加纳米TiO2之前薄膜表面凹凸不平,且存在许多宏观孔洞(如图2a所示),加入纳米TiO2之后,薄膜表面趋于平整,变得光滑致密(如图2b所示)。说明纳米TiO2颗粒的添加能有效改善膜层的表面质量,减少微裂纹以及孔洞的数量,使膜层变得平滑而致密[16]。分析认为未添加纳米TiO2时,铝合金基体与电解液中的离子发生反应,生成以Al2O3为主的反应产物,熔融的反应产物遇到电解液时,被电解液冷凝而形成类似火山峰的孔洞,同时冷凝时的热应力易导致膜层产生微裂纹。添加纳米TiO2后,由于纳米TiO2颗粒的表面活性较高,能吸附离子形成带电胶粒,在电场的作用下聚集到微弧氧化膜表层,参与并促进膜层的反应。另外,在氧化过程中纳米TiO2颗粒能沉聚在熔融层表面,堵塞放电产生的气孔,使陶瓷层的致密度提高,膜层的表面质量得到改善[17,18]。
(a)15A/dm2,30min,0g/L (b)15A/dm2,30min,4g/L
图2 添加纳米TiO2前后薄膜表面宏观形貌
2.2微弧氧化薄膜EDS能谱分析
表4为1#-9#膜层表面的EDS能谱分析结果。可见膜层的主要元素组成为O、Na、Al、Si、K、Ti六种元素,同时还存在少量的Na、K、Si元素。分析认为膜层中的Na、K、Si元素来自于电解液中的NaSiO3和KOH。Ti元素也是膜层的主要组成元素,当电解液中TiO2的浓度从2g/L增加到4g/L时,样品中Ti的原子比有所增加,但当TiO2的浓度从4g/L增加到6g/L时,试样的Ti原子比无明显变化。表明当电解液中TiO2浓度达到4g/L时,溶液中TiO2的浓度已经饱和。因此可以选定正交试验最佳的TiO2浓度值为4g/L。
表4 正交试验能谱分析
元素 原子百分比 |
O |
Na |
Al |
Si |
K |
Ti |
1# |
64.98 |
0.69 |
27.18 |
5.00 |
0.14 |
2.01 |
2# |
67.30 |
1.99 |
12.34 |
13.62 |
0.78 |
3.98 |
3# |
69.53 |
2.40 |
11.92 |
11.54 |
0.66 |
3.96 |
4# |
67.07 |
2.28 |
12.27 |
12.64 |
1.02 |
4.74 |
5# |
73.03 |
2.85 |
1.22 |
15.39 |
1.16 |
6.36 |
6# |
58.36 |
3.48 |
10.59 |
18.10 |
2.18 |
7.28 |
7# |
68.98 |
3.21 |
6.91 |
13.44 |
1.33 |
6.13 |
8# |
59.84 |
3.99 |
13.62 |
17.60 |
1.27 |
3.68 |
9# |
67.96 |
1.65 |
9.69 |
12.61 |
0.64 |
7.44 |
2.3微弧氧化膜层的物相分析
图3为2#试样、6#试样、7#试样的XRD能谱。不同工艺条件下制备的膜层表面均存在Al、Al2O3及锐钛矿TiO2的特征峰。其中Al的特征峰主要来自于基体,Al2O3是微弧氧化膜层的最主要成分,同时膜层中还含有少量锐钛矿纳米TiO2颗粒。虽然微弧氧化的工艺参数不同,但膜层的物相组成并没有发生太多的变化,表明铝合金微弧氧化过程中的主要反应为基体表面Al合金的熔融氧化过程。而电解液中的纳米TiO2颗粒嵌入到微弧氧化膜层中,并保持了原有结构。
图3 微弧氧化膜层的XRD分析
2.4正交试验结果的分析
以膜层表面形貌和膜层中Ti原子含量为评价指标,对微弧氧化的膜层质量进行指评价。由上述分析结果可知,膜层表面越平整,孔洞越少,膜层耐蚀性越好,膜层中Ti的原子比越大,代表膜层中含有的TiO2浓度越高,膜层越致密。
根据正交试验计算表5,分析各因子对薄膜表面形貌的影响,K12>K13>K11,K22>K23>K21,K33>K31>K32。因此,获得表面形貌的因素与水平的最佳搭配为A2B2C3,即为电流密度15A/dm2,氧化时间20min,TiO2浓度6g/L。各因子对TiO2浓度的影响,K12>K11>K13,K23>K22>K21,K32>K33>K31。因此,获得TiO2浓度的因素与水平的最优搭配为A2B3C3,即为电流密度15A/dm2,氧化时间30min,TiO2浓度4g/L。根据表4的正交试验能谱分析结果,最佳的TiO2浓度值为4g/L。
综上,选定氧化电流为15A/dm2和TiO2浓度为4g/L,设定氧化时间分别为10min、20min、30min,进行性能表征,选出最优的微弧氧化参数。
表5 正交试验计算表
因子 试样 |
A |
B |
C |
形貌 |
Ti原子比 |
|
1 |
1 |
1 |
1 |
10 |
2.01 |
|
3 |
1 |
3 |
3 |
13 |
3.96 |
|
5 |
2 |
2 |
3 |
11 |
6.36 |
|
6 |
2 |
3 |
1 |
14 |
7.28 |
|
7 |
3 |
1 |
3 |
17 |
6.13 |
|
8 |
3 |
2 |
1 |
16 |
3.68 |
|
形 貌 |
Kj1 |
11.333 |
11.667 |
12.333 |
|
|
Kj2 |
15.667 |
13.667 |
13.333 |
|
||
Kj3 |
11.667 |
13.333 |
13.000 |
|
||
Ti原子比 |
Kj1 |
3.3317 |
4.293 |
4.323 |
|
|
Kj2 |
6.127 |
4.673 |
5.387 |
|
||
Kj3 |
5.750 |
6.227 |
5.483 |
|
3耐蚀性能研究
采用德国Zahner公司的IM6电化学工作站,对基体及经不同微弧氧化时间处理所得薄膜的耐蚀性能和腐蚀机理进行研究。通过电化学阻抗(EIS)分析得出薄膜的腐蚀机理,通过极化曲线研究薄膜的耐蚀性能。电化学测试所用的电解液为3.5wt.%NaCl,电化学试样尺寸为10mm×10mm×3mm。
3.1电化学阻抗分析
图4为不同试样的电化学阻抗图,从图4(a)中可以看出,铝合金微弧氧化膜层阻抗模值随氧化时间的延长而增加,尤其其是在低频区表现的更为明显。但当氧化时间由20min增加到30min时,阻抗模值增加幅度较小。从图4(b)中可以看出,中频区相位角的峰随着氧化时间的增加而变宽,可知随着氧化时间的增加,微弧氧化膜层越来越接近于一个电阻值很大、电容值很小的隔绝层[19]。从图4(c)中可以看出,基体呈现一个容抗弧和一个感抗弧,分别代表着双电层电容和钝化膜点蚀诱导期感抗。微弧氧化之后有两个容抗弧,分别代表表面疏松层容抗和内部致密层容抗,且随着氧化时间的增加,容抗弧半径增大,表明试样的腐蚀电阻增大,耐蚀性增加。图4(d)为基体及微弧氧化的试样等效电路图,其中Rs表示溶液电阻,Qdl为双电层电容,Rct为电荷转移电阻,L为钝化膜点蚀诱导期感抗,Rm为钝化膜电阻,Qa、Qb分别表示疏松层和致密层常相位角元件,Ra表示疏松层电阻,Rb表示致密层电阻。
(a)阻抗模值(b)相位角
(c)Nyquist图(d)等效电路图
图4 不同试样的EIS谱图
3.2微弧氧化试样的极化曲线
图5为不同试样的极化曲线,拟合得到的电化学参数如表6所示。与基体试样相比,经微弧氧化处理后,试样的自腐蚀电位显著提高,且自腐蚀电位随着氧化时间的延长而升高。分析认为氧化时间越长,膜层越厚,电解液越难进入内部发生腐蚀。微弧氧化后膜层的自腐蚀电流密度相较基体下降了两个数量级,表明铝合金经过微弧氧化处理之后耐蚀性能显著提高。
图5 不同试样的极化曲线
表6 极化曲线拟合数据
试样氧化时间 |
E(V) |
Icorr/(A/cm2) |
0min |
-0.73898 |
5.2827E-5 |
10min |
-0.072836 |
4.2615E-7 |
20min |
-0.032238 |
2.9444E-7 |
30min |
0.0085396 |
3.1063E-7 |
3.3盐雾实验结果分析
按照GB/T10125-2012《人造气氛腐蚀试验-盐雾试验》标准,对铝合金基体及电流密度15A/dm2,TiO2浓度4g/L,氧化时间30min条件下制备的微弧氧化试样进行了500h中性盐雾加速腐蚀试验,图6为盐雾试验500h之后试样的表面形貌及对应的能谱分析结果。
(a)基体(b)微弧
图6 盐雾500h形貌及能谱分析
经中性盐雾加速腐蚀过程中,Cl-首先在铝合金表面活性点处形成点蚀,并随着腐蚀时间的延长,点蚀坑不断长大。500h后在铝合金基体表面出现直径约为200μm的腐蚀坑,且在腐蚀坑周围存在显著的龟裂特征,表明此时铝合金表面氧化膜被破坏,基体发生严重腐蚀。而微弧氧化之后的膜层表面虽然也发生了腐蚀,但是膜层基本完整,并未出现大的腐蚀点。
通过能谱数据可以看出,基体表面腐蚀坑附近有出现了Cl、Fe、Mn、Si等元素,其中Cl元素是腐蚀发生的主要原因。由于Cl—元素容易在自然氧化物膜薄弱处发生选择性吸附,形成活性—钝性腐蚀电池,具备了点蚀产生的条件。之后Cl—穿过自然氧化膜进入铝合金基体,排挤并取代氧化物中的O原子,形成可溶性氯化物,导致氧化膜局部溶解和破裂,使腐蚀液浸入到基体表面。Fe、Mn、Si等元素是5083铝合金中含有的微量元素。综上所述,经过500h盐雾试验之后,铝合金以及微弧氧化的表面均发生了不同程度的腐蚀,但经过微弧氧化处理后,其表面腐蚀程度明显弱于未经微弧氧化处理的基体表面,表明经微弧氧化处理之后,铝合金的耐蚀性能得到了显著提升。
4 结论
(1)纳米TiO2颗粒的添加能有效改善膜层的表面质量,减少微裂纹以及孔洞的数量,使膜层变得平滑而致密。
(2)5083铝合金表面纳米TiO2改性的最优微弧氧化工艺参数为:电流密度15A/dm2,TiO2浓度4g/L,氧化时间30min。
(3)微弧氧化膜层的电化学阻抗谱呈现双电容特征,表明纳米TiO2改性的微弧氧化膜层由外层多孔层和内层致密层组成。
(4)纳米TiO2改性的微弧氧化膜层具有优异的耐蚀性能,能对铝合金基体起到良好的保护作用。
更多关于材料方面、材料腐蚀控制、材料科普等方面的国内外最新动态,我们网站会不断更新。希望大家一直关注中国腐蚀与防护网http://www.ecorr.org
责任编辑:王元
《中国腐蚀与防护网电子期刊》征订启事
投稿联系:编辑部
电话:010-62313558-806
邮箱:fsfhzy666@163.com
中国腐蚀与防护网官方 QQ群:140808414
免责声明:本网站所转载的文字、图片与视频资料版权归原创作者所有,如果涉及侵权,请第一时间联系本网删除。
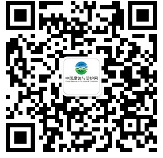
官方微信
《中国腐蚀与防护网电子期刊》征订启事
- 投稿联系:编辑部
- 电话:010-62316606-806
- 邮箱:fsfhzy666@163.com
- 中国腐蚀与防护网官方QQ群:140808414