导读:本研究以WC-Co硬质合金为例,实现了金属陶瓷颗粒内部金属纳米颗粒尺寸和含量的调控。该方法是基于定制合成陶瓷-金属复合粉末的原位反应物的组成。通过优化纳米颗粒在WC晶粒中的尺寸和含量,制备的WC-Co硬质合金的硬度、强度和断裂韧性同时得到提高,综合力学性能在文献报道的类似成分的金属陶瓷中达到最高。定量研究了陶瓷颗粒中金属纳米相对金属陶瓷微尺度应力应变分布的影响。对金属纳米相与陶瓷位错之间相互作用的详细表征和分析表明,这些纳米相阻碍位错运动,但不会引起局部应力集中和微裂纹成核,因此能够同时增强和增韧陶瓷晶粒。该研究为开发具有优异综合力学性能的金属陶瓷提供了独特的方法和定量指导,对低金属含量的金属陶瓷材料尤为重要。
金属陶瓷是制造和加工中用作工具和模具的典型代表材料。在具有各种陶瓷和金属组合的金属陶瓷中,WC-Co硬质合金占据该组的绝大多数,并且在工业中起着非常重要的作用。在服役条件下,当追求WC-Co金属陶瓷在室温和高温下的高硬度和高耐磨性时,往往需要降低Co粘结剂的含量。然而,这可能会导致金属陶瓷的韧性显著下降,进而削弱强度。强烈要求同时提高硬度、韧性和强度,即在先进的WC-Co硬质合金中获得高的综合机械性能。这也是金属陶瓷材料研究领域长期面临的主要挑战。
为了提高低钴含量WC-Co金属陶瓷的机械性能,研究者们进行了广泛的研究。以WC-6Co金属陶瓷为例,Su等研究了氧化石墨烯(Go)/纳米氧化铝()复合颗粒对力学性能的影响,获得了较高的硬度值2021和韧性值11.5 MPa⋅,但强度值2480.4 MPa。Sun等在WC-6Co中添加不同含量的石墨烯,发现石墨烯有效地将WC-6Co金属陶瓷的韧性提高到13.1 MPa⋅,但硬度和强度相对较低,分别为1850 和2321.2 MPa。Huang等人通过球磨粉末混合物和真空烧结制备了具有双峰粒度分布的WC-6Co金属陶瓷,其横向断裂强度达到3077 MPa的高值,然而,断裂韧性和硬度相对较低,分别为10.6 MPa⋅ 和1570 。
总之,尽管已经尝试了各种方法来改善低Co含量的WC-Co金属陶瓷的机械性能,但是仍然很难获得同时具有高硬度、韧性和强度的优异综合机械性能。克服硬度和韧性之间的权衡以及平衡金属陶瓷材料中的强度和韧性是一大挑战。显然,在金属含量低的金属陶瓷中,由于分布在WC陶瓷颗粒中的金属的体积分数低,金属粘合剂的平均自由程小,限制了金属相的塑性变形能力和塑性适应,从而导致金属陶瓷的韧性低。
为了突破同时提高金属陶瓷的硬度、强度和断裂韧性的瓶颈,必须解决硬度和韧性之间以及强度和韧性之间的内在平衡。这需要在微观上实现金属陶瓷的协同增强和增韧。除了在我们之前的工作中提出的通过设计和增加陶瓷相与金属粘合剂之间的界面粘聚比例来增韧金属陶瓷的策略之外,本研究将集中于改变WC基体的微观结构,该基体包含明显更大质量和体积分数的低Co含量的金属陶瓷。高分辨率显微表征和模型计算将结合起来分析微尺度应力和应变分布,以揭示所开发的金属陶瓷材料中协同强韧化的微观机制。
相关研究以“Distribution of microscale stress and effect on mechanical performance of cermets with metallic nanoparticles in ceramic grains”发表在Acta Materialia上。
链接:https://www.sciencedirect.com/science/article/abs/pii/S1359645425000771?via%3Dihub
如图1(a)和补充图S1所示,当原始粉末中的碳含量低于、和碳之间的原位还原和碳化反应所需的理论值时,由η表示的缺碳相具有诸如、等组成。在合成的WC-Co基复合粉末中产生如图1(a)和补充图S1所示,当原始粉末中的碳含量低于、和碳之间的原位还原和碳化反应所需的理论值时,由η表示的缺碳相具有诸如、等组成。在合成的WC-Co基复合粉末中产生。
图一
通过在、和炭黑的混合物中具有不同碳含量的原位反应合成的WC-6Co基复合粉末和相应的烧结金属陶瓷块体材料的相分析:(a) WC-6Co基复合粉末;(b) WC-6Co基金属陶瓷大块样品。
图2中显示了使用实验部分中描述的过程设计和制备五种类型的CERMET批量样品的微观结构,这是由HAADF-STEM观察到的。已经发现,当原位反应的原材料中的碳含量低于16.89 wt.%的理论值时,纳米级颗粒就会形成烧结的Cermet散装样品的WC晶粒内。颗粒的大小和数量取决于初始碳含量,如图2(a – e)所示。根据图2(f)中的Stem-Eds分析,WC晶粒内的纳米颗粒被证实为Corich阶段。在样品中,初始碳含量为16.70 wt.%,富含纳米颗粒的平均直径为4.38 nm,其体积分数为6.77%(图2(g)和(h))。当初始碳含量增加到16.85 wt.%时,Corich纳米颗粒的平均大小增加到8.28 nm,而纳米颗粒的体积分数降至2.69%。这表明随着初始碳含量的增加,碳缺陷阶段的含量在合成的复合粉末中减少,从而减少了WC晶粒中富含共同相的成核位点的数量,因此较低的体积较低。纳米颗粒的分数和较大的尺寸。换句话说,在基于WC-CO的基于WC-CO的复合粉末中,具有较低的碳相的碳相位和成核位点,该复合粉末合成了较低的初始碳含量,从而导致高度分散的富含纳米颗粒的分布烧结的Cermet散装材料的WC晶粒中的尺寸较小。
图二
烧结WC-6Co基金属陶瓷块体样品中WC晶粒内纳米颗粒的表征:(a–e)原位反应物中不同初始碳含量样品的HAADF-STEM图像;(f)WC晶粒内纳米颗粒的STEM-EDS元素分析;(g)纳米颗粒的平均直径对初始碳含量的依赖性;纳米颗粒的体积分数对初始碳含量的依赖性。
为了表征富含共有纳米颗粒的结构,使用Cermet Bulk样品的聚焦离子束(FIB)制备了用于透射电子显微镜(TEM)的样品,初始碳含量为16.75 wt.%。图3(a)显示了纤维采样的纳米棒的形态,其直径约为100 nm。纳米棒样品的高磁化图像如图3(b)所示,标记的位置指示收集数据的区域,并在WC晶粒中观察到许多纳米颗粒。如图3(c – f)所示,将纳米棒以不同的角度倾斜以供视图,以及所选的区域电子衍射(SAED)图案以-18 °,8 °和34 °的倾斜角度显示。3(g – i)。SAED模式表明只有一个晶体结构,即,富含共同相的HCP晶体结构与WC的晶体结构相同。
图3
使用以16.75 wt .%的初始碳含量制备的金属陶瓷大块样品对WC晶粒中的富Co纳米颗粒进行TEM分析。作为例子:(a)通过FIB取样的纳米棒的形态;(b)在(a)中标记的收集数据区域的高倍放大图像;(c–f)分别在-74°、-18°、8°和62°倾斜角下观察到的图像;(g–I)倾斜角为-18°、8°和34°时的SAED模式和索引。
图4
WC颗粒中富钴纳米颗粒的晶体学分析:(a)-(c)不同投影平面上的晶体学表征,插图显示WC基体和富钴纳米颗粒的FFT和STEM-EDS分析;沿着[0001]WC方向观察到的WC和富Co纳米颗粒之间的“AB”和“BC”相界处的(a1,a2)结晶关系;沿着[1210]WC方向观察到的WC和富Co纳米颗粒之间的“DE”和“DF”相界处的(b1,b2)晶体学关系;沿[1210]WC方向观察到的WC和富Co纳米颗粒之间的“GH”和“HI”相界处的(c1,c2)结晶关系。
图5
具有不同初始碳含量的金属陶瓷样品的裂纹传播路径的机械性能和统计分析:(a)每个金属陶瓷样品的硬度和断裂韧性测量;(b)每个金属陶瓷样品的横向破裂强度(TRS)测量;(c)比较Cermet样品的硬度,断裂韧性和TRS,初始碳含量为16.75 wt.%与文献中报道的金属陶瓷的最初碳含量为16.75 wt.%[10-12,20-26]。(d)在具有不同初始碳含量的CERMET样品的机械测试后,WC经晶体断裂裂纹的统计分析(WC经晶体骨折,称为WC TF)
如图6所示,在样品的机械测试和失效后,观察和分析用不同初始碳含量制备的金属陶瓷样品的WC晶粒内的位错形态。在初始碳含量为16.70wt.%的金属陶瓷样品中(图6a),富钴纳米颗粒由于其数量大而对WC位错表现出显著的钉扎效应,因此出现具有缠结和堆积的高密度WC位错,如箭头所示。随着初始碳含量的增加,观察到WC晶粒中位错的密度和形态发生明显变化,如图6(b–d)所示。随着初始碳含量的增加,WC晶粒内的富钴纳米颗粒数量减少,纳米颗粒间距增大。因此,纳米颗粒对WC位错的钉扎作用显著减弱。位错形态从具有短运动距离的密集缠结(图6a)发展到具有局部钉扎(图6b)和更长运动距离的分散(图6c),并最终发展到具有最小阻碍的直线(图6d,其中WC晶粒不包含富Co纳米颗粒)。WC位错形貌的演变进一步表明,WC晶粒内的富钴纳米颗粒将显著影响WC晶粒的力学行为和金属陶瓷的性能。
图6
用不同初始碳含量制备的金属陶瓷的WC晶粒内的位错形态(箭头表示WC位错)。(a)16.70wt.%的初始碳含量;(b)初始碳含量为16.75wt.%;(c)初始碳含量为16.85wt.%;(d)初始碳含量为16.89wt.%
图7
WC晶粒内位错和大的富Co纳米颗粒之间相互作用的分析:
(a)WC位错与富Co相相互作用的TEM图像,插图显示了WC晶粒的选区电子衍射(SAED)图案;(b) HRTEM图像显示WC位错终止于具有大的富Co相的界面;(c)对应于(b)中区域的(0001)面的IFFT图像;(d)靠近与WC晶粒的界面的富Co相中的局部区域的放大IFFT,其中⊥表示位错;(e)对应于(b)中区域的几何相位分析;(f)WC位错和WC与富Co相界面处的应变能和应力的计算结果。
与在相界终止位错运动的大的富钴纳米颗粒相反,较小的富钴纳米颗粒(例如直径低于10 nm)通过“穿透”机制与WC位错相互作用,如图8所示。图8(a1)中的HRTEM和FFT分析确定图8中的观察方向也是[1210]WC,并且WC位错是典型的刃位错。图8 (a)和(b)示出了穿过富钴纳米颗粒的位错,并且具有位错的富钴纳米颗粒的(1010)晶面间距为2.43(图8b),其小于没有位错的相应面间距。此外,从IFFT(图8b1)观察到,当位错穿过富钴纳米颗粒时,在富钴相与WC基体之间的界面处触发新的位错,并且在富钴相内部激发位错运动。这表明穿过富钴颗粒的WC位错会导致富钴相中的晶格畸变,阻碍WC位错的运动。当WC位错以“切穿”方式与小的富Co颗粒相互作用时,这是WC晶粒上强化的来源。
图8
WC晶粒内位错和小的富钴纳米颗粒之间相互作用的分析:(a)穿过富钴纳米颗粒(用黄色箭头表示)的WC位错(用白色箭头表示)的TEM图像;(a1)WC晶粒中刃位错的HRTEM图像;(b)穿过富钴纳米颗粒的WC位错的HRTEM图像;(b1)在(b)中的(0001)晶面的相应IFFT图像。
富钴纳米颗粒通过阻碍位错运动对WC晶粒产生强化作用的同时,局部应力和应变也随之增加。用GPA分析了位错引起的应变分布,计算了位错周围的弹性应力场。图9(a1)中标记的三个区域表现出相似的应力和应变值。从图9(b1)可以看出,当WC位错穿过富Co纳米颗粒时,在富Co相和WC基体之间的界面处以及富Co相内部出现局部应变集中。评估这些区域(标记为I、II和III)中的应变能和弹性应力。为了比较,还计算了WC基体中WC位错的邻近区域中的局部应变能和弹性应力(由图9(b1)中的白色箭头指示,表示为D-E1和D-E2)。如图9(a2,b2)所示,与WC晶粒中WC位错的其它区域中的弹性应力相比,界面处和富Co相中的局部应力明显较小。这表明当WC位错穿过富钴相时,富钴相通过纳米颗粒内部的诱导位错表现出塑性调节能力,部分释放了WC位错附近区域的局部应力集中。因此,它将避免因局部应力集中而在WC晶粒内形成微裂纹。
图9
含位错和富钴纳米颗粒的WC晶粒内的微尺度应力和应变分析:(a)只有位错的单个WC晶粒的HRTEM图像;(a1)WC晶粒内仅具有对应于(a)的位错的区域的GPA图像;(b) HRTEM图像显示了穿过WC晶粒内的富钴纳米颗粒的位错;(B1)WC晶粒内区域的GPA图像,其中位错穿过对应于(b)的富Co纳米颗粒;(a2,b2)分别计算在(a1)和(b1)中标记的相应区域的应力和应变能。
图10
原位反应物中的碳含量与复合粉末中的缺碳相和烧结金属陶瓷中WC晶粒内的富钴相的量之间的关系:(a)原位反应物中的碳含量对合成的复合粉末中的缺碳相和烧结金属陶瓷中的富钴相的质量分数的影响。插图分别显示了合成的复合粉末的SEM图像和用16.70wt.%和16.85wt.%的初始碳含量制备的含有富钴相的样品的WC晶粒的TEM图像;(b)对于用不同初始碳含量制备的样品,富钴相与WC晶粒的体积比的实验测量和理论计算.
本研究在原位合成WC-Co复合粉末反应物成分设计的基础上,将特定的富Co纳米颗粒引入到金属陶瓷的WC晶粒中,并精确控制其尺寸和数量。结果,低金属含量的金属陶瓷获得了突出的综合机械性能,包括同时高的硬度、强度和韧性。该方法突破了同时提高金属陶瓷材料硬度、强度和断裂韧性的瓶颈,为解决陶瓷基复合材料力学性能之间的权衡提供了策略。这项研究的主要结论如下:
(1)对于WC-6Co金属陶瓷,作为具有低金属含量的金属陶瓷的代表性实例,通过优化用于合成WC-Co复合粉末的原位反应物中的初始碳含量,在WC晶粒内获得合适尺寸和数量的富Co纳米颗粒,在烧结的金属陶瓷块体中同时获得高硬度(1920±10.74 kgf/)、高断裂韧性(11.2±0.8 Mpa⋅ )和高横向断裂强度(3951±229 MPa)。在文献报道的金属含量相近的金属陶瓷中,综合力学性能最高。
(2)针对WC位错停滞在大尺寸富Co纳米颗粒上并穿透小尺寸Corich纳米颗粒的实验发现,建立了微观尺度下的局部应力应变模型。结果表明,由于韧性富钴纳米相的塑性调节,WC位错和富钴纳米相之间的相互作用不会引起局部应力集中。结合实验表征和模型计算揭示了富钴纳米颗粒阻碍位错运动和释放界面应力是金属陶瓷中WC晶粒协同强韧化的关键机制。
(3)定量分析了烧结金属陶瓷中WC晶粒内富钴纳米颗粒的量与合成复合粉末的原位反应物中初始碳含量之间的关系。此外,富钴纳米颗粒对金属陶瓷强度增加的贡献根据颗粒尺寸的差异和相关的奥罗万机制或切割机制进行定量区分。WC晶粒内富钴纳米颗粒对金属陶瓷强化作用的计算结果与实验测量结果一致。这种量化使得本研究能够为开发同时具有高硬度、强度和韧性的金属陶瓷材料提供指导。
免责声明:本网站所转载的文字、图片与视频资料版权归原创作者所有,如果涉及侵权,请第一时间联系本网删除。
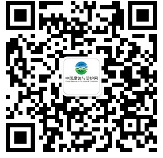
官方微信
《腐蚀与防护网电子期刊》征订启事
- 投稿联系:编辑部
- 电话:010-62316606
- 邮箱:fsfhzy666@163.com
- 腐蚀与防护网官方QQ群:140808414