0 引言
目前轨道车辆车体用钢材主要有不锈钢、铝合金、碳钢3种,不锈钢材料主要用于城市轨道交通车辆,铝合金材料主要用于高速动车组和城市轨道交通车辆,碳钢材料主要用于普通25型铁路客车。相比于不锈钢和铝合金,碳钢价格较低,表面化学稳定性能相对较低,其耐腐蚀性能不高,在大气条件下极易产生严重腐蚀,从而影响车辆的使用寿命和安全性能,因此,需对碳钢车进行专门的防腐处理。目前对碳钢车采用的防腐处理方式主要是涂装防腐保护,即在金属基体表面涂覆一层或多层具有一定厚度的保护涂层,使得金属基体与外界环境隔离,从而使金属基体得到保护,根据多年实践证明碳钢车采用涂装防腐方式是目前最经济、最实用的方式。但碳钢车涂装防腐的好坏与设计结构、涂装技术和车辆的运营环境有很大关系。本文根据厂修车车体腐蚀现状,就设计结构、涂装技术和运营环境对碳钢车体的腐蚀影响及改进措施进行探讨。
1 客车车体腐蚀现状
根据厂修车辆钢结构车体腐蚀状况调研结果,车体端墙钢结构的腐蚀主要集中在通过台区域(端门槛、端墙板下沿、地板)渡板、车端墙板下沿、端墙外侧安装座等区域;侧墙钢结构的腐蚀主要在底架边梁与侧墙连接区域的侧墙板、窗周边、立柱下口、门框周边等区域。底架钢结构腐蚀主要集中在直排厕洗所下方区域、厕洗所下方托梁、地板、车下吊挂件等部件。
2 腐蚀影响因素及改进措施
2.1 材料选择
从调研车辆来看,厕所、盥洗室、通过台等部位易积水,防腐涂层长期被水浸泡后容易起泡脱落,失去防腐效果,而碳钢材质不耐腐蚀,遇水后容易产生电化学腐蚀,使部件强度降低,引起安全隐患。
为了提高这些部位的防腐性能,在车体钢结构设计时可对这些易腐蚀部位的金属材质进行改进。通过台区域渡板在2016年新造车全部由耐候钢材质改为不锈钢材质,厕洗所托梁也由原来的09CuPCrNi改进为06Cr19Ni10,在新研制的时速200 km碳钢动车组上,部分部件材质也将原来常用的Q345NQR2改进为Q350EWR1,实践表明材质的改进大大提高了钢结构车体的防腐性能。
2.2 设计结构
车体在结构中存在封闭、半封闭及搭接(侧墙板与底架边梁)等结构,在车内防腐涂装时往往很难施工,防腐效果较差。在车辆长期运营中此类结构容易积水、积灰,且后期难以清理,腐蚀介质可渗透到金属表面,最终发生电化学腐蚀。针对厂修车车体腐蚀状况,从设计结构进行了以下改进优化。
尽量避免不合理搭接结构。25G型车底架边梁与侧墙连接以前采用搭接结构,搭接面与外界相通,焊缝及搭接面容易积水,腐蚀严重,为此在25T型车上对此结构进行了改进,采用底架边梁刨槽与侧墙板在槽内对接,外侧采用对接满焊结构,这样减小了外界腐蚀介质侵入车内的可能性,减少了该区域的腐蚀,改进措施见图1。
车体内部帽型立柱与墙板塞焊后形成透气的封闭结构,后期无法对其内部进行防腐,在2016年中车研制的时速160 km动力集中动车组上已经将帽型梁柱改为乙型梁柱(见图2),更改后结构相对简单,可方便地在车内进行表面处理和防腐涂装,有利于提高车体防腐性。
为了避免厕洗所下方地板积水加速该区域钢结构的腐蚀,在此区域设置排水孔或排水槽,并增加翻边防止水流入其他区域。
对于设计结构中无法改变的封闭腔、搭接焊缝,为了避免内腔和搭接面无法进行涂装防腐而产生的腐蚀,要求焊接封闭前对内部预涂刷防腐漆,并对焊缝周边涂打密封胶,阻止水气、氧气等腐蚀介质的进入,从而避免内腔和搭接面内部遭受腐蚀。
2.3 涂装防腐
2.3.1 涂装体系
纵观铁路客车涂装体系发展历程,主要经过了4个阶段。第一阶段:80年代前22型客车外部主要采用的是“磁化铁酚醛防锈底漆+油性腻子+醇酸磁漆”防腐体系,内部采用“酚醛底漆+石棉沥青”体系;第二阶段:90年代涂装体系主要采用“铁红环氧酯防锈底漆+环氧酯腻子+丙烯酸改性醇酸磁漆”;第三阶段:2002年车外涂装体系采用“双组分环氧树脂防锈漆+不饱和聚酯腻子+环氧中涂层+丙烯酸聚氨酯面漆层”,内部采用双组分环氧604重防腐涂料。第四阶段:2015年开始外部采用“双组分环氧树脂防锈漆+双组分不饱和聚酯腻子+双组分丙烯酸聚氨酯中涂层+丙烯酸聚氨酯面漆+丙烯酸聚氨酯清漆”,内部采用“双组分环氧底漆+双组分环氧重防腐涂料+水性阻尼涂料”。
在涂装体系发展的4个阶段,涂装体系经历了单组分涂料向双组分涂料的变化,涂装体系的耐盐雾性能、耐候性、耐有机溶剂性能、耐酸碱性能以及耐高低温循环交变性能都有了很大的提高。铁路客车钢结构挖补和截换时间从7.5 a到12 a直至现在的15 a,车外涂层寿命现在也超过4 a,从第1次返厂修理车来看,车外仅需要局部修补,车内腐蚀情况也很好。
2.3.2 涂装前表面工艺
涂层是否有良好的防腐效果不仅与于涂装体系本身有关系,同时与基材表面处理也是有直接关系的。在基材表面上经过打磨或喷砂可形成大量尖峰,增大基材与涂料间接触面积,提高总的范德华力和机械钉扎效果,从而保证涂层与基材的附着力。涂层与基材间良好附着可更好地抵抗外界腐蚀介质对基材的腐蚀,同时也可以阻碍腐蚀生成物的进一步扩散,降低腐蚀速度。从调研车辆来看,有些车辆腐蚀和涂层脱落是出现在涂层与金属基体界面,这说明基材表面处理不到位。目前要求车辆生产前必须进行钢材预处理,对热轧钢板通常采用喷砂预处理,清洁度要求必须达到GB/T 8923—2013《涂覆涂料前钢材表面处理表面清洁度的目视评定》中的Sa 2.5 级。对冷轧钢板使用磷化预处理方式,磷化膜质量必须达到GB/T 6807《钢铁工件涂装前磷化处理技术条件》,并且表面处理后对表面喷涂一层硅酸锌预涂底漆防止工序间零部件锈蚀。
2.3.3 涂装过程管控
目前车辆使用的涂料都为双组分涂料,在涂料调配过程中要严格按照涂料使用说明书按比例调配,固化剂用量不准确对涂膜的致密度和附着力都会产生影响,从而影响涂层寿命。涂装过程中的温度、湿度会影响两组分的成膜化学反应,从而影响涂膜的致密度及其网状结构;同时,由于涂装是一个特殊的过程,只能控制涂装中间过程来保证涂装最终质量,所以涂装过程应对参数(环境温度、相对湿度、工件表面清洁度、粗糙度、施工黏度、干燥温度、干燥时间、涂层厚度等)、涂装材料、人员、工艺装备等进行严格的管控,从而保证最终的涂装效果。各新造厂家也都建立了涂装流水线,涂装机器人、静电喷涂等新型工艺设备的投入让涂装效率及涂装质量都明显得到提升。
2.4 车辆运营环境
2.4.1 环境温湿度的影响
从修理车的调研结果来看,无论南方局、北方局车辆都有腐蚀,但是南方局和较潮湿闷热区域的车辆腐蚀要严重一些,这主要是因为高温湿热会加速腐蚀。通常在相对湿度低时腐蚀较慢,只有当相对湿度达到一定限度之后,腐蚀速度明显加快,这个相对湿度的数值称为临界相对湿度,理想状态下钢材的临界相对湿度大约是70%,如果大气或者钢材表面有污染时,临界相对湿度会降低,也就是在更低的相对湿度下,金属就会加速腐蚀。同时,在钢材已经腐蚀且处于相对湿度高于临界湿度的环境下时,温度升高腐蚀速度相应加快。
2.4.2 车辆维护的影响
按铁总招标要求,车体使用寿命为30 a。30 a中,车辆会经过数次段修、厂修,中间过程对涂膜的修补对车辆寿命影响是非常大的。在调研中发现,部分车辆在段修时,由于车辆段检修周期短、缺少专业技术人员和相应专业设备对人、机、物、法、环、测把控的不到位,导致重涂面漆的车辆经过几个月的运用即发生严重褪色的现象。建议段修时加强工艺和质量控制,采购满足运辆客车函[2015]73号要求的涂料,并按照文中段修涂装工艺规范进行涂装,严格执行表面处理、喷涂施工的要求,以保证涂层使用寿命,从而降低车辆的维护成本。在以往车辆维护清洗过程中,也存在使用强酸、强碱洗车,这会导致面漆过早失光老化,降低涂膜性能。
在车辆运用中也应当注意维护,对车辆定期清洗,减少污物附着,应当使用中性清洗液,避免使用强酸、强碱。同时,在车辆保养过程中也要对涂膜破损及锈蚀区域进行修补,防止车体的进一步腐蚀。
3 结语
通过对铁路客车车体部件材质的改进、设计结构的优化、涂装体系和涂装工艺的改进,目前出厂的铁路客车车体防腐质量得到了很大的提升,涂层寿命也延长很多,有的客车车外涂层甚至可以达到一个厂修期,并且也避免了运营过程中由于腐蚀产生的安全隐患。
责任编辑:王元
免责声明:本网站所转载的文字、图片与视频资料版权归原创作者所有,如果涉及侵权,请第一时间联系本网删除。
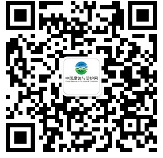
官方微信
《中国腐蚀与防护网电子期刊》征订启事
- 投稿联系:编辑部
- 电话:010-62316606-806
- 邮箱:fsfhzy666@163.com
- 中国腐蚀与防护网官方QQ群:140808414