铝是比较年轻的金属,有“20世纪的金属”之称。在全世界它的年产量仅次于钢铁,在金属材料中名列第二。铝和铝合金之所以得到广泛应用在于它有许多特点。
铝的比重是2.702,与铜(比重8.9)和铁(比重7.9)比较,约为它们的1/3.其制品重量轻,可用于汽车、飞机、铁路车辆、船舶、高层建筑等方面。
纯铝强度低,但在铝中加入少量的铜、镁、锰,锌、硅等元素后形成铝合金,显微硬度可达400~600kg/mm2,特殊情况下可达1200~15Ookg/mm2,强度比碳钢好,可与特殊钢媲美。
铝及其合金在空气中,会在表面自然生成一层极薄的厚达0.01~0.05μm的氧化膜。这层自然氧化膜虽然能阻止它们继续遭到大气腐蚀,但此膜疏松多孔,当遇到工业性气体时,抗蚀性能大大下降。不过,如经电解氧化加工,使其表面生成硬而致密的氧化膜层,那末,很多物质就对它不产生腐蚀作用,适合在工业地区和沿海地区使用。
因铝的延展性极其优良,所以易于加工成型,经人工氧化染色后,可以得到各种美丽颜色的铝制品。随着铝及其合金表面防护装饰性氧化工艺的广泛应用,近年来氧化新工艺、新技术的不断出现,如仿礼花法,转移印花法、渗透法、冰花图案法等等,使铝表面更加呈现出色彩缤纷,繁花似锦,见之令人畅心悦目。所以目前建筑行业上把其大量用于高级宾馆的门、窗、柱、框架等制件上,既坚实牢固,又美观大方。
由于铝及其合金还有良好的导热、导电性,对光、热、电波的反射性好,没有磁性,耐低温和化学药品,有吸音性……等等。故它的应用越来越广泛。
为了保证铝合金有足够的强度和较高的耐蚀,必须经过氧化处理。
铝和铝合金的氧化处理分为化学氧化和电化学氧化。化学氧化不用外来电流仅把制件置入适当的溶液内,使表面生成一层氧化膜。在电化学氧化中是把铝及其合金作为阳极,故又称阳极氧化。
电化学氧化的方法较多,本章分别介绍硫酸、铬酸阳极氧化,硬质电化学氧化绝缘电体学氧化和瓷质电化学氧化的故障及其处理方法。
硫酸电化学氧化故障及其处理方法
硫酸电化学氧化简称硫酸阳极化,生成的氧化膜色泽视铝材的成分和氧化工艺的不同而异,一般有无色,微黄色、灰色等。氧化膜的厚度约在1~6μm之间。氧化膜可以染色,其防护性能良好,且具有一定的耐压性能。本工艺的缺点是对于翻砂,铆接、焊接等有孔隙类的零件,经硫酸阳极化后,孔隙处容易泛白点,目前尚无办法彻底消除此问题。
一、硫酸电化学氧化工艺简介
1.硅酸电化学氧化液配方和操作条件
硫酸电化学氧化液配方和操作条件如下:
硫酸(比重1.84,CP)(g/l)160~180
温度(℃)15~25
电压(V)12~20
阳极电流密度(A/dm2)1~1.5
时间(min)35~45
2.工艺过程
零件上挂具→化学除油→热水清洗→冷水清洗→出光→清水洗→硫酸阳极氧化→冷水洗→烘干→染色→100℃热水封闭10min。
a.操作注意事项
(1)染色件阳极化时,浓度、温度、电压和电流密度避免用上限,时间应适当延长。
(2)除了染黑色外,需染其他色泽时,零件的材料应使用纯铝、防锈铝LF2和硬铝LY11、LY12。装饰性要求高者最好应使用高纯铝或高纯铝的铝镁合金。
二、故障和处理方法
故障现象1
氧化膜薄或有红色挂灰,抗腐蚀性能差。
原因分析
发生上述故障的原因是多方面的。
(1)硫酸含量和操作条件不符工艺规范
电化学氧化是铝件表面失去电子成为铝离子,然后与阳极上产生的新生氧结合生成氧化膜。氧化过程中在成膜的同时也存在着氧化膜的化学溶解。氧化膜的生成速度随阳极电流密度、电压的增大和溶液浓度、温度的升高而加速,随阳极化时间的延长而减慢。当然,氧化膜的化学溶解速度也随这些因素的增加而加快。氧化膜的生成与溶解是对立的统一体,是相互制约的。因而所定的工艺规范应根据零件的要求,通过实践总结出的最佳参数。
如果电位密度小、电压低、时间短,单位面积上溶解的铝离子便少,生成的氧化膜就较薄。如果溶液的浓度低,溶液中的离子少,溶液的导电率小,要达到同样的电流密度,浓度低的溶液其槽电压比浓度高的槽电压来得高,而硫酸电化学氧化一般是控制电压的,所以当溶液的浓度低时,在规定电压下,电流密度就小,生成的氧化膜也就较薄。溶液的温度低时,溶液的粘度大,离子运动慢,溶液的导电率小,在规定的电压下,电流密度就小,生成的氧化膜当然就薄。反之,氧化膜厚,但氧化膜的溶解也加快,且会形成疏松粉末状的氧化膜。
(2)零件装得太松,夹具与导电棒接触不良
若分析硫酸含量的检查操作条件都符合工艺规范,就应该检查零件的装夹情况。如零件装夹太松,并且已经位移,就会造成导电不良,以致氧化膜薄。
(3)夹具上的旧氧化膜未除尽
若硫酸含量和操作条件符合工艺规范,装夹也正常,此时就应仔细检查夹具,如夹具上的旧氧化膜未除尽,则零件装夹在有薄层氧化膜的夹具上导电不良,氧化膜生成速度变慢而使得氧化膜薄。
(4)氧化液中含铜离子过高
处理方法
对于原因1,操作者必须严格控制工艺规范。
对于原因2,解决方法是退除氧化膜,重新阳极化,不过此法对光洁度有一定影响。如果零件有精度要求,可在非工作面上边装夹,边用夹具轻轻擦去零件上的氧化膜,使夹具装夹在擦除氧化膜的部位,然后进行补氧化。
对于原因3,可将零件拆卸下来,退除净夹具上的氧化膜和零件上的氧化膜,或用夹具擦去装夹处的氧化膜,重新进行氧化,使得到正常的氧化膜。
对于原因4,只有更新电解液才能消除弊病。
故障现象2
氧化膜疏松有粉末状。
原因分析
产生疏松氧化膜的原因有两点:
(1)工艺规范控制不当
前面已经指出,在氧化过程中氧化膜的形成和溶解是同时进行的,氧化膜的化学溶解会造成氧化膜的疏松,甚至产生疏松粉末状氧化膜。氧化膜的溶解速度与溶液的温度影响较大,它随溶液温度的升高而加速。另外氧化时间长,溶液浓度浓,也会产生疏松氧化膜。电流密度过大或电压过高时,产生的焦耳热使零件发热,导致零件周围的溶液温度升高,加快氧化膜的化学溶解,造成氧化膜疏松,或产生粉末状氧化膜。所以,严格控制工艺规范是防止氧化膜疏松的重要因素。
(2)加硫酸后溶液不均匀
同槽阳极化的零件,有的氧化膜太薄,有的氧化膜已经疏松有粉末状。这种故障一般出现在加硫酸后,这是硫酸在溶液中分布不均匀所引起的。
处理方法
严格按工艺规范操作。加硫酸后通入压缩生气的充分搅拌,并进行通电处理故障即可消除。
故障现象3
氧化后染黑色产生发红或发蓝。
原因分析
氧化后染黑色出现发红或发蓝的原因有以下两个方面:
(1)氧化膜吸附性能不良
用酸性黑ATT染料染黑色时,会出现发红发蓝的故障。酸性黑ATT染料是以70%的酸性蓝黑10B和30%的酸性橙Ⅱ的分子结构组成,所以当氧化膜的孔隙小,吸收性能差时,分子小的酸性橙Ⅱ容易被氧化膜吸收,膜层中的酸性橙Ⅱ超过染料的比例,所以色泽发红。遇到这种情况,可适当延长阳极化时间,使氧化膜孔隙增大,以便分子大的酸性蓝黑10B能顺利被氧化膜吸收,膜层中的染料合乎比例,染出的色泽就黑了。
对板材和挤压零件,阳极化前应将零件进行碱腐蚀除去表面硬皮,才能得到均匀的黑色,否则会得到发红或发花的黑色。
含硅量高的零件,可在40~50ml/l硝酸和10ml/l左右的氢氟酸溶液中浸渍20s左右以溶解杂质,使表面留下一薄层较纯的铝,改善氧化膜性能,使它具有好的吸附性能,得到均匀的黑色。
(2)染色溶液的pH值不当
染色溶液的pH值对染色的影响比较大,因为各种染料的吸收性能有各自不同的pH值。例如pH接近7时,酸性蓝黑10B的吸附性能好,而酸性橙Ⅱ的吸附性能比较差,所以色泽偏蓝,pH4.5左右时,酸性蓝黑10B的吸附能力差,酸性橙Ⅱ的吸附能力强,故色泽就偏红。所以,在染色时pH应避开7或4.5左右的值,—般控制在3.6左右或5~6比较好。
故障现象4
有时生产中出现零件局部无氧化膜。
原因分析
(1)装夹位置不当
由于装夹位置不当,阳极化时氧气跑不出来滞留在局部表面上,造成闷气而无氧化膜。装夹时应注意选择适当位置,使零件的凹面向上或向上倾斜,这样就可以避免无氧化膜的故障。
(2)零件表面有附着物
阳极化前零件表面如有胶纸等透明粘性物质时,阳极化时又没有脱落,在封闭时却脱落了下来,结果在吸附物处就没有氧化膜,操作者在前处理时应注意除去这类物质。
(3)氧化液成分太稀
溶液成分太稀,局部电流太小处就无氧化膜,分析并提高硫酸浓度,故障即消除。
更多关于材料方面、材料腐蚀控制、材料科普等等方面的国内外最新动态,我们网站会不断更新。希望大家一直关注中国腐蚀与防护网http://www.ecorr.org
责任编辑:庞雪洁
《中国腐蚀与防护网电子期刊》征订启事
投稿联系:编辑部
电话:010-62313558-806
邮箱:ecorr_org@163.com
中国腐蚀与防护网官方 QQ群:140808414
免责声明:本网站所转载的文字、图片与视频资料版权归原创作者所有,如果涉及侵权,请第一时间联系本网删除。
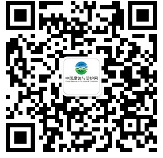
官方微信
《腐蚀与防护网电子期刊》征订启事
- 投稿联系:编辑部
- 电话:010-62316606-806
- 邮箱:fsfhzy666@163.com
- 腐蚀与防护网官方QQ群:140808414