文章详情 Article details 轻烃分离材料和机理的研究进展 罗伊雯,赵亮,张宇豪,刘东阳,高金森,徐春明 中国石油大学(北京)重质油全国重点实验室,北京 102249 引用本文 罗伊雯, 赵亮, 张宇豪, 等. 轻烃分离材料和机理的研究进展[J]. 化工进展, 2025, 44(5): 2938-2954. DOI:10.16085/j.issn.1000-6613.2024-2067 摘要 summary 随着我国新能源的发展和石油需求峰值的临近,石油行业面临炼油产能过剩的问题。将石油通过轻烃分离后转向生产化工原料是缓解炼油产能过剩、弥补当前化工原料短缺和实现石油高值化利用的有效途径。本文首先介绍了轻烃在化工行业的重要性和轻烃分离的意义,讨论了轻烃分离机理,具体介绍了分子筛效应、动力学效应、热力学平衡效应和协同效应的分离原理和适用材料。然后按照不同烃类的分离进行分类,详细讨论了各种轻烃分离的研究现状,并对不同材料的分离效果进行对比,总结了不同分离材料的适用范围。最后,对未来轻烃分离的研究方向进行了展望,为今后开发分离效果更好、成本更低的轻烃分离技术和分离材料提供了借鉴。
中国石油集团经济技术研究院发布的《2023年国内外油气行业发展报告》显示,去年中国炼油能力达到9.36×108t/a,已稳居全球第一,但随着新能源的发展和石油需求峰值的临近,以生产成品油为主的传统炼油加工路线不再适应现代市场需求。当前我国石油行业仍面临着前所未有的双重挑战,即一方面炼油产能过剩而另一方面化工原料短缺。随着经济快速发展和人口稳步增长,化工原料在石油消费中的占比逐年提高,但我国关键化工原料如乙烯、对二甲苯等仍存在产能不足,大量依赖进口。为了有效应对这一现状,炼化企业应积极开展传统炼油向化工原料生产的转型,实施轻烃分离,满足下游产业的生产需求,使轻烃更高效地转化为化工原料。 轻烃(表1)是生产燃料、塑料和高分子聚合物的重要化工原料,但从石油中获得的轻烃通常包含其他杂质,因而必须进行分离纯化。例如,甲烷是重要清洁能源,主要来源为天然气,但是其中也含有较高浓度的乙烷等杂质;乙烯和丙烯主要通过石脑油或乙烷和丙烷的高温蒸汽裂解获得,但该过程无法实现完全反应,产物中不可避免地会残留乙烷和丙烷杂质。轻烃的分离可分为烷烃/烯烃的分离、烯烃/炔烃的分离、不同碳数的烷烃分离、正异构烷烃的分离。通过石脑油和低碳烷烃蒸汽裂解得到的低碳烯烃不可避免地包含烷烃和炔烃等杂质,而烷烃/烯烃和烯烃/炔烃的分离可有效提高低碳烯烃的纯度。不同碳数的烷烃分离可以实现产出符合不同等级和质量要求的燃料产品,如汽油、柴油等;相同碳数的正异构烷烃分离能得到用作异构化反应和蒸汽裂解制乙烯的正构烷烃,和用作催化重整反应及高辛烷值汽油调和组分的非正构烷烃。 轻烃分子的性质
本文探究了轻烃分离材料的分离机理,按照不同烃类的分离进行分类,总结了烷烃/烯烃分离、烯烃/炔烃分离、不同碳数的烷烃分离、C4异构体分离和C5以上异构体分离的研究现状,并对不同材料的分离效果进行了对比,为今后开发分离效果更好、成本更低的轻烃分离技术和分离材料提供指导,并希望为缓解我国炼油产能过剩和化工原料紧缺的矛盾提供研究思路。
01 分离机理
轻烃分离机理通常包括四种类型:分子筛效应、动力学效应、热力学平衡效应和协同效应。
1.1 分子筛效应 分子筛效应(molecular sieving effect)是一种物理分离方法,是利用材料的孔径大小来实现不同轻烃分子的分离。具体来说,小于孔径的轻烃分子能够进入材料的孔道中,而大于孔径的分子则被排除在外。这种分离机理是基于材料规则的孔道结构和均一的孔径,利用分子尺寸差异来实现分离的。 分子筛效应是轻烃分离中最重要的机理,在分子筛和金属有机框架材料(metal organic frameworks,MOFs)中表现得尤为明显。AgA分子筛的孔径为4.35Å(1Å=0.1nm),介于乙烷的动力学直径4.163Å和乙烯的动力学直径4.443Å之间,因此可以利用AgA分子筛对乙烷和乙烯实现分离。由于Zn(dps)2(SiF6)的孔径和乙炔的动力学尺寸相近,都为3.3Å,而乙烯的动力学尺寸为4.2Å,根据分子筛效应,该金属有机框架材料能够实现乙烯和乙炔的分离。Lin等进一步探究,制备了一种具有一维孔道的金属有机框架材料Ca(C4O4)(H2O),其孔道横截面积为14.4Å2,大于乙烯的最小横截面积13.7Å2,小于乙烷的最小横截面积15.5Å2,因此乙烯可以通过孔道而乙烷被阻挡。 分子筛效应启发研究人员在设计新型分离材料时,将分离对象的尺寸差异作为首要考察因素,分析目标分子的尺寸和形状特性,以此为基础来精确调控材料的孔径大小和孔道结构。这样的设计策略使得材料能够更高效地分离轻烃,提高分离选择性。因此分子筛效应不仅为分离技术提供了理论基础,也为新型分离材料的开发指明了方向。 1.2 动力学效应 动力学效应(kinetic effect)是一种重要的分离机理,与分子的吸附作用和孔道之间的相互作用力有关,吸附性、作用力强的轻烃优先通过。动力学效应分为动力学吸附作用、空间位阻作用和扩散作用。动力学吸附作用是基于不同分子与孔道表面之间范德华力、静电引力或氢键等相互作用的差异实现轻烃分离。在CMS-IMP12分离正庚烷和异庚烷的过程中,烷烃中的C—H键与碳分子筛(carbon molecular sieve,CMS)中的π键之间的相互作用起到至关重要的影响。由于异庚烷中存在更多支链,导致其CH/π作用力更显著,因此CMS-IMP12对异庚烷的吸附性更强。 空间位阻作用是利用材料中某些原子或基团的空间位置或结构对吸附产生阻碍效应。Wu等采用巨正则蒙特卡罗(GCMC)方法模拟和研究了UiO-66及其变体[UiO-66-NO2、UiO-66-NH2、UiO-66-Br和UiO-66-(CH3)2]对C1~4烷烃/烯烃吸附分离的影响。研究发现,与UiO-66相比,UiO-66-(CH3)2更适合分离二元混合物。这是由于UiO-66-(CH3)2中两个官能团的尺寸较大,导致空间位阻作用强,因此具有良好的选择性。为了提高轻烃分离的选择性,可以考虑增强分子与分离材料之间的相互作用力,或引入官能团来增强空间位阻作用。 扩散作用是膜分离的重要机理,主要体现在轻烃分子从高浓度区域向低浓度区域的传递过程,这一过程基于膜两侧的浓度梯度,扩散速率也与膜材料的自身性质有关。Sridhar等分别采用由聚苯醚(PPO)、聚砜(PSF)、醋酸纤维素(CA)和乙基纤维素(EC)制成的聚合物膜分离丙烷/丙烯。结果表明,PPO膜对丙烷的渗透系数为2.1,对丙烯的渗透系数为9,分离因子为4.25;PSF膜对丙烷的渗透系数最高达到17.8,对丙烯的渗透系数为25,分离因子为1.4;CA膜对丙烷的渗透系数为5.8,对丙烯的渗透系数为15.2,分离因子为2.6;EC膜对丙烯的渗透系数最高达到52,对丙烷的渗透系数为16,分离因子为3.25。因此可见,由于不同的膜材料的孔径大小和与轻烃的相互作用力的差异,导致它们在丙烷和丙烯的分离效果上存在差异。 1.3 热力学平衡效应
热力学平衡效应(thermodynamic equilibrium effect)是基于轻烃进入分离材料的孔道时,孔道表面和不同分子之间的相互作用而产生的热力学差异实现分离,如吸附自由能(ΔG)、吸附热(ΔH)和吸附熵(ΔS)等。赵丽等通过Monte Carlo模拟研究了丙烯/丙烷混合物在分子筛上的吸附热力学。结果表明,丙烯的吸附量为2.3mmol/g,丙烷的吸附量为0.61mmol/g,这是由于丙烯的等量吸附热大于丙烷,因此分子筛更倾向于吸附丙烯。Couck等发现C5烷烃在色谱中的保留时间随着支链的增多而减少,这归因于异构烷烃的亨利常数明显低于正构烷烃。
1.4 协同效应
协同效应(synergistic effect)指的是多种作用机理结合在一起共同对分离过程产生影响。Xu等探索了9种纳米多孔石墨烯膜对C2~4烷烃/烯烃的分离效果。从热力学角度分析,C4H10的扩散能垒比C4H6高15.07kJ/mol,意味着C4H6比C4H10更容易穿过石墨烯膜。从动力学角度分析,碱性石墨烯膜的孔径为4.4~4.8Å,C4H6和C4H10的最小横截面积分别为3.4Å×5.2Å和4.4Å×4.7Å,因此C4H6更容易通过。正是动力学尺寸筛分和热力学竞争吸附的协同作用,使得该石墨烯膜吸附炔烃但排斥烷烃。分子筛的分离机理主要是分子筛效应,分离小分子而排斥大分子,但也会存在反常现象。比如CPDA@A-ACs对乙烷的吸附等温热高于乙烯,因此更倾向于优先吸附乙烷。这表明分子筛对分子的吸附能力不仅受孔径大小的影响,还受到热力学效应的影响。在轻烃的分离过程中,分子筛效应通常伴随着热力学效应、动力学效应和扩散作用,多种机理共同作用能产生独特的分离效果。
02 轻烃分离
在工业生产过程中,为了最大限度地利用轻烃,通常需要获得较高纯度的单一烃类产品。因而需要对石油或天然气加工过程中获得的轻烃混合物进行分离和纯化。轻烃是石油化工的主要原料,其分离具有重要意义。例如,乙炔被广泛用于合成化工产品和电子材料,乙烯和丙烯是生产塑料的主要原料。目前,基于分子筛和金属有机框架材料的吸附分离,以及基于膜材料的膜分离技术已逐步取代传统轻烃分离技术。近年来,在烷烃/烯烃的分离、烯烃/炔烃的分离、不同碳数的烷烃分离、正异构烷烃的分离方面取得了很大进展。表2总结了烷烃/烯烃分离的研究成果。
烷烃和烯烃结构相似,沸点相近,因此分离难度较大。低温精馏是一种传统的烷烃/烯烃分离技术,其分离原理是利用气体组分的沸点差异来分离目标产物。该方法能够实现高效分离,然而操作条件严苛,需要高压、多塔板和高回流比,因此分离过程存在成本高和耗能大的问题,其能耗约占全球能源消耗的0.3%。例如,乙烷/乙烯分离在248K和2300kPa下进行,丙烷/丙烯分离在243K和3000kPa的条件下有100多个塔板的蒸馏塔中进行。迄今为止,关于烷烃/烯烃的分离研究很多,常用的分离技术有基于碳分子筛和金属有机框架材料的吸附分离,以及基于碳分子筛膜(carbon molecular sieve membrane,CMSM)和混合基质膜(mixed matrix membrane,MMM)的膜分离,但这些研究主要集中在C4以下的分离。表2总结了烷烃/烯烃分离的研究成果。
2.1.1 分子筛 分子筛是一种具有有序晶体结构、均匀孔道和高比表面积的吸附剂,可以允许尺寸小于或等于孔径的分子进入,而大于孔径的分子则被阻挡在外,从而达到筛分的目的。分子筛的骨架结构主要由硅氧和铝氧四面体组成,以共享的氧原子连接在一起,形成一种三维网状结构。通过调整分子筛的硅铝比可以得到不同类型的分子筛,如A型分子筛、MFI型分子筛等。分子筛具有高吸附能力、强选择性和优异耐高温特性,已成为工业气体分离的优良吸附剂。 20世纪80年代,Schoellner等首次报道了利用改性4A分子筛从混合气(23%甲烷、22%乙烷、42%乙烯和12%丙烯)中分离乙烯、丙烯。在323K和常压下,乙烯和丙烯的穿透时间为15min和33min,甲烷和乙烷在3min前穿透。由于烷烃和烯烃都具有一定的极化率,普通分子筛的分离效果一般,因此需要通过引入金属离子,利用π络合对烯烃进行选择性吸附,提高对烷烃/烯烃的分离能力。Aguado等用银离子交换的A型分子筛(AgA)来分离乙烷/乙烯,并与银离子交换的沸石(AgX)进行了比较。实验表明,在303K、1×105Pa下,AgX对乙烯的吸附量为2.4mmol/g,对乙烷的吸附量为1.4mmol/g;AgA对乙烯的吸附量为2.3mmol/g,对乙烷不吸附,说明银离子交换的A型分子筛对乙烷/乙烯的分离效果更好。这是由于AgA的孔径为4.35Å,介于乙烷的动力学直径4.163Å和乙烯的动力学直径4.443Å之间,因此可以吸附乙烯而排斥烷烃,达到分离的效果。由于丙烷和丙烯的极化率非常接近,丙烷/丙烯的分离难度比乙烷/乙烯更大。Divekar等用重量微天平测量了丙烷和丙烯在13X分子筛和制备的Na-ETS-10上的吸附平衡等温线。在298K、1×105Pa下,13X分子筛和Na-ETS-10对丙烯的吸附量分别为3.1mmol/g和1.75mmol/g,对丙烷/丙烯的选择性分别为22和7.4。由此可见,AgA分子筛适用于乙烷/乙烯的分离,而13X分子筛和Na-ETS-10分子筛更适合丙烷/丙烯的分离。 2.1.2 碳分子筛
碳分子筛是一种的特殊碳材料。与沸石分子筛相比,碳分子筛不是高结晶体,而是由很小的类石墨微晶组成,其微孔由相邻的微晶底面构成,呈狭缝状,孔径集中在0.3~1nm,孔容一般为0.25cm3/g,结构如图1所示。碳分子筛由于孔隙率丰富、热稳定性好、比表面积大和吸附分离能力强,已被证明是用于烷烃/烯烃分离的有前途吸附剂。其主要利用大小均匀的狭缝状微孔实现轻烃分离。因此设计和调控碳分子筛的孔径是分离的关键点,影响孔径大小的因素包括炭化温度和炭化时间。
图1 碳分子筛的结构和孔隙度模型 Liu等用凝胶型强酸阳离子交换树脂合成碳分子筛,研究了炭化温度550~1000℃对丙烯/丙烷分离的影响。随着炭化温度升高,丙烷/丙烯吸附曲线先远离再靠近,850℃时相距最远,说明850℃是最佳炭化温度。使用该碳分子筛进行填充床吸附实验,得到丙烷/丙烯的分离因子高达27。碳分子筛的分离机理主要是孔径筛分,小于孔径的分子可以进入,而大于孔径的分子被阻挡在外。Liang等合成了炭化聚多巴胺和沥青基活性炭复合碳材料(CPDA@A-ACs),发现其对乙烷的吸附优于乙烯。在25℃和100kPa条件下,乙烯吸附量为6.25mmol/g,乙烷吸附量高达7.12mmol/g。这是由于该碳分子筛对乙烷的吸附等温热高于对乙烯的吸附等温热,因此优先吸附乙烷。由此可见,碳分子筛对分子的吸附能力不仅受到孔径大小的影响,热力学效应也是决定吸附性能的关键因素。 为了提高烷烃/烯烃的吸附选择性,可以向碳分子筛的骨架或表面引入金属阳离子,通过金属阳离子与烯烃之间形成的π络合作用,进一步增强对烯烃的吸附能力。Gao等将CuCl2负载到碳分子筛上进行改性。在303K和100kPa条件下,铜负载量为8mmol/g的碳分子筛对乙烯的吸附量为2.57mmol/g,对乙烷/乙烯的吸附选择性为70,与不负载铜的碳分子筛相比,选择性提升了3832%。杜胜君进一步探究了Na+、K+和Rb+三种金属阳离子对碳分子筛的分离效果。结果表明,改性前和改性后的碳分子筛对丙烷与丙烯的吸附量比值比5A分子筛和ZSM-5分子筛高出78%,这表明碳分子筛比传统分子筛更适合分离烷烃和烯烃。尽管碳分子筛能够分离的范围更广,但单一的孔结构和配位方式限制了孔径调节和功能化发展。目前只能通过控制炭化条件和取代金属阳离子的方法对碳分子筛进行改性,这在一定程度上限制了其分离性能的提升。因此如何更有效提高分离性能,成为未来碳分子筛研究的重要方向。 2.1.3 金属有机框架材料
金属有机框架材料(MOFs)是近些年快速发展起来的一种纳米多孔材料,它们以金属离子为中心、有机物为配体,通过配位键(或氢键、范德华力、π-π作用等)连接在一起,形成三维网状的晶体结构,如图2所示。这种材料之所以能吸附轻烃,主要是因为其独特的孔道和空腔结构,可以根据分离对象的尺寸大小设计合适的孔结构和孔径,从而达到分离效果。MOFs因具有孔结构可设计性、孔径可微调、易功能化等优点,在气体吸附、储存与分离等方面得到了广泛应用,弥补了碳分子筛孔结构和配位方式单一的不足。
Wang等首次制备出具有开放金属位点的金属有机框架材料Cu-BTC,用于乙烷/乙烯的分离。在22℃、80kPa下,乙烷吸附量为4.7mmol/g,乙烯吸附量为5.8mmol/g,这是由于乙烯的π电子与Cu-BTC中铜离子相互作用。Bao等进一步研究了Ni2+、Mg2+、Co2+三种金属离子对金属有机框架材料M-gallate分离乙烷和乙烯的影响。结果表明,Co-gallate对乙烯的吸附量最高,达到3.37mmol/g,且对乙烷/乙烯的选择性高达52。这一优异的分离性能归因于该材料具有相互连接的三维锯齿状通道,其孔径大小为3.47~3.69Å,介于乙烯(3.28Å×4.18Å×4.84Å)和乙烷(3.81Å×4.08Å×4.82Å)之间。除了引入金属离子来增强乙烷/乙烯的分离效果,还可以通过引入基团的方式增强金属有机框架材料和乙烯分子的作用力,提高乙烷/乙烯的选择性。Yang等制备了一种含羟基基团的金属有机框架材料NOTT-300。结果表明,在293K、1×105Pa下,乙烯的吸附量能达到6mmol/g,乙烷/乙烯的选择性为48.7。这是由于乙烯通过氢键、π···π堆积相互作用和分子间偶极子相互作用与NOTT-300形成较强联结。
2.1.4 碳分子筛膜
碳分子筛膜是由聚合物前体在惰性气氛或真空条件下高温热解制备而成,其内部是由sp2杂化的六边形碳构成的极小有序层状或片状碳层,并通过无序堆叠造成的缺陷形成膜中微孔,其孔结构如图3所示。碳分子筛膜的性能受聚合物前体的结构影响。具有更多共面芳环的聚合物前体有利于炭化过程,这有助于形成有序的碳层堆积结构,从而提高的分离选择性。相反,大体积侧链会削弱了聚合物前体的共面性,阻碍碳层的堆积,进而导致选择性下降。此外,炭化条件对膜的渗透性起着决定性作用,包括炭化温度、炭化时间、通入气氛和升温速率。通常,较高的炭化温度、较低的升温速率和较长的炭化时间会产生更多的碳层堆积,形成更有序的微孔结构。这意味着膜的渗透性会降低,但选择性会提高。作为近30年迅速发展的新型微孔无机膜,碳分子筛膜不仅具有传统无机膜的优点,如机械强度高、热稳定性高和孔径分布均匀等,还具有优良的气体分离性能。
Salinas等以具有羟基官能团的PIM-6FDA-OH聚酰亚胺为前体,在800℃下炭化得到碳分子筛膜,其对乙烷/乙烯的选择性达到17.5。Chu等进一步研究发现,加入金属阳离子可以增强CMSM对烷烃/烯烃的分离能力。他们以6FDA-DAM:DABA聚酰亚胺为前体制备碳分子筛膜,将纯碳分子筛膜和含Fe2+碳分子筛膜进行对比,结果表明,乙烷/乙烯和丙烷/丙烯的选择性分别提高了19%和11%。Wang等以羧化聚酰亚胺为前体制备碳分子筛膜,并探究了热解温度和Zn2+功能化对膜分离性能的影响。研究发现,当炭化温度为576℃和800℃时,CMSM对乙烯的渗透率显著下降,从244.6Barrer降至10.4Barrer,而乙烷/乙烯的选择性则从4.80上升至24.1,是迄今为止的最高值。说明升高炭化温度可以提高CMSM的选择性,但会牺牲一定的渗透性。此外,Zn2+功能化的CMSM选择性从4.80提升至6.75。由此可见,提高热解温度和使用Zn2+功能化都可以提高CMSM的气体选择性。
2.1.5 混合基质膜 混合基质膜是以高分子聚合物相为主体,无机材料为分散相的复合膜材料。其结合了无机材料高分离性和高分子聚合物经济性与易加工性的优势,提高了单一膜材料的性能。混合基质膜的分离核心是填料,填料一般以高分离性的金属有机框架材料为主,不同的填料对膜材料的渗透性和选择性的影响效果也不同。徐笑峰等以ZIF-8为填料制备了混合基质碳膜,考察了ZIF-8掺杂量和炭化温度对丙烷/丙烯分离效果的影响。结果表明,在ZIF-8掺杂量为1%和炭化温度为550℃的条件下,掺杂的混合基质碳膜对丙烯渗透率为174Barrer,丙烷/丙烯分离选择性为14.4,而未掺杂的纯碳膜选择性仅为5.1。Liu等以Zr-fum-fcu-MOF作为填料制备6FDA-DAM混合基质膜,并进行了丙烷/丙烯分离实验。研究表明,当在聚合物膜中添加29.4%(体积分数)的Zr-fum-fcu-MOF时,丙烯的渗透速率为19Barrer,丙烷/丙烯的选择性约为34,与纯聚合物膜相比,丙烯的渗透率和丙烷/丙烯的选择性分别提高了7.6%和73.1%。可见无机材料的引入能够提高聚合物膜的分离效果。 金属离子改性或基团修饰后的分子筛可用于烷烃/烯烃的分离,但选择性相比于其他材料较低。碳分子筛膜和碳分子筛的孔结构相似,以无序堆积的六边形碳为主。调控材料的孔径大小可以通过控制热解条件来实现,如炭化温度、时间、气氛和升温速率等。这两种材料的主要区别在于材料的形态,碳分子筛膜由于薄膜形态,其对小分子烯烃的渗透性较强,因此对烷烃/烯烃的选择性更强。而通过金属离子改性以后的碳分子筛,由于金属离子与烯烃之间形成的π络合作用,对烷烃/烯烃的选择性比普通碳分子筛更强。金属有机框架材料的分离一方面依靠孔径筛分,另一方面源于金属离子与π电子云相互作用,其对烷烃/烯烃的选择性有高有低,主要与金属有机框架材料的选择有关,其分离效果与未改性的碳分子筛和碳分子筛膜相似,但明显低于改性后的碳分子筛。混合基质膜对烷烃/烯烃的分离效果也不如改性后的碳分子筛,但其具有无机材料和高分子聚合物的共同优势,可以通过在聚合物中掺入金属有机框架材料来提高膜的选择性。 2.2 烯烃/炔烃分离
乙烯和丙烯是石油化工生产过程中最常见的烯烃原料。在蒸汽裂解制烯烃的过程中,不可避免地会混有炔烃。为了获得聚合级乙烯和丙烯,烯烃/炔烃的分离是很重要但也是具挑战性的工业过程之一。溶剂吸收是一种用于炔烃脱除的传统分离方法。它的分离原理是基于不同气体在吸收剂中溶解度的差异,具有选择性高、可回收等优点,但是大多数溶剂具有毒性,且存在溶剂再生的问题。基于金属有机框架材料的吸附法为开发成本低、能耗小的炔烃脱除技术提供了巨大的希望。表3总结了烯烃/炔烃分离的研究成果。
烯烃/炔烃分离的研究成果总结 2011年,Xiang等开发了首个用于乙烯/乙炔分离的金属有机框架材料(M'MOF),通过手性二胺(R,R)-1,2-环己二胺向M'MOF中引入手性孔,并通过掺入不同的双羧酸盐来调节手性孔的大小。室温下,该材料对乙烯/乙炔的分离选择性达到5.23。金属有机框架材料的分离性能不仅仅取决于孔径大小,引入金属位点也能进一步提升材料的分离选择性。Wang等将金属有机框架材料NCU-100中的Zn2+金属位点替换为Cu2+金属位点,观察到NCU-100中存在两种尺寸的空腔(3.6Å×4.3Å×4.2Å和4.7Å×4.5Å×4.2Å),与Zn2+取代的UTSA-300(3.5Å×3.9Å×4.1Å和4.3Å×4.3Å×4.1Å)相比,Cu2+取代的NCU-100与乙炔(3.3Å×3.3Å×5.7Å)更匹配。在298K、1kPa下,NCU-100的乙炔吸附量比UTSA-300提升了17.25倍,乙烯/乙炔混合气穿过填充床,乙烯纯度能超过99.99%。然而,目前报道的大多数MOFs都存在大吸附容量和高选择性的不能兼得的问题。JCM-1中吡唑酸盐作为金属结合基能够形成强的金属配体键,增强乙炔的吸附能力,但对乙炔/乙烯的选择性仅为3.1。这种对乙炔的强吸附能力来源于乙炔与孔表面的咪唑官能团相互作用,而选择性不高的原因是JCM-1具有大纳米孔径。迄今为止,只有少数MOFs在丙炔/丙烯的分离中表现出出色的分离性能。Li等制备了首个用于丙烯/丙炔分离的柔性金属有机框架材料ELM-12。该材料具有两种空腔,一种呈哑铃形,尺寸为6.1Å×4.3Å×4.3Å,另一种呈椭圆形,尺寸为6.8Å×4.0Å×4.2Å。与丙烯相比,丙炔与这些空腔的尺寸和形状匹配更合适,因此在103Pa和298K时,ELM-12对于丙炔的吸附量(1.83mmol/g)明显高于丙烯(0.67mmol/g)。 上述研究表明,金属有机框架材料适用于烯烃/炔烃的分离。其孔结构可通过两种方式进行调节:一是引入手性孔或金属阳离子的方式进行微调,二是在表面引入官能团以实现材料的功能化。该材料在烷烃/烯烃和烯烃/炔烃分离方面表现出色,近年来受到大量的关注和研究,然而MOFs的合成大多停留在实验室阶段,大规模生产所需的苛刻条件和昂贵的有机溶剂的使用限制了其工业化应用。因此尽管它在轻烃分离上具有优势,但合成成本高和合成规模小制约了其进一步的发展。 2.3 不同碳数的烷烃分离
不同碳数的烷烃分离可以提高原料的利用率,产出符合不同等级和质量要求的燃料产品,这对于化工产品的质量和性能至关重要。表4总结了不同碳数烷烃分离的研究成果。
A型分子筛具有三维孔隙结构,扩散性能良好,可以通过离子交换得到不同孔径的分子筛,如5A分子筛。目前大多数吸附分离研究都集中在低碳数轻烃上,针对高碳数烃类分离的研究相对较少。刘宇斯等以5A分子筛作为吸附剂,在不同的温度下对C11~16正构烷烃进行脉冲实验,发现随着温度升高,5A分子筛对正构烷烃的分离度先升高再降低,180℃时分离度达到最高:C11(1.31)>C12(1.14)>C13(1.01)>C14(0.98)>C15(0.95)>C16(0.94)。结果表明,随着碳链增长,5A分子筛对正构烷烃的吸附能力下降。这是由于正构烷烃的扩散活化能随着碳数的增长而增加,根据阿伦尼乌斯公式,相同温度下正构烷烃碳数越大,扩散速率常数越小。而随着温度升高,正构烷烃在5A分子筛中的扩散速率常数增大,因此分子筛的吸附速率加快,但吸附反应是放热反应,温度过高不利于反应进行,所以温度超过180℃,5A分子筛对正构烷烃的分离度开始下降。为了提高5A分子筛对正构烷烃吸附速率,陈翔等以二甲基十八烷基[3-(三甲氧基硅基)丙基]氯化铵为模板剂合成多级孔道5A分子筛。发现当加入0.4%模板剂时,合成的分子筛不仅具有0.5nm的微孔,还新增了7~13nm的介孔,正戊烷的液相扩散系数增大81.2%,正己烷增大89.9%,正庚烷增大98.3%,吸附速率明显加快。
2.3.2 聚合物膜 聚合物膜(polymer membrane)是一种有机膜,起源于20世纪60年代,由高分子聚合物材料制成。根据原料的不同,聚合物膜分为聚烯烃类、聚酰胺类、聚砜类、聚酰亚胺、聚偏二氟乙烯、聚四氟乙烯等。由于其具有多样的有机结构单元和极低的质量密度以及可调节的孔径,因而常用于轻烃分离。2006年,ExxonMobil公司提出了使用膜从炼油厂尾气中回收液化石油气的概念。由于聚硅氧烷膜和聚丁二烯膜对丙烷和丁烷烃类具有高吸附性,但不通过甲烷和乙烷,因而适用于液化石油气分离。Pinnau等在-20~35℃的温度范围内,测定了聚二甲基硅氧烷膜(PDMS)对单组分气体的渗透率和二元正丁烷/甲烷的选择性。进料温度为35℃时,甲烷、乙烷和丙烷的气体渗透率分别为1300Barrer、3900Barrer和7400Barrer。在25℃下,当正丁烷进料体积分数从1%增加到8%时,正丁烷/甲烷选择性从10增加到12。Kim等用聚乙烯-烯丙基-二甲基硅烷膜(PVASMS)分离C1~4正构烷烃,探究了热处理温度和时间对膜性能的影响。当热处理温度为120℃、热处理时间为15min时,PVASMS膜对甲烷、乙烷、丙烷、丁烷的渗透率分别为32.1Barrer、48.7Barrer、110.7Barrer、451.2Barrer,对甲烷/丁烷的选择性为14.1。 5A分子筛由于孔径范围较广,适用于C4以上烷烃的分离,在工业上已被用于分离石脑油中的正构烷烃,而聚合物膜更适合分离C4以下小分子的烷烃。这两种材料结合起来,可以实现全碳数烷烃的分离。 2.4 C4异构体分离
C4烃的需求范围很广,正丁烷主要用于生产乙烯、乙酸和马来酸酐,异丁烷用于生产叔丁醇和环氧丙烷,也可用于聚合物加工和在发泡聚苯乙烯生产中作为发泡剂,而C4烯烃作为石化工业的原料之一,在工业生产方面用于合成丁二烯橡胶、ABS树脂,在化工原料方面用于生产仲丁醇、甲基叔丁基醚。尽管C4烷烃有许多优点,但由于它们的尺寸和沸点相似,因此分离具有挑战性。表5总结了C4异构体分离的研究成果。
除了常用的MFI型分子筛之外,用于分离C4烷烃的还有ERI型分子筛。Richter等研究了微孔磷酸硅铝分子筛SAPO-17对丁烯异构体的分离。结果表明,反式-2-丁烯比1-丁烯和顺式-2-丁烯更容易吸附。这是由于SAPO-17具有0.36nm×0.51nm的椭圆孔,允许较小的分子(反式2-丁烯)通过,而阻塞较大的分子。在333K下,反式2-丁烯的吸附量为0.75mmol/g,反式-2-丁烯/1-丁烯和反式-2-丁烯/顺式-2-丁烯的选择性均为75,说明分子筛主要利用尺寸差异或者分子筛效应实现分离。在此基础上,进一步研究了热力学效应对分子筛吸附的影响。Ferreira等用压力法和微量热法探究了不同温度下正异构丁烷在MFI分子筛上的吸附,并进行了热力学计算。结果表明,在373K和100kPa下,n-C4H10的吸附量为1.37mmol/g,i-C4H10的吸附量为0.64mmol/g,n-C4H10/i-C4H10的选择性为2.14。这是由于n-C4H10在孔道中吸附,而i-C4H10仅在交叉处吸附。
2.4.2 金属有机框架材料
金属有机框架材料由于其均匀的孔径可实现精确的分子筛筛分,因此可用于C4异构体的分离。Chen等合成了具有最小缺陷的锆基金属有机框架材料(Zr-fum-fcu-MOF),通过控制合成反应条件(调制剂和配体的数量)在分子水平上对结晶度和结构缺陷进行调节。结果表明,富缺陷的Zr-fum-fcu-MOF对正异构丁烷的分离性能较差,主要受热力学驱动,而具有较少或无缺陷的Zr-fum-fcu-MOF分离性能较好,主要由动力学和分子筛效应驱动。在293K和80kPa下,无缺陷的Zr-fum-fcu-MOF对正丁烷的吸附量为4mmol/g,对正丁烷/异丁烷的选择性为20,相比之下,有缺陷的Zr-fum-fcu-MOF对正丁烷吸收量和选择性显著降低,分别为3.5mmol/g和1.4,首次证明了结构缺陷对金属有机框架材料分离C4异构体的重要影响。Cui等首次制备出能有效分离丁烯异构体的柔性金属有机框架材料MnINA。与CuINA(4.84Å)相比,MnINA具有更小的孔径(4.62Å),对正丁烯具有高的吸附容量(1.79mmol/g),通过C—H···π键形成强的相互作用。在0~1×104Pa的压力范围内,狭窄的通道对大分子异丁烯(4.84Å)产生了阻碍,这使得MnINA对正异丁烯的选择性高达327.7。相较于分子筛,金属有机框架材料不仅利用分子筛效应,还利用热力学效应和动力学效应实现分离。
2.4.3 分子筛膜 分子筛膜(zeolite membrane)是由分子筛在载体表面交错生长而形成,本质上属于无机膜,具有和分子筛相似的特点,如孔道均一、吸附性高和稳定性好。到目前为止,MFI型分子筛膜,包括silicalite-1膜和ZSM-5膜,因其易于制备、孔径适宜而被广泛研究。silicalite-1膜是一种纯二氧化硅基的无机膜,具有优异的热稳定性和化学稳定性,但亲水性差。相比之下,ZSM-5膜通过部分Si原子被Al原子取代,从而表现出良好的表面亲水性。 不同制备方法得到的分子筛膜材料,其分离效果也各不相同。Zhang等采用多层MFI(ML-MFI)分子筛制备了不含任何有机结构导向剂的二维分子筛纳米片。ML-MFI首先通过熔融复合剥离,然后使用H2SO4和H2O2的混合物进行去模板化,得到不含OSDA的MFI纳米片。存在于多孔多苯并咪唑载体上的纳米片对n-C4H10的渗透率为3.5×10-7mol/(m2·s·Pa),对n-C4H10/i-C4H10选择性为5.4。Sun等采用新型微波加热法在α-Al2O3管的内表面制备silicalite-1分子筛膜,并与常规加热法制备的膜进行了比较。当温度为333K时,其对n-C4H10渗透率为1.3×10-7mol/(m2·s·Pa),n-C4H10/i-C4H10的分离系数为45,比常规加热法制备的silicalite-1膜具有更高的选择性。李良清等利用两次变温热浸渍法在大孔α-Al2O3多孔管状载体外表面涂覆B-ZSM-5大小晶种,并通过二次生长法制备B-ZSM-5分子筛膜,同时利用气体渗透测试装置进行实验。研究表明,在200℃、0.125MPa下,B-ZSM-5分子筛膜对n-C4H10和i-C4H10的气体渗透率分别为5.98×10-8mol/(m2·s·Pa)和5.71×10-10mol/(m2·s·Pa),n-C4H10/i-C4H10的分离系数达104.73。由此可见,随着制备方法的不断改进,分子筛膜对正异丁烷的分离效果也在逐步提升。 2.4.4 碳分子筛和碳分子筛膜 碳分子筛和碳分子筛膜用于C4异构体的研究还处于起步阶段,目前报道较少。Li等通过高温炭化将金属有机框架材料(CD-MOF-2)转变为用于正异构烷烃分离的碳分子筛。在298K、1×105Pa时,通入等摩尔的正丁烷-异丁烷混合气,发现异丁烷可以直接穿过色谱柱而正丁烷在色谱柱中保留35min/g,表明该碳分子筛对正异丁烷具有筛分效果。Zhou等以P84聚合物膜为原料,在γ-Al2O3基体上热解制备碳分子筛膜。通过调控热解温度,在600℃热解温度下,成功制备出无裂纹、具有6Å均匀微孔的碳分子筛膜。该材料对n-C4H10渗透率为384GPU[1GPU=10-6cm3(STP)·cm-2·s-1·cmHg-1],n-C4H10/i-C4H10分离因子为74,是分离n-C4H10/i-C4H10性能最佳的膜之一。除了微孔和超微孔的组合之外,该膜的超薄厚度(0.59µm)也是高分离性能的原因。 目前,碳分子筛和碳分子筛膜更常用于烷烃/烯烃的分离,对C4异构体分离的研究较少,而分子筛膜是最常用于C4异构体分离的材料,包括ZSM-5沸石分子筛膜和silicalite-1膜。这是由于MFI分子筛膜由直通道(5.3μm×5.6μm)和锯齿形通道(5.1μm×5.5μm)构成,刚好介于n-C4H10和i-C4H10的尺寸4.7μm和5.3μm之间,因此能引起强分子筛效应。 2.5 C5以上异构体分离
C5以上异构体的分离包括石脑油中正构烷烃的分离和二甲苯异构体的分离。表6总结了C5以上异构烷烃分离的研究成果。
C5以上异构体分离的研究成果总结 2.5.1 5A分子筛和ZSM-5分子筛
石脑油中由于正构烷烃的辛烷值较低,而异构烷烃、环烷烃和芳烃的辛烷值较高,因此将正构烷烃分离出来可提高汽油的辛烷值。分离出的正构烷烃作为乙烯裂解的原料可提高乙烯收率,而剩余的组分作为催化重整的原料可提高芳烃收率。利用5A分子筛进行简单组分的正异构烷烃分离效果比较理想,但真实油品的组分复杂,与模型油的分离效果有显著差异。Liu等利用5A分子筛从石脑油中吸附分离正构烷烃,为蒸汽裂化和催化转化过程提供原料,产物中正构烷烃的分离纯度>99.9%,发现当吸附温度180~340℃、进料空速30~300h-1时,吸附能力较大,吸附传质区较小。翟万军对工艺条件进行了更详细的考察,以5A分子筛为吸附剂,采用固定床吸附器分离石脑油中的正构烷烃,考察了压力、温度、空速以及吸附剂使用周期对分离效果的影响。结果表明,压力0.5MPa、温度300℃、吸附空速0.5h-1和脱附空速230h-1时,正构烷烃总回收率达到95%,吸余油中正构烷烃含量<3%,且5A分子筛在使用了520个周期后仍保持吸附活性。20世纪60年代,5A分子筛分离C10~14正构烷烃已实现工业化,包括美国UOP公司开发的Molex工艺、Isosiv工艺和Exxon公司开发的Ensorb工艺,其对正构烷烃的回收纯度>98%,分离出的正构烷烃可以转化为烷基氯或烯烃,也可以将苯转化为烷基苯,但这些工艺在原料、反应条件和脱附剂方面有所不同。Molex工艺是唯一的液相工艺,以煤油为原料、正戊烷为脱附剂,Isosiv工艺和Ensorb工艺在气相条件下反应,前者以全馏分石脑油为原料,后者以氨为脱附剂。2013年,华东理工大学首次提出固定床双塔并联石脑油吸附分离工艺,工艺流程如图4所示。该工艺以32~174℃馏程的石脑油为原料,5A分子筛为吸附剂,氮气为脱附剂。其原理是利用正构烷烃和其余组分的尺寸差异,分离后脱附油中正构烷烃质量分数大于95%,可作蒸汽裂解制乙烯原料,与石脑油直接裂解相比,乙烯收率提高了14%。
图4 双塔并联吸附分离实验装置工艺流程 1—原料油储罐;2—原料油进料泵;3—原料油汽化炉;4—手动阀;5—电磁阀(红色表示打开状态,该状态表示1号床脱附、2号床吸附);6—中间油冷凝器;7—脱附油冷凝器;8—1号床层吸余油冷凝器;9—2号床层吸余油冷凝器;10—中间油气液分离器;11—脱附油气液分离器;12—分子筛床层;13—脱附油预热器;14—氮气储罐 除了5A分子筛,ZSM-5分子筛也常用于轻烃分离。ZSM-5分子筛属于MFI结构,具有三维交叉孔道结构和独特的十元环孔道,其中c轴方向的椭圆形直孔道孔径为0.54nm×0.56nm,a轴方向的圆形之字形孔道孔径为0.51nm×0.55nm,因而具有良好的择形吸附性能。田鹏等对ZSM-5分子筛吸附分离2-甲基戊烷和正己烷进行了研究,并将其分离效果与5A分子筛进行比较。结果表明,303K时,ZSM-5和5A分子筛对2-甲基戊烷吸附量分别为1.1mmol/g和0.04mmol/g,对正构烷烃的吸附量分别为1.34mmol/g和1.77mmol/g,说明ZSM-5分子筛比5A分子筛更适合吸附单甲基异构烷烃。基于此研究,江蕾等先用5A分子筛分离石脑油中正构烷烃,再用ZSM-5分子筛分离单甲基异构烷烃,最终得到的产品对烷烃的脱除率达到92.9%。 5A分子筛主要用于分离正构烷烃,而ZSM-5分子筛主要用于分离单甲基异构烷烃。在工业上,这两种分子筛常被联合使用,通过连续吸附分离过程,实现从石脑油中分离烷烃。尽管传统分子筛具有性质稳定、循环再生能力强、分离纯度高、经济性好的优点,但在烷烃/烯烃分离方面的研究较少,这仍是一个值得继续探索的领域。 2.5.2 分子筛膜
对二甲苯(PX)是一种常用的有机原料,在聚酯、涤纶和涂料的生产中扮演着关键角色,因此其分离非常重要。目前,工业上分离二甲苯异构体的工艺有吸附分离法和结晶分离法,但这两种工艺设备复杂、对装置的稳定性要求高,相比之下膜分离成本低、能耗低,具有发展前途。分子筛膜不仅可以分离C4异构体,还可以分离二甲苯异构体。Xomeritakis等在α-Al2O3表面二次生长制备定向MFI膜,在22~275℃和0.7~0.9kPa的进料分压范围内,对二甲苯异构体的分离效果进行了评价。研究发现,膜的分离性能与膜的合成条件及微结构相关。其中,在175℃下生长24h的膜对对二甲苯/邻二甲苯的选择性高达150。但由于在对二甲苯存在的情况下,邻二甲苯的通量急剧增加,二元混合物的分离系数很小。Daramola等制备了在高压下也能分离对二甲苯的HZSM-5/氧化铝复合膜。在200℃时,该膜对PX的通量为3.5×10-6mol/(m2·s),PX/OX分离因子大于400。当压力高达150kPa时,该膜仍保持对二甲苯的选择性,归因于氧化铝限制了孔和MFI纳米颗粒之间的紧密接触,减少了长期应力,从而防止了对二甲苯吸附过程中MFI框架的变形。
2.5.3 碳分子筛膜 碳分子筛膜不仅用于烷烃/烯烃的分离,也用于二甲苯异构体的分离。Koh等制备了一种反渗透碳分子筛膜。其对单组分PX的渗透通量是OX的25倍。在室温进料、压力为5~12MPa、进料为PX∶OX=1∶1的条件下,该材料对PX的渗透率超过81%,PX的渗透通量超过1.0×10-3mol/(m2·s),且分离因子大于4。Jang等制备出厚度仅1.8μm的超薄碳分子筛中空纤维复合膜。当压力为7~11MPa时,二甲苯异构体的选择性可达39.88,PX通量为0.032mol/(m2·s),膜通量比其他碳分子筛膜高出10倍,比沸石分子筛高出100~1000倍。 相比于分子筛膜,碳分子筛膜展现出更多的优势。在分离效率上,碳分子筛的孔道是狭缝形状,这不仅赋予了其高选择性,而且提高了渗透率,使得通量能够达到分子筛膜的10倍。在节能方面,碳分子筛的中空纤维膜对二甲苯异构体的分离不需要改变有机物的相态,从而可以减少分离过程中的能量损耗。 2.6 不同材料分离轻烃的性能对比
目前用于轻烃分离的材料分为分子筛、膜材料和金属有机框架材料三大类,其中膜材料包括碳分子筛膜、分子筛膜、聚合物膜以及混合基质膜。不同分离材料的分离性能如表7所示。
不同轻烃分离材料的分离性能 综合来看,每种材料都有其独特的优点和局限性。分子筛、碳分子筛和金属有机框架材料通过吸附小分子、阻挡大分子实现轻烃分离,而膜材料则依赖于吸附和膜两侧的压力差来驱动分离过程。分子筛虽然已实现工业化,稳定性好,但其吸附量较小,且孔径难精准控制。碳分子筛选择性高,但热稳定性一般。金属有机框架材料作为一种新兴材料,具有高选择性和可微调的孔径,但制备成本较高,难以实现规模化。膜材料由于较薄,通常具有比相应的分子筛更高的选择性,但普遍存在容易被污染的问题。 在实际应用中,选择合适的材料需要综合考虑分离目标、操作条件以及成本效益。对于高温高压环境的分离,分子筛和分子筛膜是理想选择;对于高选择性、中等温度环境的分离,碳分子筛和碳分子筛膜更为合适;对于孔径需求高的分离,金属有机框架材料是较好的选择;对于大规模、常温环境的分离,聚合物膜具有成本优势;而混合基质膜因其同时具有有机膜和无机膜的特点,在多种环境下的分离中展现出广阔的应用前景。未来的研究方向应集中在提高材料的稳定性、降低制备成本以及优化膜结构,以满足工业生产中对轻烃分离的多样化需求。
03 结语与展望 当前我国炼油产能过剩问题突出,为了将轻烃高效转化为下游化工原料,轻烃分离过程显得尤为重要。根据市场需求,分离出的正构烷烃可用作异构化反应或作为蒸汽裂解原料制乙烯。同时,异构烷烃、环烷烃和芳烃因其较高的辛烷值,可以直接用作调和汽油或送至重整装置进一步加工,生产高辛烷值的汽油组分。通过蒸汽裂解正构烷烃得到的低碳烯烃中,不可避免地会含有烷烃和炔烃等杂质,因此需要分离出其中的杂质,来有效提高烯烃的纯度。 轻烃分离材料的分离机理包括分子筛效应、动力学效应、热力学平衡效应和协同效应。分子筛和金属有机框架材料的分离主要利用分子筛效应、动力学效应和热力学平衡效应,而膜材料的分离主要依靠动力学效应中的扩散作用。当然在实际分离过程中,往往是多种机理共同作用,而非单一机理独立工作。 不同轻烃分离所用的材料也不同。烷烃/烯烃的分离主要使用碳分子筛、金属有机框架材料、碳分子筛膜和混合基质膜,其中改性后的碳分子筛分离效果明显高于其他材料。烯烃和炔烃由于分子尺寸相近且都含有不饱和键,分离难度大,目前研究最多的材料是金属有机框架材料。不同碳数的烷烃分离使用5A分子筛和聚合物膜,前者在工业上用于分离石脑油,后者适合分离C4以下的小分子烷烃。正异构烷烃的分离分为C4异构体的分离、石脑油中正构烷烃的分离和二甲苯异构体的分离。其中分子筛膜是最常用于C4异构体分离的材料,5A分子筛和ZSM-5分子筛适用于分离石脑油中正构烷烃,分子筛膜和碳分子筛膜适用于分离二甲苯异构体。 目前关于轻烃分离的研究仍十分有限,基于以上总结,未来轻烃分离的研究方向可以考虑以下几点。 (1)开发新型分子筛、金属有机框架材料和膜材料,增大分离材料的渗透性和选择性,使其更利于轻烃分离。 (2)目前碳分子筛、金属有机框架材料和膜材料的应用还局限于实验室阶段,将小规模实验室合成转化为大规模工业化应用是未来轻烃分离材料的研究方向。亟待解决的问题包括碳分子筛的老化、金属有机框架材料和膜材料的稳定性以及与现有工业流程的兼容性。 (3)由于轻烃分离需要更高的通量来减少处理给定进料量所需的膜面积,从而降低模块和整体分离系统的成本,因此未来必须通过进一步优化MOFs聚合物配方来减少膜厚度,从而增加渗透通量。 (4)结合计算化学和分子模拟,深入理解轻烃分离机理,并利用这些工具指导新型分离材料的设计。 第一作者:罗伊雯,博士研究生,研究方向为膜材料分离。 通信作者:赵亮,教授,博士生导师,研究方向为清洁油品生产、石油加工、催化材料、计算化学。
免责声明:本网站所转载的文字、图片与视频资料版权归原创作者所有,如果涉及侵权,请第一时间联系本网删除。
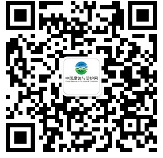
官方微信
《腐蚀与防护网电子期刊》征订启事
- 投稿联系:编辑部
- 电话:010-62316606
- 邮箱:fsfhzy666@163.com
- 腐蚀与防护网官方QQ群:140808414