铝锂合金由于其低密度、良好的耐腐蚀性以及高强度和韧性的结合,在航空航天领域取得了成功的应用。常用的铝锂合金,包括2195、2050、2099和2199,主要通过铸造和锻造加工成薄片和试管。增材制造(AM)铝锂合金在制造仿生结构、晶格结构或其他复杂的功能/结构组件方面显示出巨大的潜力。然而,激光粉末床熔合(LPBF)加工的铝锂合金仍然面临挑战。高能束激光加工会导致铝锂合金产生严重热裂纹以及锂元素的烧蚀。
近日,北京科技大学张百成副教授(通讯作者)等研究人员为了消除铝锂合金中的热裂纹,降低锂元素的烧损,开发了一种用于LPBF工艺的纳米陶瓷颗粒改性的新型铝锂合金。相关工作以 “Effect of lithium anti-ablation and grain refinement introduced by TiC nanoparticles in LPBF Al-Li alloy” 为题发表在《Journal of Materials Research and Technology》上。北京科技大学博士研究生孙金娥为论文第一作者,本工作获得北科大曲选辉教授指导。
熔体池中TiC纳米颗粒有效地提高了铝合金液体的粘度,减少了金属汽化和液体飞溅,从而防止了LBPF过程中Li元素烧蚀。Li含量从打印铝锂合金中的0.87 wt.%,显著提高到打印TiC改性铝锂合金中的1.34 wt. %。此外,在铝锂合金凝固过程中,TiC纳米颗粒作为额外形核质点,促进了柱状晶向等轴晶的转化过程,极大的降低了材料热裂性,实现了全致密铝锂合金制备。在LPBF过程中,在TiC纳米颗粒表面发现了从TiC到Al3Ti的梯度转变反应,原位形成的Al3Ti相显著降低了与Al基体的晶格失配,从而使其具有优异的极限拉伸强度(343 MPa)和伸长率(9.3 %)。TiC纳米颗粒诱导的锂元素抗烧蚀作用为添加剂制造轻质合金提供了一条新的途径。本研究通过调控不同激光功率(140-10-300W)和扫描速度(60 - 400 mm/s)制备了TiC改性的Al-Mg-Li合金,图1 (a)显示了该合金的OM显微图。在扫描速度为320~400 mm/s,激光功率为200~300W时,以及扫描速度为80~400 mm/s,激光功率为140~180W时合金中形成了不规则孔隙,这是由于较低的能量输入导致了不良的熔合。此外,当扫描速度低于80 mm/s,激光功率在200-300W范围内时,可以发现一些大的圆形孔隙,这些可见的冶金缺陷可以解释为过高的能量输入导致轻质元素如Al、Mg和Li的汽化。当激光功率在140~180W范围内,扫描速度在60~240 mm/s范围内时,打印TiC改性的Al-Mg-Li合金呈现几乎全致密状态,如图1 (a)中红色实线框所示。相反,打印的Al-Mg-Li合金在所有激光参数区域均形成了微小的热裂纹,如图1 (b)所示,这在LPBF打印的铝-铜合金中也发现了类似的现象。此外,相应的相对密度结果表明,TiC改性的Al-Mg-Li合金的相对密度高于Al-Mg-Li合金。TiC改性Al-Mg-Li合金在60~240 mm/s扫描速度和140~180W激光功率下的高相对密度为99.6 %,而Al-Mg-Li合金应用工艺参数下的最高相对密度为96.1 %,这是由于严重的裂纹形成所致。因此,TiC改性Al-Mg-Li合金在宽工艺参数窗口下具有良好的LPBF打印性和有效的抗裂性。
图1 不同激光功率和扫描速度下制备的(a)合金和(b)TiC纳米颗粒改性Al-Mg-Li合金的光学显微图和相对密度
采用ICP-OES研究了相同激光加工参数(扫描速度为240 mm/s,激光功率为140 W)下不同状态Al-Mg-Li合金中Li元素的含量,如图2所示。结果表明,打印的TiC改性Al-Mg-Li合金的锂含量与原料粉相似。而打印的Al-Mg-Li合金中的锂含量显著降低到0.87 wt.%。这是因为Li元素(342℃)的沸点比其他元素的沸点低很多,导致了高能激光束处理中Li的烧蚀。显然,与Al-Mg-Li合金粉末和TiC改性Al-Mg-Li合金粉末中的锂含量(1.4 wt.%)相比,TiC显著降低了Al-Mg-Li合金中Li的损失率,降低了56.5 %,明显低于任何LPBF加工铝锂合金的研究[13-15]。因此,纳米陶瓷颗粒改性是防止LPBF过程中锂元素损失的有效方法。
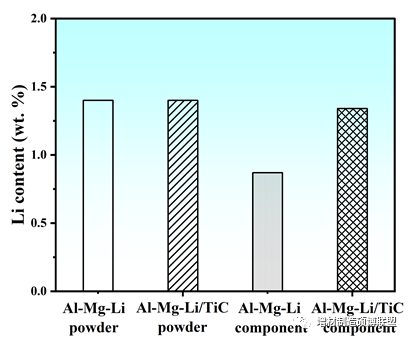
图2 Al-Mg-Li合金粉末、TiC纳米颗粒改性Al-Mg-Li合金粉末、LPBF打印Al-Mg-Li合金和TiC纳米颗粒改性Al-Mg-Li合金中的Li含量选择240mm/s的LPBF扫描速度和140W激光功率下制备的Al-Mg-Li合金和TiC改性Al-Mg-Li合金试样进行扫描电镜和EBSD表征,典型的扫描电镜和EBSD微观结构特征如图3所示。如图3 (a)所示,Al-Mg-Li合金呈现出LPBF打印铝合金的典型熔体池(MP)形态,即沿建筑方向(BD)的“扇形”形态。注意到,由于LPBF过程中热梯度与凝固速率的比值较高,MP内的微观结构均由粗长的柱状晶粒组成,如图3 (b)所示。如图3 (c)所示,LPBF打印的Al-Mg-Li合金由具有<001>优先生长取向的柱状晶粒组成。此外,柱状晶间处可见热裂纹。相反,TiC改性Al-Mg-Li合金的微观结构表现为随机取向的全等轴晶粒,如图3(d-f)所示。这表明TiC纳米颗粒的加入有效地消除了热裂纹,并对Al-Mg-Li合金的柱状向等轴晶粒转变起到了关键作用。
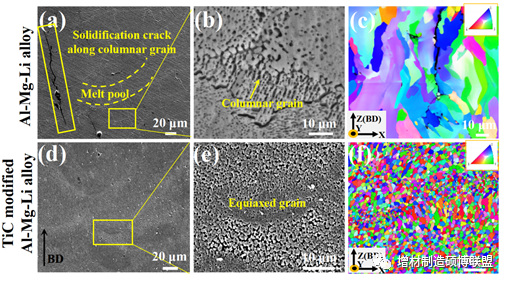
图3 LPBF打印的(a-c)Al-Mg-Li合金和(d-f)TiC纳米颗粒改性的Al-Mg-Li合金的扫描电镜图像和EBSD IPF图像据统计,柱状晶粒的平均粒径为173 ±34µm(图4 (a)),说明柱状晶粒在多层上沿BD外延生长(层厚设为30µm)。等轴晶粒的平均粒径约为1.5 ±0.9 μm,比打印的Al-Mg-Li合金细化了两个数量级,如图4 (b)所示。根据Liu等[22]和Qu等[24]的文献,在TiC纳米颗粒增强Al-Mg-Cu合金和6061合金中也发现了类似的晶粒细化现象,但这些合金的粒径在2.22μm~10.6μm之间,大于本研究中获得的1.5 μm的晶粒尺寸。这种期望的全等轴晶粒微观结构与Sc或Zr改性LPBF Al合金[29]中发现的等轴/柱状双峰结构有显著的区别,具有显著的力学性能。
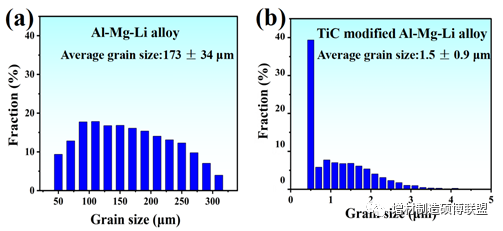
图4 打印的(a)Al-Mg-Li合金和(b) TiC改性Al-Mg-Li合金的粒径分布图5显示了描述材料内部微观弹性应变的平均取向偏差(KAM)图。在LPBF打印的Al-Mg-Li合金中,应变沿低角度取向偏差的柱状晶界集中,如图5 (a)和(c)所示。而打印的TiC改性Al-Mg-Li合金的KAM图像应变分布均匀,平均局部取向偏差略有下降(图5 (b)和(d))。结果表明,TiC纳米颗粒的加入显著降低了Al-Mg-Li合金的残余应力。
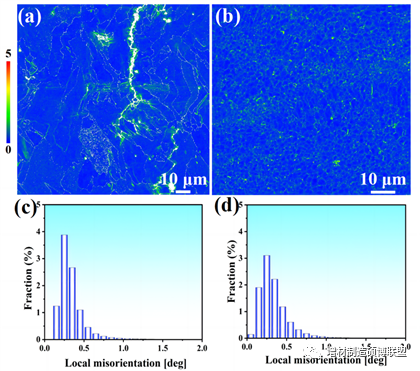
图5(a、c)Al-Mg-Li合金和(b、d) TiC改性Al-Mg-Li合金的KAM图和局部取向偏差分布通过透射电镜分析研究了TiC改性的Al-Mg-Li合金的微观结构和相演化,结果如图6所示。如图6 (a)所示,在TiC改性的Al-Mg-Li合金中,清晰可见尺寸为1-2 μm的精细等轴晶粒结构,与SEM和EBSD结果一致(图4 (e)和(f))。观察到一些明亮的立方沉淀物,尺寸为260 nm。根据图6 (a)对应的STEM-EDX结果,立方沉淀物在Ti和Al中富集。图6 (b)中的SAED图样分析证实,立方沉淀物为Al3Ti,具有L12超晶格结构。根据沉淀相统计,Al3Ti相分数为43.4%。Xia等人[17]研究报道,在LPBF(~106 K/s)的超高冷却速率下,在LPBF过程中加入TiC纳米颗粒会导致亚稳态L12-Al3Ti相的形成。L12-Al3Ti相分布在等轴晶粒内,其平均尺寸约为240 nm,这与我们的研究结果是一致的。此外,α-Al/Al3Ti界面的HRTEM图像显示,Al3Ti相的晶格失配为0.84%(失配定义为(dAl3Ti-dAl)/dAl3Ti),如图6 (c)中黄色框区域对应的(d)所示。
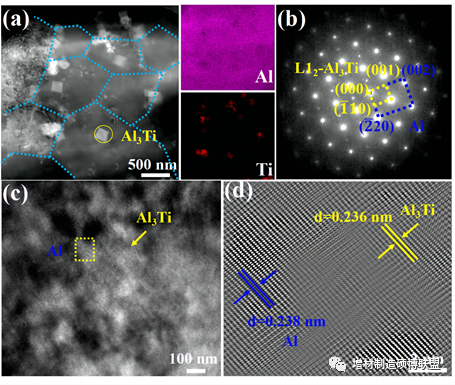
图6 TiC改性的Al-Mg-Li合金的TEM图:(a)高角环形暗场(HAADF)图像和EDX元素映射;(b) Al3Ti的SAED图;(c) Al3Ti的HRTEM图像;(d) (c)中黄色区域对应的α-Al/Al3Ti界面的HRTEM图像聚焦于晶界上板状粒子的高倍透射电镜图像如图7 (a)所示。图7 (b)中相应的SAED图显示该粒子是由Al3Ti和TiC相组成的复合结构。根据EDX图和图7 (c)中的横截面线扫描结果,元素在粒子中的分布表明,Al和Ti元素由内到外产生了明显的扩散现象。另外,通过对图7 (a)中A区域的高分辨率透射电镜图像分析,在α-Al基质(200)和TiC(111)之间有一个厚度为6 nm的Al3Ti(111)中间层,如图7 (d)所示。Al3Ti中间层的存在表明在LPBF过程中,TiC纳米颗粒表面发生了TiC与Al3Ti的反应。同时,在Al基体中,TiC与Al3Ti的晶格错配(晶格错配为6.9 %)可以显著减少原TiC与Al基体的晶格错配(18.8%)。此外,有趣的是,在粒子中心发现了明显的堆积断层(SFs),这可能是由于Al3Ti相在TiC纳米颗粒上外延生长所致[31-33],如图7 (a)中B区域对应的图7 (e)所示。
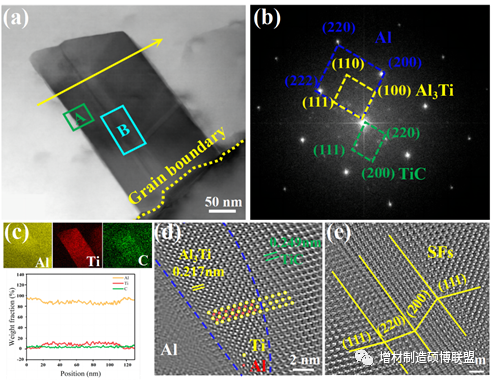
图7 (a)TiC的高角环形暗场(HAADF)图;(b)相应的SAED图;(c)相应的EDX元素映射和TiC纳米颗粒上的元素分布;(d) (a)中A区TiC-Al界面的高分辨率透射电镜图;(e) (a)中B区SFs的HRTEM图LPBF加工过的Al-Mg-Li合金和TiC改性的Al-Mg-Li合金的力学性能如图8所示。如图8(a)所示,由于热裂纹的存在,LPBF加工的Al-Mg-Li合金的极限抗拉强度(UTS)为63 ± 4 MPa,屈服强度(YS)为56 ± 3 MPa,延伸率为1.3 % ± 0.2 %。而TiC改性的Al-Mg-Li合金的UTS显著高于343 ± 6 MPa,YS为340 ± 6 MPa,延伸率为9.3 ± 1.6 %。TiC改性Al-Mg-Li合金的强度和延伸率分别比Al-Mg-Li合金提高了约440 %和610 %。在TiC改性的Al-Mg-Li合金的加工硬化速率曲线中出现了连续的应变硬化转变,这与均匀塑性区域的不稳定性相吻合,如图8(b)中可见的锯齿所示,这可以归因于明显的柱状到等轴晶粒转变引起的位错和大晶界密度之间的高相互作用。在TiC纳米颗粒上原位形成的Al3Ti层进一步改善了晶格结构,实现了良好的伸长率和SFs的形成诱导的加工硬化。值得注意的是,TiC改性的Al-Mg-Li合金的比强度优于之前报道的AM制造的Al-Li合金[15, 34-37],如图8 (c)所示。TiC纳米颗粒对Al-Mg-Li合金的改性为在LPBF过程中开发具有较高比强度、较高锂含量的Al-Mg-Li合金提供了广阔的机会空间。
图8 LPBF加工的Al-Mg-Li合金和TiC改性Al-Mg-Li合金的(a)应力-应变曲线和(b)加工硬化率曲线;TiC改性Al-Mg-Li合金与之前报道的其他铝锂合金的比强度比较
如图3中的ICP-OES结果所示,在Al-Mg-Li合金中加入TiC纳米颗粒显著降低了Li的损失率。由于Li元素(342℃)的沸点远低于Al(2327℃),致使Li元素在Al-Mg-Li合金的高能激光加工过程中容易蒸发,最终造成Li元素的烧蚀。因此,Li元素的损失主要发生在金属汽化过程中。在本研究中,加入TiC纳米颗粒可以显著提高铝合金液体的粘度[24]。由于粘度的增加,所产生的粘性应力需要更少的液体表面变形来平衡反冲压力。反冲压力是由蒸汽射流推动熔体表面向下形成蒸汽凹陷而产生的。因此,铝合金液体粘度的增加抑制了金属的汽化。因此,Li含量在熔体池中得到了很好的固结。另一方面,蒸汽喷射流的高速向上的蒸汽流将液滴喷射出去,形成液体飞溅[38]。如图9 (a)和(b)所示,TiC改性的Al-Mg-Li合金的液体溅射明显降低。液体飞溅通常是指金属蒸汽凹陷边缘周围熔体池的液体破裂。液体破裂是由流体动量引起的惯性压力克服了表面张力引起的毛细管压力引起的,类似于水的飞溅[39]。随着金属汽化量的降低,液体动量突然增加的驱动力也减小。因此,由液体破裂产生的液体飞溅显著减少。此外,当激光熔化粉末时,液滴表面的纳米颗粒也会产生毛细管压力势垒。这种毛细管压力势垒能够在液滴碰撞时阻碍液滴的聚结。毛细管压力势垒可以用以下公式[40]来估计:
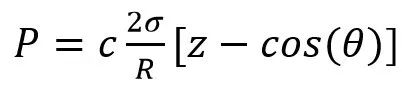
其中σ为液体铝表面张力的(1100 mNm-1),R为颗粒半径,θ为铝在TiC上的接触角,取51°[41],c为与飞溅表面纳米颗粒覆盖分数的相关常数(θ<90°,z为2.73),z为与两个液体飞溅表面之间纳米颗粒数相关的常数(θ<90°,z为0.633)。LPBF制备的TiC改性Al-Mg-Li合金的毛细管压力势垒为1.2 MPa,明显比5.7×10-2MPa的惯性压力高2个数量级,即从熔融温度到526 K以上促进熔融直接液液接触的动能,如图9 (c)所示。结果表明,这种高压屏障足以防止碰撞过程中液滴聚结,从而避免产生大的液溅。因此,可以得出结论,TiC的引入大大降低了金属汽化,消除了金属汽化产生的液体飞溅物,减少了铝合金在LPBF加工过程中的锂损失。
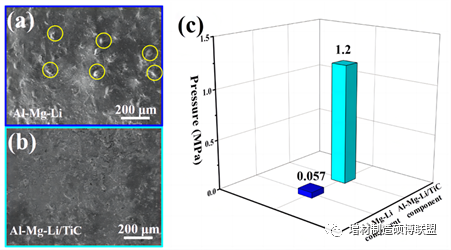
图9 打印的(a)Al-Mg-Li合金和(b) TiC改性Al-Mg-Li合金的顶表面SEM图;(c)惯性压力,即促进打印Al-Mg-Li合金液滴聚结的直接液-液接触的动能,以及TiC改性Al-Mg-Li合金的毛细管压力势垒热裂纹是AM工艺中高强度铝合金常见的问题,是导致材料打印性差的直接原因。一般来说,LPBF成形的热裂纹是由冶金力和机械力的共同作用造成的[42]。LPBF加工的Al-Mg-Li合金的凝固行为和微观结构演变的相关示意图如图10 (a)所示。当凝固过程中半固态温度范围较宽时,可引起冶金驱动力,导致长通道的树突间区域,因此,由于液相不及时供给凝固收缩而造成裂纹的形成。另一方面,在LPBF成形过程中,较大的热梯度和超高的冷却速率通常会导致残余应力的产生,即机械驱动力,这也导致了热裂纹的形成。如图3(b-c)所示,LPBF固有的温度梯度与凝固速率的高比值导致Al-Mg-Li合金中出现粗柱状晶粒,由于半固体态柱状晶粒的适应应变能力低,因此粗柱状晶粒之间形成热裂纹[43]。相比之下,在LPBF成形的Al-Mg-Li合金中加入TiC纳米颗粒,通过原位形成的Al3Ti诱导了大量的晶粒细化,有效地抑制了裂纹形成,如图10 (b)所示,这是由于LPBF成形TiC改性Al-Mg-Li合金中细等轴晶粒的应变容纳能力比LPBF成形Al-Mg-Li合金中的粗柱状晶的应变容纳能力更强(图3 (c)和(f))。此外,在Al-Mg-Li合金中加入TiC,显著降低了LPBF成形的残余应力,如图5 (b)和(d)所示。因此,我们可以合理地认为添加TiC可以通过减少细等轴晶粒之间的液相存在和减轻热收缩引起的残余应力来消除热裂纹。
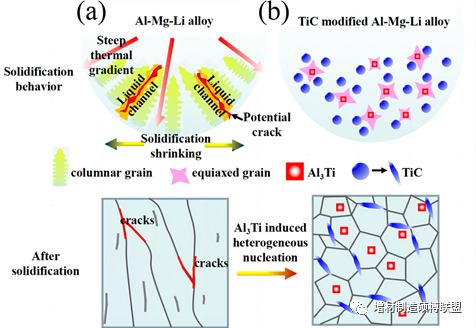
图10 LPBF加工的(a)Al-Mg-Li合金和(b) TiC改性Al-Mg-Li合金的凝固行为和微观组织演变示意图此外,在LPBF加工的TiC改性Al-Mg-Li合金晶粒中发现了立方L12-Al3Ti沉淀相,如图7所示。图8 (c)中TiC纳米颗粒上的Al和Ti元素分布和图8 (d)中α-Al与TiC之间形成的Al3Ti相证明Al原位与TiC反应形成Al3Ti。因此,考虑到铝合金LPBF过程中熔体池温度超过2000℃时,该反应的标准吉布斯自由能差为显著负值,具有较强的反应趋势。根据热力学计算结果(图11),Al3Ti相在Al结晶前沉析,说明TiC的加入改变了Al相的凝固顺序。在TiC上形成的Al3Ti作为随后固化Al相的直接晶粒细化剂。因此,由于Al3Ti沉淀相与α-Al相同的晶格匹配,有效地促进了α-Al的非均匀成核。
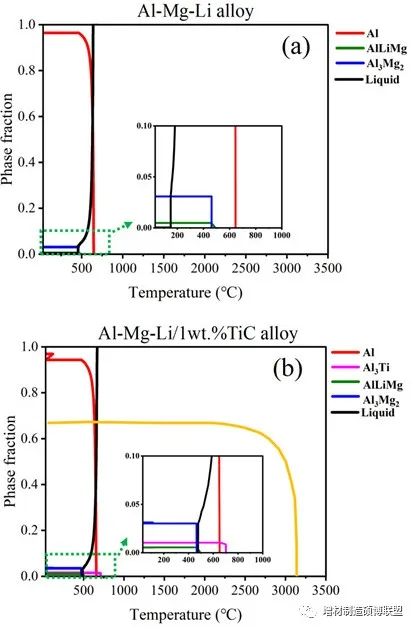
图11 (a)Al-Mg-Li合金和(b) 1 wt.%TiC改性l-Mg-Li合金的相图
如图3 (d)和(f)所示,LPBF成形的TiC改性Al-Mg-Li合金呈现出完整的等轴晶粒结构,与打印的Al-Mg-Li合金的晶粒明显不同。在力学性能方面,LPBF成形的TiC改性Al-Mg-Li合金的强度和伸长率分别为340 MPa和9.3 %,比强度为150 MPa,在所有LPBF打印Al-Mg-Li合金中具有优异的性能。LPBF成形的TiC改性Al-Mg-Li合金力学性能的提高主要是由于裂纹的消除和全等轴晶粒的形成。如图4 (a)和(b)所示,LPBF成形的TiC改性Al-Mg-Li合金的平均粒径比Al-Mg-Li合金的平均粒径低两个数量级。因此,引入了更多的单位面积晶界,通过有效抑制晶界对位错运动的影响,大大提高了材料的晶界增强(σGB)。可以根据经典的Hall-Petch公式[45]给出,如下所示:
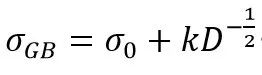
其中,σ0为晶格对位错运动的固有阻力(约20 MPa),k为铝合金的Hall-Petch常数(0.17 MN/m3/2)。D为晶粒尺寸。因此,计算得到的LPBF打印TiC改性Al-Mg-Li合金的晶界强度为158 MPa,如图12所示,由于超细的等轴晶粒,其晶界强度高于其他LPBF打印铝合金的晶界强度。这与文献数据中的拟合线(黄色实线)[11, 13, 14, 24, 42]相一致。随着晶粒尺寸的减小,TiC改性Al-Mg-Li合金的晶界强度在1.5µm时达到最大值,为158 MPa,Al-Mg-Li合金的晶界强度在173µm下降低到32 MPa。这些数据与σGB-1/√D外推的Hall-Petch线(蓝色虚线)相一致。LPBF打印TiC改性Al-Mg-Li合金的明显硬化与晶粒尺寸相当的LPBF打印铝合金的硬化是一致的,这源于在较细粒径下从位错滑移到晶界强化过程的塑性变形机制。图12 LPBF打印铝合金的晶界强度随粒径尺寸的变化[11, 13, 14, 24, 42];黄色实线是文献数据的拟合线;蓝色虚线是σGB-1/√D外推的Hall Petch曲线图;R2值代表模拟的测量指标此外,如图6 (a)所示,Al3Ti相在LPBF成形TiC改性的Al-Mg-Li合金的晶粒内或晶界处均匀分布,在拉伸变形过程中钉扎位错和晶界运动中起着关键作用。这有助于增强奥罗万强化机制,提高了材料的力学性能。根据图S1中的EDX-映射结果,Mg主要固溶于铝基中,从而提供了固溶强化。因此,材料的整体屈服强度可以通过对个别加强机制的所有贡献的总和来评估。LPBF成形的TiC改性Al-Mg-Li合金的强度增量是晶界强化、奥万罗强化和固溶强化的代数和。此外,如图7 (d)所示,新形成的Al3Ti相与α-Al的晶格失配低于TiC与α-Al的晶格失配,这不仅减少了原子排列失配,提高了成核效率,还提高了粘接强度,改善了延性。
特别地,发现在LPBF制备的TiC改性Al-Mg-Li合金中形成的堆叠断层(SFs)很有趣(图7 (e))。由于晶界的高能量和高原子活性,新的Al3Ti相很容易在晶界上的TiC纳米颗粒上优先成核(图7 (d))。而附着在TiC纳米颗粒上的Al3Ti相的外延生长导致了TiC纳米颗粒中产生SFs(图7 (e)),这也在AlTi和Ag层之间观察到了相似的现象。因此,形成的SFs扭曲了晶格,从而阻碍了位错发射,导致了显著的加工硬化。