粉末喷涂工序少,产生的问题的环节也少。主要工序只有前处理、静电喷涂和烘烤三个工序。其中影响质量的主要工序应属前处理工序。然而许多生产厂家对此没引起足够的重视,以致带来许多后患。有些隐患还不是短期内能反映出来。一般较先进的工艺、用在前处理上的花费约占总费用的25%以上。
从生产工艺中出现的各种问题分析。我认为设备的先进程度和原料的好坏,对产品质量又起着决定性作用,两者缺一不可。我们作为工程技术人在这个问题上应该建立共识,决不能在上新喷粉生产线时。只图一时省钱就凑和,采用低标准的生产设备和工艺、材料,必将给长期生产带来许多后患,甚至生产不出高质量产品。不少厂家上了涂粉生产线,应用不久就被迫下马或跟换新设备,概出于以上原因。我们常看到国外产品表面涂装很漂亮,其主要原因之一是他们不断地采用先进的设备和新工艺新材料。
从这个意义上分析,对涂粉设备及涂料生产厂家来讲,在当今市场竞争条件下,非优质设备和涂料是没有发展前途的。特别是在国内上百个喷粉设备和粉末涂料生产厂家竞争条件下,更是如此。仅我们陕西省已经有近十家设备及粉末涂料生产厂转产或倒闭。
产生缺陷的分析探讨
(一)前处理方面:
1、除油除锈不彻底
首先我不主张用除油除锈二合一的工艺。二合一工艺本身容易产生这个问题。因为通常用的除油、除锈液配方事项互消弱的,而不是相辅相成的,因此很难搞出合理的二合一或三合一工艺(包括磷化)配方。另一工艺方发式用金属清净剂处油,更不能彻底除油。因为金属清洗剂除油效果差,一般只能是油脂浮到金属机体表面上,要除掉它,还需一种机械力,如没有这种外加机械力,就会造成处油不彻底,可见金属清洗剂不适合于工业化批量生产。我主张用碱化学除油。碱液对动植物油去除效果很好,因其产生皂化反应。但对矿物油去除效果较差,为去除矿物油,还需加乳化剂。另外水洗质量对去油效果影响较大,一是水质,二是水温。三是要分级翻动,三项均良好,目的只有一个,就是用纯净水清洗油脂。最后一级最好用去离子水清洗。
2、磷化膜粗糙等问题
钢铁件喷粉前必须磷化,国外普遍采用的是喷沙磷化工艺。我们用的磷化液,许多是不够理想的,这就直接影响到磷化膜质量。比较常见的是磷化膜粗糙问题。对此我想从三个方面进行分析:第一是选好磷化液,这是保证质量的根本。首先涉及的问题是选高、中、低温那种类型?从其发展史来看,开始是有高温厚膜型,现已进展到中、低温薄膜型。国内低温磷化液,由于溶液不够稳定,维护困难,磷化膜附着力较差,有的甚至不耐水冲洗等,较少被采用。有的低温磷化液较理想,但价格又较贵。尽管低温磷化是发展方向,但达到普遍应用的效果,还有待于新的突破。目前祥和磷化(成都)公司已成功的解决了常温磷化(钝化)粉剂问题,并已批量供货。目前普遍采用的还是中温磷化工艺。其次是选锌系,铁系\锌钙系等那一种磷化液?相比之下,我认为锌钙系磷化液较好,对喷塑前处理要求薄涂层磷化膜来考虑,铁系亦是一种较好的选择。它除了锌系的一些优点外还具有耐热性好。中温条件下水解少,沉渣较少,溶液易维护,机械强度好,耐蚀性强,膜较厚时结晶仍很细。而铁系的磷化铁膜,耐蚀性较差。总之选中温锌钙系磷化液较好。第二是必须随时调整磷化液,主要是调整酸度比和含锌量,这两个因素都直接影响成膜率和结晶的粗细度。必需根据工作量定期和不定期的分析溶液,及时加以调整,无分析数据,盲目补充料液是不科学的。第三是控制膜层的厚度各类磷化膜都有其最佳厚度,例如锌系和钙锌系最佳膜厚为1.5~2克每平方米,而铁系为0.5~0.7克每平方米,在这个范围内其防腐性能最好,晶粒最细如过厚着影响膜的柔韧性和附着力,晶粒也变粗。通常生产中出现的问题是磷化膜偏厚。下面就如何克服晶粒变粗问题谈几点意见。
第一是用表面调整剂的办法使晶粒变细化。即在工件磷化前进行一次表面调整处理,使金属表面吸附一层胶体粒子,形成一层“活化中心”,进而磷化时,在次“活化中心”上继续成长,这样可使磷化晶粒明显变细,特别是低温磷化之前,表调是不可少的一步处理方法。
第二是往磷化液中加晶粒细化剂,如钙、镍等盐类作改进剂,最好用复和型盐类,效果更好,同时可降低低沉渣量。
第三是磷化后进行钝化处理,使磷化膜上面形成的峰窝结构,从而提高耐蚀性能,同时提高涂层的附着力。
第四是随时调整磷化液的酸度比和锌含量。前面已谈过了。
(二)静电喷粉方面:
1、喷粉不均主要是供粉桶内粉末流化不均匀所致。应更换微孔板或调节微孔板下的供气系统,使使粉层恢复正常沸腾状态,即可消除。有是气压偏低,则加大气压即可消除。另一可能是管道堵塞,包括文丘里咀堵塞,则需清理管路。若文丘里经常堵塞,则属文丘里的积粉咀用材(如黄铜等)不当,只要把他改成聚四佛乙烯材料,就可以解决,喷枪头堵塞也可用同样的方法解决,如果供粉同捅不是流化床型的,则需改善搅拌器或加装振汤器,防止粉层出现空洞,供不上涂料。 2、粉末上粉率低:
(1)电压低或无高压是主要原因之一。需调高输出电压或维修高压静发生器。
(2)工件接地不良,挂钩或低层电阻大;如喷第二遍粉时或腻予不导电,都会使低层电阻大。用普通喷枪喷第二遍粉时必须把工件预热到104℃左右,进行热喷,利用热溶吸附的原理。热喷作业还有利于粉末流平,用变色龙喷枪,可以克服低层电阻大的问题,第二遍喷涂可以实现冷喷。它是利用附加板行成喷室恒定静电场的原理实现的。
(3)粉末荷电量过大或小也影响上粉率。对环氧型粉末实验结果;当粉末带电电量为1.6微库仑/克时,上粉率可达百分之九十五以上。而电晕放电喷枪只能使粉料带电0.8~0.9微库仑,所以上粉率只达百分之八十五左右。这个数椐说明带电量对上粉率的影响。因此摩擦喷枪不如静电喷枪上粉率高。一般控制电流不须过大,60微库仑左右已够用了,否则荷电量太大,也容易引起过流断电,过大反而容易引起法拉第屏遮效应。一般是荷电量影响上粉率,荷电量小原因,除了不同粉末涂料的自身反电离效应有差别外,主要原因是由于高压静电发生器故障引起,需进行维修,使恢复高压。
(4)气压过大:会抵消静电引力。使付在工件上的粉末被吹掉,降低上粉率。实验结果表明;当输送空气量为3升/秒时,上粉率百分之就九十五左右,而加大气量时,而输粉空气量每增加一升/秒时,则上粉率降低百分之二到三。
3、施工时打火这个问题一般不存在了,因为高压静电发生器现在大多装有恒压、恒流保护线路。老式喷枪有着个问题。打火原因如下:
(1)枪与工件距离太近和粉末在静电场内浓度大,超过了极限浓度,是重要原因。
(2)内电阻小,导致电流过大。
(3)电压太高:实验证明:场强在1kv/cm时,吸附效率已接近饱和。此后场强再增加三倍,涂覆效率只增加百分之三到五。所以电压太高不可取,反而容易引起打火。一般控制在60kv已够用了。
4、涂层有缩坑:
(1)多数情况是由工件表面不撤底引起,有的是压缩空气中含油引起。因为油点明显影响粉层固化时的表面张力。
(2)粉末涂料的内在应素如混入了不同厂家或批次的粉粒,引入硅尘,也会影响其固化时表面张力的均匀性,造成缩坑。
5、涂层有针孔起泡:涂层下面的气体在烘干过程中到达涂层表面,突破界面者为针孔,来不及排除者为气泡。涂层中的气体可以是空气、水蒸气或氢气(镀锌层中带来的)等。根本解决方法是喷涂前彻底排除气体。小量的无法排除的气体,也可用控制烘干和喷涂条件的方法避免产生针孔或气泡。据计算,排除涂层的空气需要26秒,在除膜开始固化前的安全熔融流平段(100~135℃)升温慢些。给予足够的排气时间。或采取工件预热后喷粉的方法,均有效果。
6、涂层有橘皮:产生橘皮的主要原因来自粉末涂料自身的流平性差。施工也有影响,是属次要因素。
更多关于材料方面、材料腐蚀控制、材料科普等等方面的国内外最新动态,我们网站会不断更新。希望大家一直关注中国腐蚀与防护网http://www.ecorr.org 责任编辑:王元 《中国腐蚀与防护网电子期刊》征订启事
投稿联系:编辑部
电话:010-62313558-806
邮箱:ecorr_org@163.com
中国腐蚀与防护网官方 QQ群:140808414
免责声明:本网站所转载的文字、图片与视频资料版权归原创作者所有,如果涉及侵权,请第一时间联系本网删除。
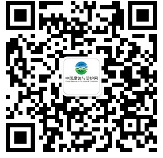
官方微信
《中国腐蚀与防护网电子期刊》征订启事
- 投稿联系:编辑部
- 电话:010-62316606-806
- 邮箱:fsfhzy666@163.com
- 中国腐蚀与防护网官方QQ群:140808414