导读:本文研究了Si改性奥氏体不锈钢在550◦C时效至3000 h时,邻近δ-铁素体的奥氏体分解行为及其对冲击韧性的影响。热时效过程中,邻近δ-铁素体的奥氏体分解顺序如下:(1)发生γ→M23C6+α转变。M23C6次生碳化物的优先形成不仅将Si原子排斥到周围的奥氏体中,而且产生了一个贫c区。(2) M23C6次生碳化物的生长导致Ni和Si原子不断被排斥在M23C6/γ和M23C6/α界面中,Ni和Si之间强烈的相互吸引作用为M6C碳化物和g相的形核提供了化学驱动力。(3)随着时效时间的延长,分解奥氏体边界的低C、高Ni、高Si浓度会促进M6C碳化物的优先析出,而M23C6碳化物的优先析出。在冲击变形过程中,次生M23C6与α-铁素体之间由于应变不相容而产生微裂纹,导致冲击韧性略有下降。
AISI 300系列奥氏体不锈钢因其优异的力学性能和良好的成形性,被广泛用作轻水反应堆和第四代核反应堆的结构材料。为了提高在液态金属、超临界水或熔盐等恶劣环境下的耐腐蚀性,硅改性奥氏体不锈钢被开发出来,因为添加硅可以促进氧化保护膜的形成。由于Si是一种强铁素体稳定元素,因此Si的加入会使奥氏体合金不稳定,导致δ-铁素体形成的高倾向性。在大型工业坯料中,由于凝固时间的延长,δ-铁素体的形成是不可避免的冷却速度慢。研究发现较长的凝固时间促进了元素的偏析程度,较低的冷却速度增加了凝固反应的时间,导致180 mm厚AISI 316连铸板坯中δ-铁素体的数量明显增加。此外,Si是负偏析元素,比Cr和Mo具有更高的偏析。
在奥氏体不锈钢中加入Si不仅改变了δ-铁素体的数量,而且改变了δ-铁素体的化学组成。由于Si表现出比Cr更强的铁氧体稳定能力,现有的δ-铁氧体分解机制可能不适用于富Si的δ-铁氧体。迄今为止,Si的加入对δ-铁氧体分解机理的影响尚不清楚。特别地,我们发现Si改性Fe-Cr-Ni奥氏体不锈钢在热时效过程中不发生δ-铁素体分解。相反,在δ-铁素体附近发现了独特的奥氏体分解机制,这与传统的δ-铁素体分解机制形成了显著的对比。
中国科学院大学陈胜虎团队制备了一种Si改性Fe-Cr-Ni奥氏体不锈钢,研究了铸态下δ-铁素体的形成机理。在此基础上,对含有δ-铁素体的铸态试样进行550℃的热时效处理,以揭示δ-铁素体附近奥氏体分解的机理及其对力学性能的影响。同时,比较了Si改性钢与304奥氏体不锈钢在相同时效时间后的δ-铁素体相关分解行为。
相关研究成果以“Austenite decomposition behavior adjacent to δ-ferrite in a Si-modified Fe-Cr-Ni austenitic stainless steel during thermal aging at 550 °C”发表在Acta Materialia上
链接:https://www.sciencedirect.com/science/article/pii/S1359645424003008?via%3Dihub
表1Si改性和304奥氏体不锈钢wt.%的化学成分。
图1(a, b)铸态Si改性钢的OM和(c) SEM图像。
(a)偏振光下的低倍率和(b)高倍率彩色OM图像。
图2(a-d)低倍率和(e-h)高倍率铸态Si改性钢枝晶组织的EPMA显微图。
(a, e)背散射电子(BSE)图像,(b-d, f-h) Cr, Ni和Si元素分布图。
EPMA进一步观察了树突核之间和树突间的元素分布,如图2所示。OM显微图(图1b)和低倍率EPMA显微图(图2a)的综合结果显示,Cr和Si向枝晶间区域偏析,而Ni富集于枝晶核心区域(图2a-d)。可以看出,δ-铁氧体形成于Cr浓度最高的区域。高倍EPMA显微图清楚地显示,δ-铁氧体在树枝晶间区域形成(图2e-h)。在δ铁氧体中观察到Ni的严重耗损和Si的明显富集(图2g和h)。此外,与δ铁氧体内部相比,δ铁氧体周围区域观察到明显的Cr富集(图2f)。
图3铸态试样中δ-铁素体的TEM图像及化学分析。
(a)HAADF图像和相应的Cr和Ni组合的EDS元素映射,所示为δ-铁氧体和初生碳化物M23C6对应的选定电子衍射(SAED)图。
(b)δ-铁素体和奥氏体的EDS线扫描。
图4(a, b) 304和(C -e)Si改性Fe-Cr-Ni奥氏体不锈钢在550◦C时效
(a, C), (b, d) 500 h, (e) 3000 h后的SEM图像。
图5(a, b) Si改性钢时效50 h后分解奥氏体的TEM亮场(BF)图和(c-f)对应的EDS元素图。
(b)中的插图显示了相应的残余奥氏体的SAED模式。
图5为Si改性钢时效50 h后,邻近δ-铁素体的分解奥氏体TEM显微组织。图5(a)的亮场(BF)图像显示,δ-铁氧体周围仍然存在M23C6碳化物,δ-铁氧体没有发生分解。(a)偏振光下的低倍率和(b)高倍率彩色OM图像。采用Cr、Fe、Si和Ni的元素映射,试图利用元素划分来区分新形成的产物(图5b-f)。通过SAED分析(见图5b),可以确认在分解区域中仍然存在黄色箭头所示的残余奥氏体。Cr和Fe的EDS元素映射也表明,残余奥氏体和未分解奥氏体中存在相同的浓度水平。此外,在分解的奥氏体区域,富Cr相和富Fe相共存。Crrich相呈现出精细的棒状形态,如图5(c)中的红色箭头所示。
图6时效50 h后Si改性钢δ-铁素体附近分解组织的TEM图像
(a) BF图像,(b) HAADF图像,(c) Fe和Cr相对应的EDS元素映射图,
(d) α-铁素体、次生M23C6碳化物和残余奥氏体的EDS线扫描图。
(a)和(b)分别显示了α-铁氧体和M23C6碳化物的SAED模式。蓝色箭头表示初级M23C6碳化物,红色箭头表示次生M23C6碳化物。
图7时效50 h后Si改性钢中分解奥氏体推进边界的TEM图像和化学分析。
(a) BF图像和相应的Ni、Si映射,(b) α-铁素体、M23C6次生碳化物和奥氏体的EDS线扫描。
图8时效50 h后Si改性钢中奥氏体、次生M23C6碳化物和α-铁素体的APT分析。
(a) C、Si、Ni、Cr、Mn和Fe原子映射,
(b)选定元素在奥氏体、次生M23C6碳化物和α-铁素体中的相应1D浓度分布图。
图9 TEM图像显示了时效500 h后Si改性钢中分解的奥氏体的宏观形貌。
(a) BF图像,(b-d)对应的Cr, Ni, Fe和Si的EDS映射。
图10时效500 h后Si改性钢中δ-铁素体附近分解组织的TEM图像。
(a)Cr、Ni、Si和Mn的BF图像和相应的EDS元素映射图(图中为M6C碳化物和α-铁素体对应的SAED图),
(b) G/α和G/ M23C6界面的高分辨率TEM图像(图中为G相、M23C6碳化物和α-铁素体对应的快速傅里叶变换图)。红色箭头表示次生M23C6碳化物,黄色箭头表示次生M6C碳化物,粉色箭头表示g相碳化物。
图11时效500 h后Si改性钢中分解奥氏体推进前沿的TEM图像。
(a) BF图像和Cr、Ni组合元素映射图,(b) M23C6/M6C界面HRTEM图像,
(c、d) (b)中M23C6和M6C次生碳化物的放大图像和(e、f)相应的FFT图。
图12时效500 h后Si改性钢的M6C/M23C6界面的APT分析。
(a)C、Si、Cr和Ni原子映射,(b) 等浓度面35% Cr和20% Ni。
(c) (b)中选定元素在M6C/M23C6界面上对应的1D浓度分布图。
图13(a)时效3000 h后Si改性钢中分解奥氏体的STEM图像和(b、c)对应的EDS元素图。
图14时效3000小时后,Si改性钢的α/γ界面上的APT分析。
(a) C、Si、Cr、Ni、Mn和Fe原子映射和(b) (a)中选定元素的相应1D浓度分布图。
图15 Si改性奥氏体不锈钢550℃时效至500 h后的室温冲击能。
图16(a、d)铸态试样和(b、e)时效50 h和(c、f)时效500 h试样冲击后的断口表面。
(d、f)高倍扫描电镜图像。
图17(a)铸态试样和(b)时效50 h、(c)时效500 h试样断口纵断面的SEM图像。
图18(a-c)冲击变形后的TKD结果,
(d)时效500 h后Si改性钢对应的Cr和Ni结合的STEM-EDS元素图。
(a)波段对比(BC)图,(b)相图,(c)核平均取向偏差(KAM)图。
图19(a) δ/γ界面生成初生M23C6碳化物,(b, c) γ→M23C6+ α转变,
(e, f)生成毗邻次生M23C6碳化物的M6C碳化物和g相,
(d)生成孤立M6C碳化物和g相的奥氏体分解机理示意图。
(a, b, d, e)宏观视图和(c, f)对应的(b, e)放大图像。
图20基于理论计算的Si含量对Fe-Cr-Ni奥氏体不锈钢中C扩散率的影响。
图21(a) APT样品制备位置的SEM图像和(b-d)时效50 h后样品中δ-铁素体附近奥氏体的APT分析。
(b) C原子映射和2% C等浓度表面,
(C)等浓度表面为23 %Cr。(d) (c)中二次M23C6碳化物与奥氏体界面的接近直方图。
图22利用thermocalc软件和tcfe8数据库对Si改性奥氏体不锈钢的相变进行热力学计算。(a) 550℃时M23C6碳化物的数量与C含量(基于Fe-x C-17 Cr-7 Ni-5 Si-0.65 Mn (at.%)),
(b) Ni含量(基于Fe-0.5 C-17 Cr-x Ni-5 Si-0.65 Mn (at.%))在δ-铁素体附近的奥氏体中。
免责声明:本网站所转载的文字、图片与视频资料版权归原创作者所有,如果涉及侵权,请第一时间联系本网删除。
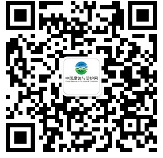
官方微信
《腐蚀与防护网电子期刊》征订启事
- 投稿联系:编辑部
- 电话:010-62316606
- 邮箱:fsfhzy666@163.com
- 腐蚀与防护网官方QQ群:140808414