增材制造(AM)为先进装备复杂高性能金属部件加工带来了巨大潜力。然而,在成型中不可避免会遗留熔池轨迹和微观缺陷。作为增材金属的本质物理印记,深入理解这些微结构如何影响材料的力学性能和服役行为,已成为其走向重大工程装备的关键问题。近日,西南交通大学、澳大利亚新南威尔士大学、中国科学院高能物理研究所、四川大学、英国曼彻斯特大学等5家单位联合,综合应用原位高时空分辨同步辐射X射线微/纳米三维成像及X射线衍射技术,首次原位追踪到不同载荷下增材铝合金内部损伤行为,揭示了熔池微结构(MPB)和缺陷在试样全寿命期内的演化过程和相互作用关系,阐明了不同加载条件下广域分布的MPB微结构和缺陷在疲劳损伤与断裂过程中的主导作用,并提出了从对MPB微结构不敏感到敏感的疲劳裂纹扩展过渡的新机制。基于这一发现,研究团队进一步引入物理信息驱动的神经网络(PINN)机器学习模型,开发了一种将三维缺陷特征与增材铝合金疲劳性能相关联的新方法。这一新结果为增材制造金属在不同应用场景的结构优化设计和部件服役性能评价提供了新的实验证据和理论参考,有望推动该技术在航空航天、轨道交通、国防等关键行业中的广泛应用。
最近,该项研究成果以“Critical damage events of 3D printed AlSi10Mg alloy via in situ synchrotron X-ray tomography”为题发表在工程结构材料顶级期刊《Acta Materialia》上。西南交通大学博士研究生吴正凯为论文第一作者(现职为日本九州大学项目助理教授,日本JSPS外籍特别研究员),西南交通大学吴圣川研究员和英国曼彻斯特大学PJ Withers院士(现职为澳大利亚莫纳什大学访问教授)为共同通讯作者,西南交通大学康国政教授和胡雅楠副教授、四川大学王清远教授、澳大利亚新南威尔士大学Jamie J. Kruzic教授和Xiaopeng Li副教授以及中科院物理所张星星研究员为共同作者。该研究得到国家自然科学基金(U2032121、12192212)和西南交大新型交叉学科培育基金联合资助。
研究背景
增材制造正以前所未有的速度推动制造业的数字化和低碳化转型,其应用前景在过去的十年间迅速拓展。当前,金属增材制造,尤其是激光粉末床熔融(L-PBF)技术,在关键工程金属合金的设计和加工方面取得了显著突破,涵盖了铝、钛、镁合金、钢铁、镍基超合金、高熵合金等。L-PBF通过高能激光束逐层熔化金属粉末,其间伴随复杂而剧烈的熔化与凝固过程,由此制备的部件中将不可避免地存在大量熔池轨迹(例如,10 mm3的L-PBF金属立方体内大约包含约104条熔池轨迹)及微观制造缺陷(全域分布,且尺寸形貌复杂)。这些熔池结构(MPB)和微观缺陷成为L-PBF金属的固有特征。除熔池内部的微观结构(如晶粒和胞状结构等)外,这些MPB结构和微缺陷在很大程度上决定着L-PBF部件的力学性能,尤其是其疲劳损伤断裂性能。然而,由于MPB和缺陷的复杂性及其跨尺度特征,长期以来在不同加载条件下量化它们对损伤失效机制的影响面临巨大挑战。此外,过去十几年的研究主要集中于控制熔池内部的多尺度微观结构来提升材料拉伸性能,而针对MPB和缺陷在不同加载条件下对疲劳性能影响的系统性研究仍不深入,极大限制了L-PBF技术在关键工程合金材料中的广泛应用。
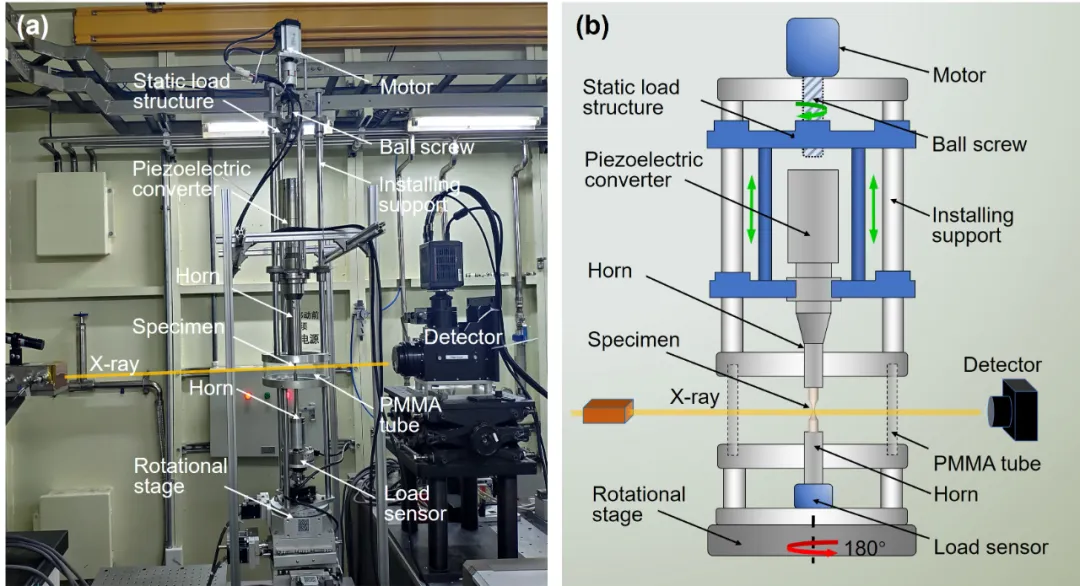
图1 基于高分辨三维成像的增材制造铝合金内部缺陷和MPB特征,以及微结构分布特征和相关力学性能
主要思路
本研究首先自主研制多功能(轴向拉伸、低周及高周疲劳)集成式原位三维成像加载装置,结合高时空分辨率原位同步辐射X射线微米成像(Micro-CT)和X射线衍射(SXRD)技术,开展了不同加载模式下增材铝合金内部微结构疲劳损伤与断裂行为的高分辨三维定量表征,以探明不同载荷历程下缺陷和MPB结构耦合机制。针对增材微结构与其力学性能的多尺度物理特征,综合采用高空间分辨纳米成像(Nano-CT)技术、EBSD和TEM等表征方法对临界损伤区域进行多模态关联表征,以阐明MPB损伤及微孔洞的形核模式,揭示不同加载模式下材料损伤破坏机制。最后,将三维缺陷特征对疲劳寿命的影响作为物理约束,进一步借助机器学习模型,建立三维缺陷特征与增材金属疲劳性能的关系,从而实现对增材材料疲劳寿命的准确预测。

图2 多功能集成原位加载系统及其原理图
研究结果
本研究系统揭示了L-PBF制造成形的AlSi10Mg合金在拉伸、低周疲劳(LCF)和高周疲劳(HCF)加载条件下内部缺陷和损伤演化过程。结果发现,在高应变加载(拉伸、低周疲劳)下,与加载方向垂直的大尺寸缺陷导致微裂纹萌生和扩展,促进缺陷快速增长与连通。在此过程中,强度更低的MPB发生更大的塑性变形,MPB内粗大的硬质Si相与相对较软的Al基体发生变形不匹配,促使MPB优先萌生微孔洞和裂纹,因此试样内部裂纹桥接和扩展主要沿着MPB进行。而在低应力加载下(高周疲劳),疲劳寿命主要受裂纹源处的临界缺陷主导,其余缺陷对疲劳性能的影响较小。另外,裂纹源缺陷的尺寸、取向、位置和形貌等特征对疲劳性能均具有显著影响。
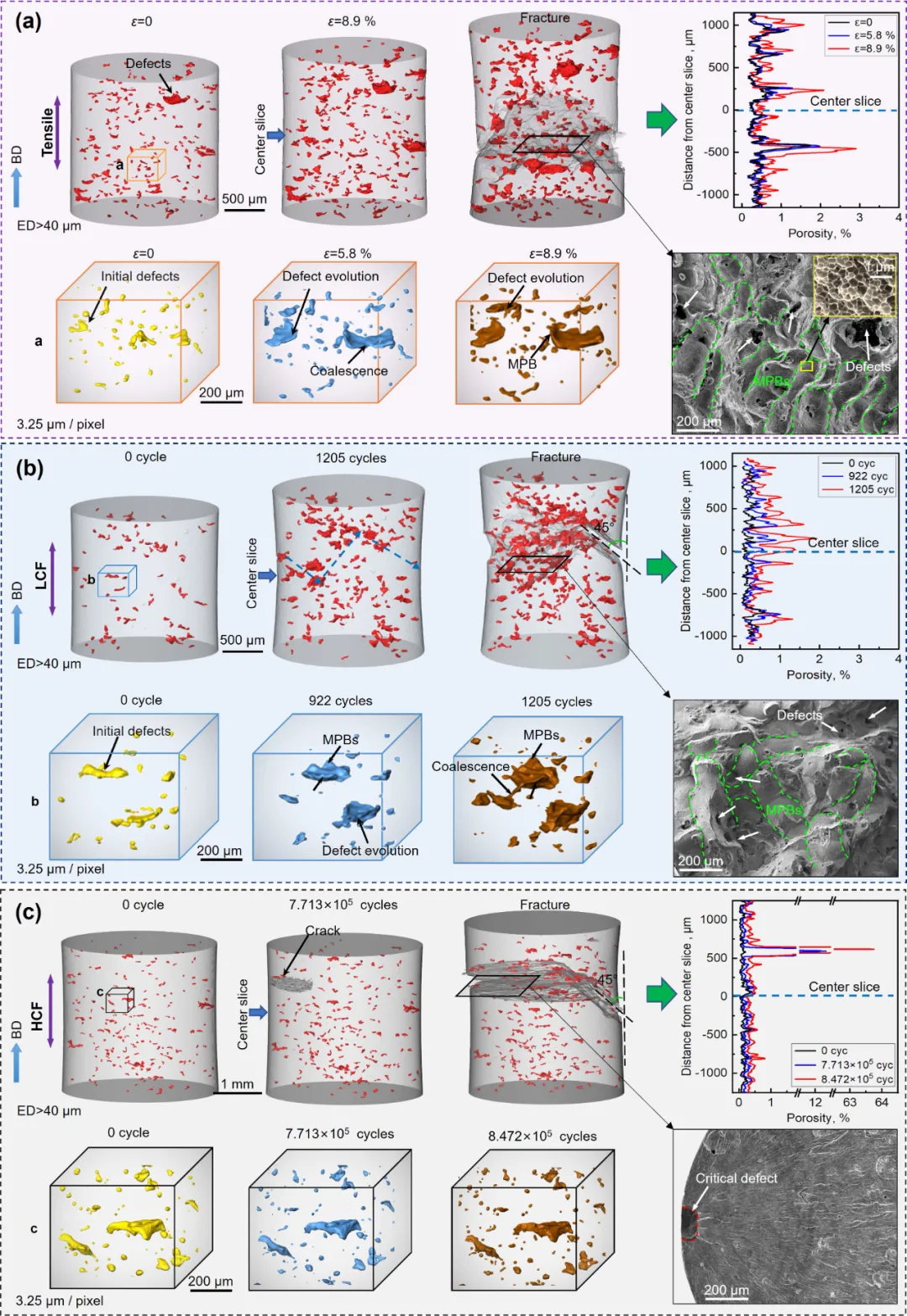
图3 增材铝合金在拉伸、LCF(σmax = 125% YS)和HCF(σmax = 60% YS)加载下内部缺陷演变与裂纹扩展行为,以及试样三维CT成像(上图)与局部放大(下图)结果、试样截面孔隙率变化曲线(右上)及相应的断口损伤特征(右下图)

图4 (a) 微空洞主要成核于拉伸和LCF样品的MPB中; (b) 试样纵截面上几何必须位错(GNDs)分布;(c) TEM观测和Si元素分布图; (d) 通过原位SXRD测量的拉伸(左图)加载下Al和Si相的应力变化以及 LCF加载期间的相应力变化(中间和右侧)
在高应变条件下,内部损伤积累逐步加剧,微空洞首先在MPB处成核,裂纹随后沿着MPB扩展;而在低应力加载条件下,表面缺陷主导了疲劳裂纹萌生过程,MPB的影响较为有限。在疲劳裂纹萌生和扩展过程中,随着塑性区的增大,裂纹表现出从对MPB不敏感逐渐过渡到对MPB敏感并沿MPB开裂的扩展机制。研究结果为增材制造构件的疲劳性能评估与工艺优化提供了新思路,指出应根据不同工程应用需求制定缺陷控制与微结构调控策略,从而实现增材金属材料的按需设计与安全评估。

图5 不同载荷历程下增材合金的损伤失效行为: (a) 拉伸、LCF和 HCF加载条件下增材合金损伤失效机制示意图;(b) 不同ΔKeff 水平下疲劳裂纹扩展行为的转变,不同裂纹长度尺度的塑性区分别显示出不同的疲劳裂纹-微结构相互作用机制
疲劳实验发现,增材金属部件的高周疲劳性能分散性显著,且主要与主导裂纹萌生的关键缺陷的物理特征相关。通过X射线三维成像、疲劳测试和断口分析,建立了关键缺陷三维特征与疲劳寿命的关联数据集,进一步开发了引入物理约束的神经网络模型(PINN),将缺陷几何特征对疲劳寿命的影响纳入损失函数,建立了一种将三维缺陷特征与疲劳性能相关联的新方法,实现了增材金属疲劳寿命的准确预测。
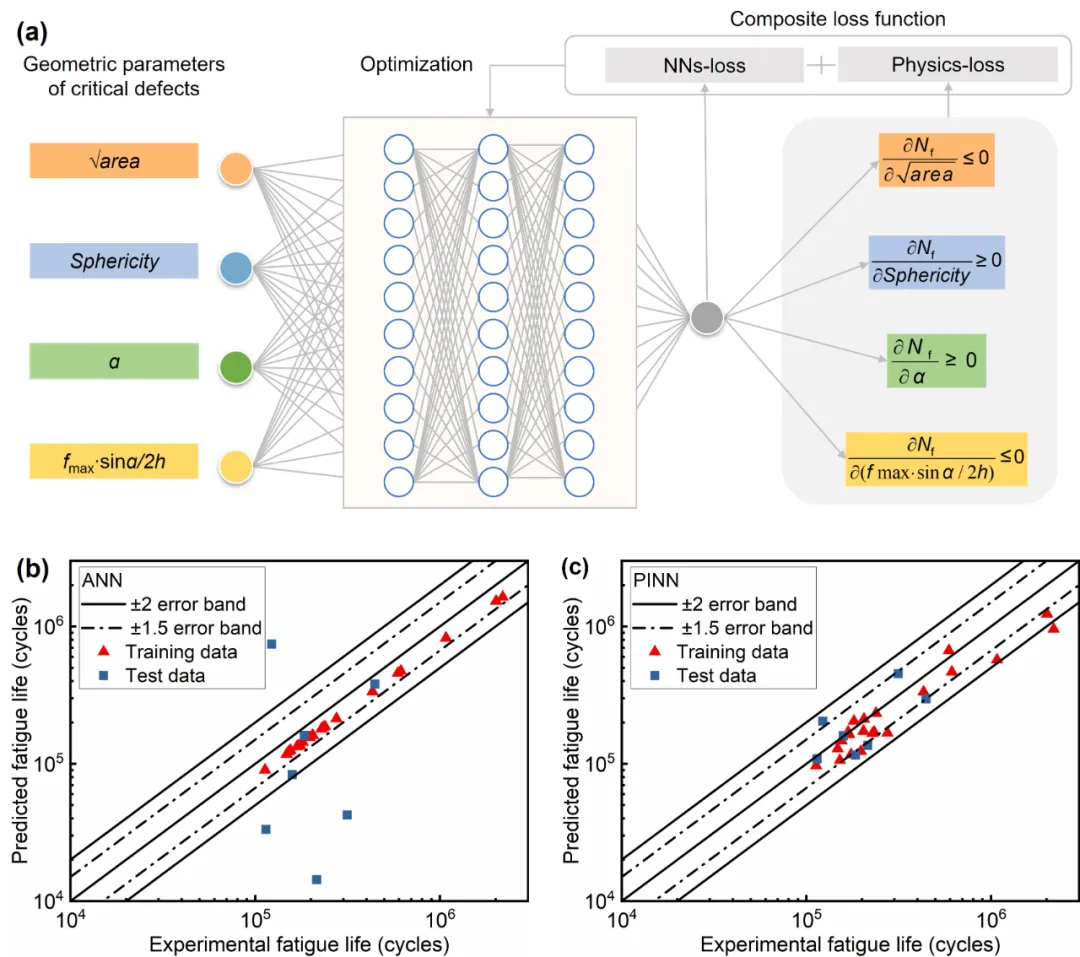
图6 基于机器学习的疲劳寿命预测:(a) 基于关键缺陷几何参数的 PINN 示意图;基于 (b) ANN 和 (c) PINN 模型的疲劳寿命预测与实验结果比较
总结与讨论
增材制造应用场景日益广泛,从功能件到关重件,从低周疲劳、高周疲劳到超高周疲劳材料部件,都具有巨大应用发展潜力,在航空航天、轨道交通、医学、国防、能源等重要行业领域被“寄予厚望”,相关理论研究、资金投入、设备研发等也与日俱增。然而,由于增材制造本身涉及参数繁多、成型机理复杂、应用场景不一、评价标准欠缺,其工程应用仍存在较大技术障碍。目前,增材制备“完美无暇”材料成为学术界和工业界的共同追求目标,研究主要集中于去除缺陷、调控组织、降低残余应力和表面粗糙度等,进而得到一种高强度、高塑形性且疲劳性能优异的构件,在此方面也取得了一定进展。但是,这种“高标准、严要求”并不总被接受,因为它会极大地提高研发和制造成本。众所周知,焊接作为主要的成型工艺之一,在工业制造中同样面对着焊接气孔、组织不均匀、残余应力等问题,但百余年来,其已广泛应用于各关键工业领域,并发挥着无可替代的作用。因此,一般认为,增材制造技术作为一种先进制造工艺,在保持对其前沿课题研究的同时,应尽可能发挥其现有技术特色。例如,不同的应用场景对材料的服役性能要求截然不同,在工业应用中,“没有问题”不可能,“问题可控”便可行。本研究正是基于此思想,综合采用原位高分辨三维成像和跨尺度关联表征系统研究了L-PBF增材AlSi10Mg合金在拉伸、低周疲劳和高周疲劳下的内部损伤演化过程和裂纹扩展机制,明确了高塑性加载下熔池微结构占主导,低应力加载下孔隙缺陷占主导的损伤断裂模式,并提出了从对熔池结构敏感到不敏感的裂纹扩展过渡的新机制,这为不同应用场景下的增材材料工艺调控与设计明确了方向:以熔池微结构调控为主以提高其强韧性,以缺陷水平控制为主以提高其疲劳寿命,从而实现面向工程应用的增材制造部件定制化设计。此外,关键缺陷与疲劳寿命(尤其是高周、超高周疲劳)密切相关,“缺陷可控”通常比“消除缺陷”更具可行性,X射线三维成像在缺陷的空间几何表征方面优势显著,随着机器学习(ML),尤其是物理信息驱动的神经网络模型(PINN)的发展,直接建立缺陷特征与疲劳性能的关系成为一种新的思路。这里需要指出的是,缺陷应不仅仅局限于通常意义上的定义,比如微观组织异性和表面粗糙度也亦应被视为缺陷。不仅如此,机器学习在处理复杂多物理场信息方面优势显著,有望建立“工艺参数-微观组织-缺陷特征-力学性能”(PSP)的定量化关系,从而促进增材制造技术的快速发展和应用,是未来增材制造材料开发、应用及性能评价过程中不可或缺的技术手段之一。
【通讯作者:吴圣川研究员wusc@swjtu.edu.cn(西南交通大学);Philip J. Withers院士p.j.withers@manchester.ac.uk(英国曼彻斯特大学)】
团队简介
近年来,西南交通大学吴圣川课题组研制了基于同步辐射光源三维成像技术的原位拉压、微动疲劳、接触磨损、轴向/旋弯疲劳及超高温/超低温/强腐蚀等先进材料结构内部损伤表征的系列原创装置,提出了增材制造和焊接构件内部损伤的图像力学方法(3D+时间+损伤),建立了应力水平-缺陷临界-疲劳寿命的三参数K-T评定图(或W-W参数模型),创立了基于先进光源的结构内部损伤原位跨尺度表征方向,入选《中国力学2035发展战略》,基于高时空分辨的原位超高周疲劳试验技术被国家标准《超高周疲劳超声疲劳试验方法》确定为第三方验证方法,相关成果在Nature子刊、Acta Mater、Int J Mech Sci、Int J Fatigue等期刊发表,多篇入选ESI高被引论文,授权发明16件,出版论著《材料疲劳损伤行为的先进光源表征技术》和《增材制造先进材料及结构完整性》,试验数据与模型被国际科研领军软件Thermo Fisher Scientific采纳,兼任Int J Fatigue编委及Tomo Mater Struct创刊编委,部分成果支撑了2022年中国质量技术一等奖(排名2)。
相关参考文献:
[1]Wu ZK, Wu SC, Qian WJ, Zhang HO, Zhu H, Chen QY, et al. Structural integrity issues of additively manufactured railway components: Progress and challenges. Eng Fail Anal 2023;149:107265. https://doi.org/10.1016/j.engfailanal.2023.107265.(综述,ESI高被引)[2]Peng X, Wu SC, Qian WJ, Bao JG, Hu YN, Huang ZX, et al. The potency of defects on fatigue of additively manufactured metals. Int J Mech Sci 2022;221:107185. https://doi.org/10.1016/j.ijmecsci.2022.107185.(ESI高被引)[3]Qian WJ, Wu SC, Wu ZK, Ahmed S, Zhang W, Qian GA, et al. In situ X-ray imaging of fatigue crack growth from multiple defects in additively manufactured AlSi10Mg alloy. Int J Fatigue 2022;155:106616. https://doi.org/10.1016/j.ijfatigue.2021.106616.(ESI高被引)[4]Wu ZK, Wu SC, Bao JG, Qian WJ, Karabal S, Sun W, et al. The effect of defect population on the anisotropic fatigue resistance of AlSi10Mg alloy fabricated by laser powder bed fusion. Int J Fatigue 2021; 151: 106317. https://doi.org/10.1016/j.ijfatigue.2021.106317.(ESI高被引)[5]Bao HY, Wu SC, Wu ZK, Kang GZ, Peng X, Withers PJ. A machine-learning fatigue life prediction approach of additively manufactured metals. Eng Fract Mech 2021;242:107508. https://doi.org/10.1016/j.engfracmech.2020.107508.(ESI高被引)[6]Hu YN, Wu SC, Withers PJ, Zhang J, Bao HYX, Fu YN, et al. The effect of manufacturing defects on the fatigue life of selective laser melted Ti-6Al-4V structures. Mater Des 2020;192:108708. https://doi.org/10.1016/j.matdes.2020.108708.(ESI高被引)[7]Hu YN, Wu SC, Wu ZK, Zhong XL, Ahmed S, Karabal S, et al. A new approach to correlate the defect population with the fatigue life of selective laser melted Ti-6Al-4V alloy. Int J Fatigue 2020;136:105584. https://doi.org/10.1016/j.ijfatigue.2020.105584.(ESI高被引)[8]Zhang H, Li RS, Liu JJ, Wang KY, Qian WJ, Shi L, et al. State-of-art review on the process-structure-properties-performance linkage in wire arc additive manufacturing. Virtual Phys Prototyp 2024;19:e2390495. https://doi.org/10.1080/17452759.2024.2390495.(邀请综述)[9]Hu YN, She YF, Wu SC, Kan QH, Yu H, Kang GZ. Critical physics informed fatigue life prediction of laser 3D printed AlSi10Mg alloys with mass internal defects. Int J Mech Sci 2024:109730. https://doi.org/10.1016/j.ijmecsci.2024.109730.[10]Wu ZK, Wu SC, Duan YS, Huang K, He WT, Du DF, et al. In situ X-ray tomography of fracture behaviour in low-porosity L-PBF AlSi10Mg alloy with laser shock peening. Virtual Phys Prototyp 2023;18:e2273955. https://doi.org/10.1080/17452759.2023.2273955.[11]Wu ZK, He ZA, Wu SC, Gao X, Lei L, Liu CK, et al. Rotating bending fatigue mechanisms of L-PBF manufactured Ti-6Al-4V alloys using in situ X-ray tomography. Int J Fatigue 2023;176:107876. https://doi.org/10.1016/j.ijfatigue.2023.107876.
[12]Wu ZK, Wu SC, Gao X, Lin Y, Xue YL, Withers PJ. The role of internal defects on anisotropic tensile failure of L-PBF AlSi10Mg alloys. Sci Rep 2023;13:14681. https://doi.org/10.1038/s41598-023-39948-z.