设备制造质量的优劣及设备制造工艺是否优化,都涉及到设备的使用寿命问题。本文就石化核电等静设备中空冷器、换热器和压力容器在制造和使用中突出的非正常腐蚀失效的案例进行了简要概述。
文| 束润涛 武汉市润之达石化设备有限公司
据中国青年网财经报道,某企业PX 项目爆炸起火,起因源于管理不善等诸多人祸因素。目前,部分石化企业为节约成本,采取最低价格中标的方式给石化装置的正常运行带来了很大的安全隐患。由偷工减料所涉及到的质量问题五花八门, 如新疆某石化企业采购的DN2000 不锈钢固定管板式换热器,使用周期仅3 个多月,经拆卸后发现管束壳程的8 块不锈钢支撑板全部没装;四川某企业采购的08Cr2AlMo 石油液化气空冷器使用仅2 个多月就发生严重泄漏,给安全生产带来巨大隐患。石化、核电等行业对于设备使用前的检验验收都有严格的规范和要求,但由于部分石化企业管理不善,或简单强调节约采购成本,而忽略了对产品质量的严格要求,特别是一些财团或地方企业跨界投资的新上化工项目,这种情况尤为突出。同时,我国石化装备制造业近几年发展迅猛,许多石化设备企业或故意以劣充优, 或技术水平低下,造成了很多设备非正常失效的案例,给石化企业的正常生产带来极大困扰和巨大的安全隐患。以下是几起与制造质量和制造工艺相关的非正常腐蚀失效的典型案例,以及一些与制造和材料相关的其它问题整理出来与大家一起学习和探讨。
空冷器管束非正常腐蚀失效的典型案例
空冷器粗制滥造的典型案例
本案例为表面蒸发式空冷器上段的翅片管管束,管内为液化石油气,介质中含硫化氢和氢气,在气体冷却过程中经过露点温度,设备处于湿硫化氢腐蚀环境,选用的翅片管基材为耐硫化氢腐蚀的08Cr2AlMo,管箱为Q245R,接管、法兰为20#。该设备使用仅2 个月就陆续发现6 支翅片管的端部泄漏,由于介质易燃易爆,被迫停止使用(见图1), 并重新采购。
图1 空冷器管箱内部偷工减料焊接结构图例
图1 为空冷器管箱内部结构,图示标注1 为插管与管箱侧板的内部焊接接口, 未焊接;标注2 为翅片管管头与管板焊接接口,未焊接;标注3 为管箱底板与管板连接处,未见封底焊缝;标注4 为底板与丝堵板连接处,未见封底焊缝。
该空冷器管箱焊缝外表比较美观,但管箱内部所有焊缝都未按要求封底,目的是节省工时、节省焊接材料,并降低焊接能耗。
在该产品制造企业提供的竣工资料中, 未见任何焊接工艺和热处理资料,其加工制造成本不及合格产品的一半,属于典型的粗制滥造产品。
不合理的制造工艺给高压空冷器带来非正常腐蚀失效的案例
中石化某石化分公司加氢装置4 台高压碳钢空冷器使用仅几天就有3 台泄漏, 由于使用部位存在易燃易爆的安全隐患, 该部位的4 台高压空冷器被迫废弃后重新采购,其停工损失高达2000 多万元。
经追踪分析,制造厂在高压空冷器组装工艺的前后顺序方面存在有很大偏差。目前国内外许多高压空冷器的图纸要求大多都是先做管箱,后进行管头焊的焊接, 其目的是保证高压空冷器管箱的绝对安全。先焊管箱后焊管头焊的工艺顺序忽略了采用管箱深孔焊焊接的管头焊缝拉脱力很差的事实,而且不能对管头焊进行PT 检查和煤油渗漏检查,只能在水压试验或气压试验时寻找泄漏点。发现缺陷后也不能进行挖补(挖除缺陷再补焊),解决方法也只能在有缺陷的部位进行重新堆焊。在缺陷没有被彻底挖除的情况下,在焊缝表面加盖焊缝是存在巨大安全隐患的。
相同的案例在国内已发生多起,国家某行业管理机构明确要求制造企业在空冷器的制造上按先管箱后管头的工艺顺序进行制造,目前大多数空冷器制造企业都遵守这一规定予以执行,这是导致问题频发的原因之一。须知国内企业在深孔焊方面的焊接技术和检验方法都没有成熟可靠的技术,制造及检验过程也没有严格的控制措施。管头焊接质量的绝对可靠是保证石化企业获得生产稳定的保障,管箱的焊接质量是保证石化企业设备安全运行的前提, 二者不可孰轻孰重。其实,先焊接管板管头, 后焊接管箱的制造方案早已获得非常稳定的运行效果,对于管箱的焊接检验和焊后热处理目前都有可靠的手段来予以保证, 管箱的各种焊缝质量都可以采用UT 检验的方式来进行检验,焊后热处理可以采用炉外局部热处理的方法完成。
以下是空冷器管头焊缝的图例说明:
图2 空冷器管头深孔焊焊接图例
图3 空冷器管子-管板焊接接头PT检验图例
图2 是将管箱预制好以后再进行深孔焊接的制造工艺,图3 是先焊接管板管头, 进行PT 检验的图示。图2 的焊接方式等同于盲焊,焊后无法进行直接检验,焊接缺陷也无法挖补,而图3 的焊接及焊后检验就不存在图2 那样的所有问题。
换热器管束非正常腐蚀失效案例
不锈钢U型管的腐蚀案例
本案例中U 型管不锈钢换热器管束的腐蚀问题来源于海川化工论坛,壳程介质中不含Cl-,含有溶剂乙酸乙酯和溶质有机物,管内通蒸汽加热,使用周期大约一年。
从图4 判断,该换热管的R 段有拼接痕迹(见图4 中的蓝色标记),GB151 仅允许在U 型管的直管段进行拼接,在R 段拼接属于违规制造。小口经管对接焊缝的可靠性不高,应直接采购整支换热管进行弯制。
图4 换热器U型管R部位拼接图例
U 型管在拼接后会产生焊接残余应力,而弯制过程又将焊接残余应力与弯曲形变应力叠加。材料在弯制时会延纤维方向拉伸,使管子靠R 外侧的壁厚形成拉伸减薄,在管材进行弯制时就可能已经在焊缝处产生了微缺陷,这是使用寿命很短的主要原因。
图5 换热器U型管腐蚀失效后的PT检验图例
图5 是另一台U 型管加氢换热器管束腐蚀失效后的PT 检验照片,从照片上可以看到很多横向裂纹,是典型的应力腐蚀特征。
普通奥氏体不锈钢材料中都含有少量铁素体,部分条形铁素体会在纤维拉伸的作用下断裂,形成微小空洞。本人在其它科研项目中对304L 的焊接弯曲试样进行微观分析时发现,条形铁素体断裂的最大空洞尺寸约30μm。所以,对于U 型管应进行固溶热处理以恢复材料的组织性能。很多制造企业由于条件有限而不做固溶热处理,导致很多U 型管R 段在应力腐蚀介质的作用下腐蚀失效。U 型管冷弯后进行整体固溶热处理处理或在R 段做局部固溶热处理,按国内现有技术能力都是可以实现的,这样既可以完全消除弯曲应力,又能将铁素体重新固溶,起到修复微缺陷的作用。
管束管头焊接质量问题
本案例为某地方炼油企业原料油- 减一线换热器,换热管材质08Cr2AlMo,管板16Mn 锻,使用4 个月以后开始泄漏,后经过3 次堵管,使用11 个月后报废(见图6)。08Cr2AlMo 换热器管束在该部位的正常使用寿命应该超过3 年。
图6 08Cr2AlMo换热器管束非正常腐蚀图例
该设备壳程介质原料油,温度65~ 85 ℃,管程介质为减压塔顶油气,温度130~100℃,管程为湿硫化氢腐蚀环境。壳程管外基本无腐蚀痕迹,管程换热管、管板和焊缝金属仅见轻微腐蚀痕迹,泄漏点均出现在管口焊缝的熔合区。经分析, 腐蚀原因如下:
(1) 材质不匹配:08Cr2AlMo, 管板16Mn 锻,焊材H08CrMoA;
(2) 焊接质量很差:焊缝高度明显不够,不满足图纸和GB151 要求。
很多制造企业的焊接工程师不知道08Cr2AlMo 其实就是有淬硬倾向的Cr-Mo 钢,这种淬硬倾向在北方的冬天尤为明显, 必须按焊前预热、焊后消氢和最终回火热处理工艺来进行严格制造和过程控制。对于预热、后热和热处理,很多企业把关不严,或不知道该怎么做,就干脆不做,这是该材质换热器管束使用寿命很短的直接原因。
压力容器非正常失效的案例
奥氏体不锈钢容器非正常失效案例
奥氏体不锈钢与碳钢和低合金钢相比,具有热膨胀系数大,热导率低的特点。由于冷却速度慢,奥氏体不锈钢设备在焊接时会导致焊缝收缩量大和焊接应力大, 在焊接过程中应严格控制线能量,并对设备本体进行有效防护。设备在焊接时若不对母材进行保护,而任由飞溅和焊瘤与母材熔为一体,这将使局部产生冷却收缩应力,极易造成点腐蚀,以及由点腐蚀源所造成的应力腐蚀破坏。如某化工企业一台316L 材质的环己烷污水分离器,使用1 年后就发生腐蚀泄漏,而原污水分离器在使用304L 的情况下正常运行时间都超过2 年。检修时在罐内发现了大量焊瘤和飞溅痕迹, 在焊瘤和飞溅部位,均可用肉眼看到腐蚀坑点(见图7)。在该设备物料介质中, 仅有极少量乙酸和氯离子,在入口处的氯离子含量仅2~5ppm,由于随意起弧的焊瘤和飞溅给氯离子的聚集创造了条件,在污泥沉积后便形成由点腐蚀源构成的应力腐蚀破坏。
该设备仅在焊缝粗制滥造部位出现腐蚀泄漏,其余部位均未发现任何腐蚀痕迹, 如果能严格按工艺要求控制焊接过程,该设备在氯离子含量很低的情况下,其使用寿命将大大延长。图7 是该设备随意起弧以及焊瘤腐蚀后的凹坑痕迹。
图7 环己烷污水分离器脱水包与筒体焊缝野蛮焊接痕迹
低合金碳钢容器内壁的非正常裂纹
本案例为某核电厂还没有投入使用的除氧器,按ASME Ⅷ-1 卷进行制造,材质为SA516-G70,化学成分和机械性能相当于Q345R,厚度38mm。设备到现场后经检验发现容器内壁有一处裂纹,见图8。
图8 核电站除氧器筒体内部缺陷
经UT 检测, 发现缺陷深度最大约11mm。该缺陷发现后现场检验人员认为是母材质量问题,但裂纹周边椭圆形痕迹与母材明显不同,椭圆长宽尺寸大约35×20mm,经判断裂纹周边椭圆形痕迹内的金属为焊缝。该问题产生的原因无资料可追踪,分析为铆工在装配时损伤了母材, 害怕被追责,而没有按质保程序进行处理, 在没有焊接工艺指导的情况下进行了私自补焊。缺陷挖补的焊接难度远远大于一般普通正常焊缝的焊接技能,没有压力容器焊接证书的铆工是不可能完美完成焊接修补的。从宏观可以判断,该缺陷是由夹渣引起的裂纹。说到底,是铆工想蒙混过关。对于核电设备的制造,比一般石化压力容器的过程控制应更为严格,说明该设备制造企业的质保培训被走了过场,铆工质量意识薄弱。
本文之所以把这个案例拿出来与大家分享,是因为核电设备在使用前的检验非常严格,从而可以避免在使用过程中发生非正常失效。石化企业的设备验收一般以水压试验和质量证明文件为依据,基本没有对罐体内壁进行检验。该案例中出现的质量问题在石化企业大量存在,只有加强使用前的严格检验才有可能将非正常失效的安全危害降到最低。
其它与腐蚀相关的制造问题探讨
关于换热器管束的胀接问题
换热器管束的腐蚀泄漏不仅仅发生在管头焊缝,许多胀接过的换热管也有腐蚀泄漏的情况。普通奥氏体不锈钢、双相不锈钢, 以及15CrMo、12CrMo 的换热管都有许多在胀接部位存在非正常腐蚀泄漏的案例,如大连石化在2000 年投入几台SAF2205 的双相不锈钢管束使用不到3 个月就发生多支换热管穿孔,其穿孔部位均位于离管口15~20mm 处。还有许多企业也都有过奥氏体不锈钢换热管在胀接部位发生腐蚀泄漏的事故(见图9)。由于泄漏点发生在离管头焊缝较近的管子母材上, 责任的划定往往由制造企业和管材生产企业担责,很多制造企业都被当成了冤大头。
德国巴斯夫公司在WN75-100 的企业标准中规定,当管子内外有腐蚀及应力腐蚀介质时,不推荐采用机械或其它方式胀管。北京钢铁研究总院的陆世英教授曾经做过试验,发现321 不锈钢材料的换热管贴胀以后胀接变形台阶处的残余应力超过100MPa。奥氏体不锈钢在冷作变形过程中屈服强度会迅速上升,冷作硬化极其明显, 是构成应力腐蚀的直接原因。双相不锈钢中的奥氏体只有50% 左右,在冷变形中不稳定的奥氏体会转变为马氏体,是造成胀接部位腐蚀穿孔的主要原因。铬钼钢塑性较低,淬硬倾向明显,胀接后在台阶处的附加应力很大,将会使胀接部位变脆。
奥氏体不锈钢在胀接部位的腐蚀特征为微裂纹,双相不锈钢在胀接部位的腐蚀特征则主要为腐蚀穿孔,裂纹较少,而铬钼钢在胀接部位的腐蚀特征主要为穿孔。因此,本人建议在所有存在氯离子及其它卤素介质的应力腐蚀环境中,奥氏体不锈钢、双相不锈钢和铬钼钢换热管都不进行任何形式的胀接,应以强度焊为主。
以下图例中,图9 是304 不锈钢管束试压时管内喷雾的图片,图10 是15CrMo 合金钢管束试压时管内喷水的图片。
图9 304不锈钢管束胀接部位泄漏图例
图10 15CrMo管束胀接部位泄漏图例
从图9 和图10 的试压照片可以看出, 304 不锈钢的水雾和15CrMo 的水柱都是从离管端很近的管内喷出来的,都是材料胀接以后的不适应性影响。胀接的目的是防止壳程管板管孔与管子外壁发生缝隙腐蚀, 但忽略了不同材质的换热管在形变应力条件下的不适应性,这种不适应性将使管束使用寿命大大缩短。当缝隙腐蚀与胀接的不适应性发生冲突时,应以两权相害取其轻来考虑。
奥氏体不锈钢管件、膨胀节和封头的非正常腐蚀失效
奥氏体不锈钢管件和膨胀节在实际使用过程中出现大量腐蚀失效的案例。与前述U 型管冷作变形的原理一样,管件和膨胀节在制造过程中的变形量都很大,只有固溶处理才能彻底消除形变应力和微观缺陷,但大多数管件制造企业以高温拔制或高温推制代替了固溶热处理。在国家相关标准中, 奥氏体不锈钢膨胀节和封头都没有固溶热处理的强制要求,所有制造企业在部件制造完成后都不做固溶热处理,这是造成应力腐蚀的主要症结所在。如果使用单位的工况介质中有硫化氢和氯离子等腐蚀介质, 建议在采购技术条件中对不锈钢管件、膨胀节和封头提出固溶热处理的强制要求。
图11 大型筒体膨胀节翻边边缘出现应力裂纹以后的补焊图片
图11 是膨胀节出现应力裂纹后补焊的图片,裂纹出现在膨胀节翻遍的焊缝附近, 为形变应力与焊接应力叠加后出现的应力腐蚀失效。图中圆孔是维修焊接前为阻止裂纹延伸的人工孔。
以上案例和探讨的内容是国内空冷器、换热器、压力容器等静设备在制造和使用管理上的一些共性问题,希望引起制造企业、使用单位以及行业管理部门的高度重视。国内压力容器制造企业几千家,绝大多数是中小企业,在此也衷心希望国内中小型压力容器制造企业能够真正从技术管理水平和质量档次上强大起来。
责任编辑:班英飞
《中国腐蚀与防护网电子期刊》征订启事
投稿联系:编辑部
电话:010-82387968
邮箱:ecorr_org@163.com
中国腐蚀与防护网官方 QQ群:140808414
注:本稿为中国腐蚀与防护网版权所有,未经允许, 严禁用于商业用途。转载时请务必以超链接形式标明文章原始出处和作者信息及本版权声明。
免责声明:本网站所转载的文字、图片与视频资料版权归原创作者所有,如果涉及侵权,请第一时间联系本网删除。
-
标签: 石化核
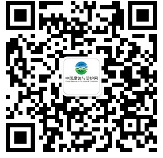
官方微信
《腐蚀与防护网电子期刊》征订启事
- 投稿联系:编辑部
- 电话:010-62316606-806
- 邮箱:fsfhzy666@163.com
- 腐蚀与防护网官方QQ群:140808414