全球塑料年需求量预计2050年将超11亿吨,但其生产严重依赖化石资源,2020年全生命周期温室气体排放达24.5亿吨CO₂当量。5-羟甲基糠醛(HMF)电氧化制备2,5-呋喃二甲酸(FDCA)是合成可再生聚酯的关键路径,但传统热催化需高温高压及贵金属催化剂,且存在副反应问题。此前千瓦级电流密度下的高选择性FDCA电合成始终未能突破,主要受限于电极界面传质不足、非法拉第副反应(如HMF缩合生成腐殖质)以及分子渗透等问题。
北京化工大学邵明飞、周华和清华大学段昊泓开发出一种固体聚合物电解质(SPE)反应器,通过工程化设计成功实现HMF的高选择性电氧化。该反应器在1.5 A cm⁻²工业级电流密度下,以97.0%选择性和88.2%法拉第效率稳定生产高浓度FDCA(~1.24 M),连续运行140小时性能无衰减。进一步构建的4.3 kW模块化电化学平台,达到33公斤/日的FDCA中试规模产能,较先前技术提升1-2个数量级。
反应器创新设计
团队提出系统性解决方案:1)采用催化剂涂层膜(CCM)集成阳极(NiCoMoO₄)和阴极(RuO₂),消除阴极液以抑制分子渗透,使HMF/FDCA跨膜通量降低10倍;2)优化多孔传输层(PTL)结构,组合菱形网格/泡沫镍/镍网(RSG/NF/NM)形成湍流,增强径向对流传质;3)蛇形流场设计使电解液流速提升10倍(28.8 cm s⁻¹);4)阳极板集成冷却腔控制温度<30°C,抑制HMF高温缩合副反应。200 cm²单模块测试表明(图2h),在0.5 A cm⁻²电流密度下连续运行140小时,FDCA产率保持88.1 g h⁻¹,浓度达1.27 M。
图1 | HMF电氧化制备FDCA的背景、演示与挑战。
图2 | SPE反应器设计与性能。
关键组件优化
对比实验验证了组件必要性:采用PTL-2(含RSG)与蛇形流场时,FDCA法拉第效率达84.5%,较基础PTL-1提升32%。流体模拟显示RSG结构产生大涡流,显著增强电极表面径向传质。冷却系统则使反应温度控制在29°C,避免82°C高温导致的FDCA选择性骤降至40.9%,并抑制腐殖质生成,将副反应导向可转化的Cannizzaro产物。
图3 | SPE关键组件优化对HMFOR的影响。
运行参数调控
高浓度HMF(1.4 M)将OER竞争反应压制至10.3%法拉第效率,使FDCA产率在1.5 A cm⁻²下提升至654 W功率。无阴极液设计将FDCA浓度提升至1.34 M(历史最高),同时单程模式将HMF停留时间缩至2.9分钟,较循环模式提升选择性20%。能耗降至2.54 kWh/kg FDCA,低于文献报道值。
图4 | 运行条件对HMFOR的影响。
中试应用展示
八台SPE反应器并联的4.3 kW平台(图5a)在1.0 A cm⁻²电流密度下,以88.7%法拉第效率日产FDCA 33公斤,同步产生高纯氢气(0.67 m³ h⁻¹)。所得FDCA成功用于生物基塑料制造:与乙二醇聚合生成聚呋喃二甲酸乙二醇酯(PEF)热塑性塑料,经3D打印成定制结构(图5e);与木质素衍生胺单体结合形成可回收环氧树脂,模压为"THU/BUCT"字母标识(图5f)。经济分析表明,通过联产K₂SO₄和H₂,FDCA成本可降至1301美元/吨,媲美热化学工艺。
图5 | 千瓦级FDCA生产与生物塑料应用
工业前景展望
该工作首次实现千瓦级生物质单体的高选择性电合成,为可持续塑料产业提供了可放大的技术原型。未来需开发更大电极面积的反应器、优化电解质循环系统,并降低HMF原料成本。研究团队强调,电化学路径有望推动塑料工业从"石油基线性模式"向"生物质闭环模式"转型,助力碳中和目标实现。
免责声明:本网站所转载的文字、图片与视频资料版权归原创作者所有,如果涉及侵权,请第一时间联系本网删除。
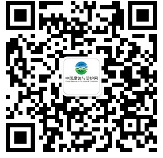
官方微信
《腐蚀与防护网电子期刊》征订启事
- 投稿联系:编辑部
- 电话:010-62316606
- 邮箱:fsfhzy666@163.com
- 腐蚀与防护网官方QQ群:140808414