激光增材制造技术,是一种创新性,革命性的先进制造技术,因其高效制造复杂构件的突出优势而获得业界的广泛关注。该技术采用逐层沉积方法,能够精确制备出三维实体样件,不仅提高了制造的精细度,也极大扩展了设计的多样性及复杂度。陶瓷材料因其固有的高硬度及低韧性,很难通过传统制备技术直接一步获得复杂结构陶瓷试样。为克服以上问题,借助激光增材制造的独特优势制备陶瓷材料,逐渐成为材料领域研究热点,也是超高温候选材料制造和设计的一个新方向。熔体生长的氧化物共晶陶瓷在超高温环境中表现出突出的组织和性能稳定性,这种卓越的性能主要源于其独特的耦合生长三维网状凝固共晶组织和共晶相界面之间极低的应变能。氧化铝基共晶自生复合陶瓷具有高熔点、低密度、抗氧化、良好的高温力学性能、优异的组织和性能热稳定性等特点,有望成为超高温氧化性环境中长期服役的新一代结构材料。研究发现,借助高能激光束,在适宜的加工参数下,能够迅速实现陶瓷材料的充分熔化与凝固,从而获得熔体生长凝固共晶陶瓷。陶瓷固有的高脆性和对热冲击的高度敏感性,使其在高能激光扫描加工过程中极易产生多种缺陷。此外,陶瓷熔体的高粘度对凝固过程的精确控制提出了更高的要求,不恰当的工艺条件易引发熔化不良、层间或与基板的结合力不足、孔隙率高,裂纹和翘曲变形等一系列问题,直接影响试样的成形质量。特别是裂纹缺陷,严重制约了陶瓷加工过程的稳定性,对试样的性能造成了决定性影响。因此,在增材制造过程中,对加工参数进行细致而精确的控制,对于确保陶瓷试样的高质量和高性能至关重要。为此,科研人员进行了大量探索工作,涉及对增材制造工艺优化,增设预热装置,采用水冷基板等多种方法。近年来从材料本身出发,考虑粉末的物理和化学属性,如氧化物熔点、吸收率、流动性和粉末堆积密度等因素,通过粉末掺杂来改进激光与粉末间的相互作用也成为一个重要的技术路径。研究发现,FeCoCrNiMn高熵合金展现特有的高强度、超高的裂纹起始和裂纹扩展韧性、以及优异的延展性。FeCoCrNiMn高熵合金是最先开发设计的单相FCC高熵合金,拥有优异的塑韧性,耐腐蚀性,抗氧化性和耐高温性能,受到了众多学者的广泛关注。合金通过变形机制、位错滑动、堆积-断层形成、纳米孪晶和相变的逐步协同作用来发展抗断裂性,这些协同作用可以延长应变硬化,同时提高强度和延展性,从而获得异常的韧性,尤其适用于极端环境(如高应力应变环境)。因此,进一步探索高延展性颗粒掺杂以克服陶瓷材料固有的脆性和硬度引起的加工难题,是一项非常有意义的创新性工作。
近日,西北工业大学苏海军教授团队报道了一种通过激光粉末床熔融技术制备复杂结构氧化物共晶陶瓷的新方法。利用高熵合金粉末掺杂,通过激光粉末床熔融方法制备了氧化物共晶复合陶瓷,并进一步分析了氧化物共晶陶瓷凝固组织形成机制及复合陶瓷熔池动力学机制。通过实验优化,制备获得了尺寸约为70 mm,表面光滑且具有典型复杂结构特征(涡轮叶片形状,变截面曲边结构等)Al2O3/GdAlO3/ZrO2-HEA氧化物共晶复合陶瓷。掺杂HEA未影响凝固组织形貌,且有利于提高加工过程稳定性,获得超细层片共晶组织,共晶间距可细化至61.4 nm。相关工作以题为“Enhanced 3D printing and crack control in melt-grown eutectic ceramic composites with high-entropy alloy doping”的研究论文发表在Journal of Materials Science & Technology, 2025, 209: 64-78。https://doi.org/10.1016/j.jmst.2024.04.076
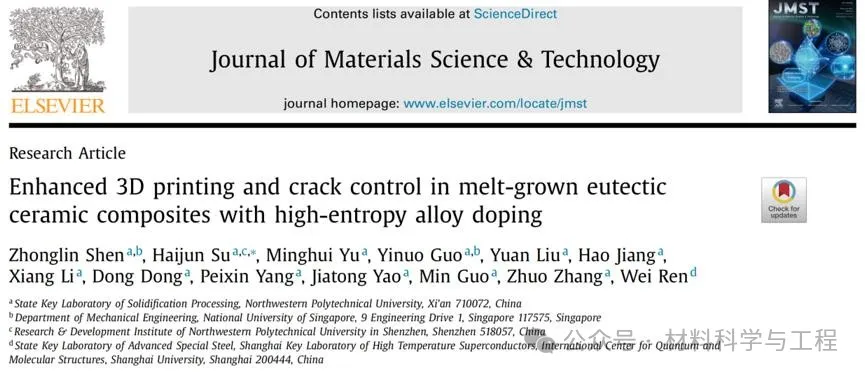
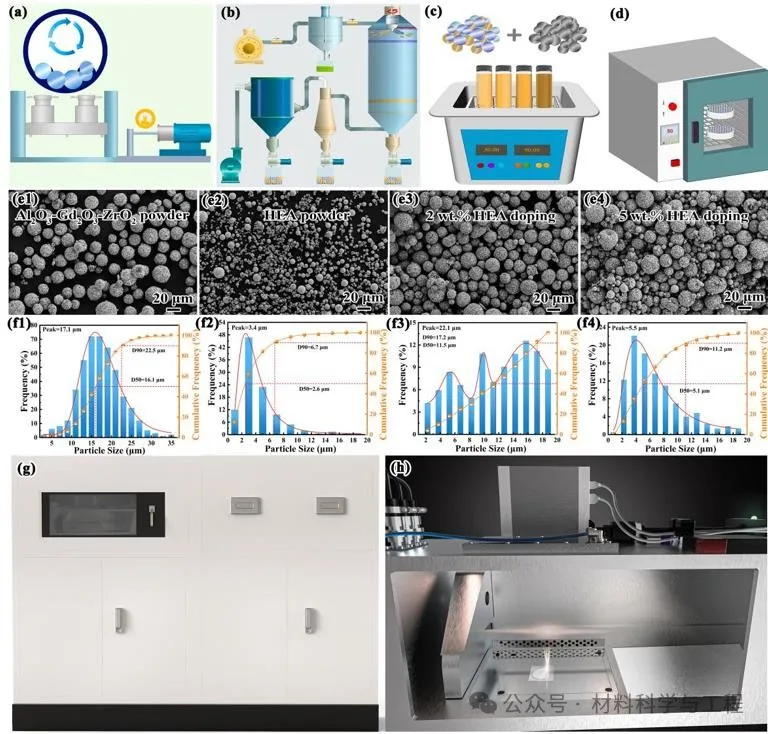
图1 激光粉末床熔融制备共晶复合陶瓷示意图: (a) 行星球磨混合三元陶瓷粉末, (b) 高速离心喷雾造粒制备球形三元共晶配比复合陶瓷粉末, (c) 超声振动混合获得HEA掺杂的均匀混合的粉末材料, (d) 烘箱干燥粉末, (e1-e4) 不同粉末颗粒形貌, (e1) 三元陶瓷粉末, (e2) HEA粉末形貌, (e3) 2wt.% HEA混合粉末形貌, (e4) 5wt.% HEA混合粉末形貌, (f1-f4) 对应粉末的粒度分布, (g) 自主设计研发的LPBF一体化装置, (h) LPBF加工过程。实验采用自主设计研发的氧化物陶瓷LPBF装备(配备二氧化碳激光器,激光波长10.6 μm, 最大功率650 W)。陶瓷粉末材料为喷雾造粒法制备的具有三元共晶配比的Al2O3-Gd2O3-ZrO2陶瓷粉末,复合粉末呈球形或近球形,粉末粒度D90=22.5 μm。HEA金属粉末为气雾化法获得的CoCrFeMnNi球形金属粉末,粉末粒度D90=6.7 μm。混合粉末进行LPBF加工制备,激光功率200-300 W, 扫描速率100-450 mm/s。高能激光器快速扫描下,陶瓷粉末材料能够完全熔化,自生复合,层层熔覆成形三元共晶氧化物陶瓷。由于金属材料对二氧化碳较低的吸收率,HEA颗粒未完全熔化,对共晶陶瓷凝固组织形貌影响不大。
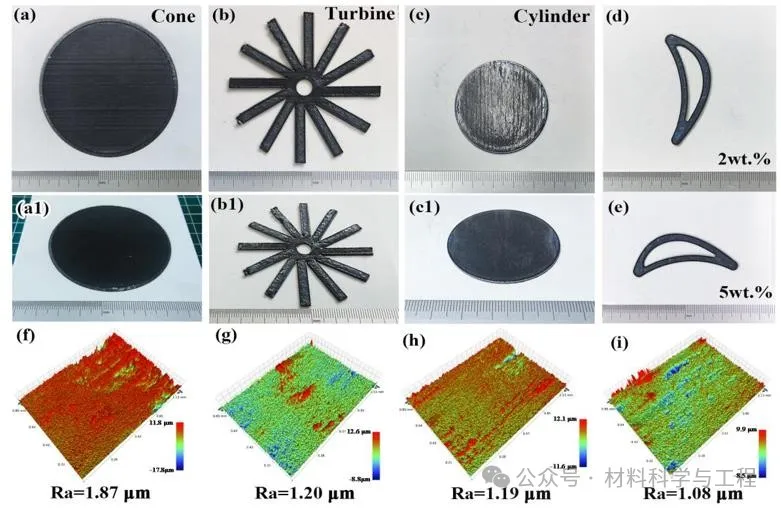
图2 不同参数LPBF制备的复合陶瓷试样形貌: (a-a1) 300 W, 300 mm/s, 7层, 6wt.% HEA, 最大直径为70 mm的变截面曲边圆柱体, (b-b1) 200 W, 200 mm/s, 10层, 8wt.% HEA粉末, 最大宽度为70 mm的涡轮状试样, (c-c1) 200 W, 200 mm/s, 12层, 5wt.% HEA粉末掺杂, φ45 mm,高度为1.2 mm的圆柱体试样, 掺杂不同含量HEA粉末的涡轮叶片状共晶复合陶瓷试样形貌, (d) 2wt.%, (e) 5wt.%, (f-i) 陶瓷试样表面粗糙度: (f) 300 mm/s, (g) 350 mm/s, (h) 400 mm/s, (i) 450 mm/s, HEA粉末掺杂含量6wt.%, 激光功率300 W。HEA粉末掺杂有效减少了加工过程中粉末飞溅现象,降低了其对后续铺粉及加工过程的不良影响。HEA粉末掺杂后能够有效改善均匀平整粉床的铺设,对激光快速扫描及凝固过程的稳定性有很大提高,能够有效抑制分层、变形或裂纹等缺陷。试样的均匀性有了显著提升,表面粗糙度能够达到1.08微米。采用LPBF方法结合高熵合金(HEA)粉末掺杂技术,成功制造出了大尺寸陶瓷复合材料试样。试样长度或直径达到约70 mm,展示出复杂的涡轮结构形貌及变截面曲边结构特征。该共晶复合陶瓷是目前利用LPBF直接制备出的具有较大宽高比的氧化物共晶陶瓷试样,代表了大尺寸熔体生长陶瓷领域的一项新突破。
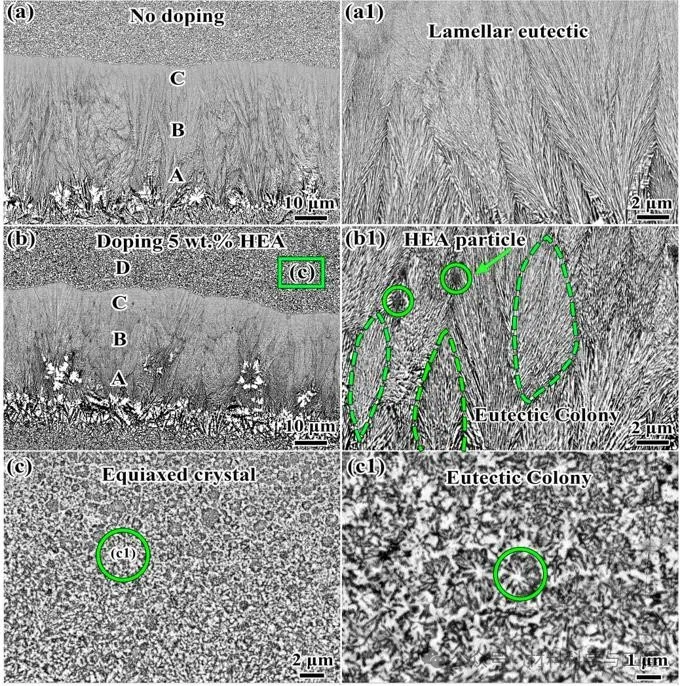
图3 HEA粉末掺杂前后复合陶瓷试样微观组织形貌对比: (a-a1)未掺杂HEA粉末的三元共晶陶瓷组织形貌, (b-b1) 掺杂5wt.% HEA制备的共晶复合陶瓷组织, LPBF加工参数相同, 300 W, 300 mm/s, (c-c1) 区域D的组织形貌。通过LPBF技术制造的陶瓷复合材料,无论是否掺杂HEA颗粒,所得陶瓷均展示出典型的三元共晶微观组织特征。在沉积层的下部,均呈现出带状结构特征,呈现超细的层片共晶组织形貌,共晶间距沿沉积方向自下而上逐渐细化。该区域存在较高的温度梯度和较低的凝固速率,温度梯度与凝固速率的比值达到最大,促进超细层片共晶组织的形成。熔池的顶部区域,温度梯度降低而凝固速率大幅增加,呈现出超细的等轴枝共晶组织形貌特征。
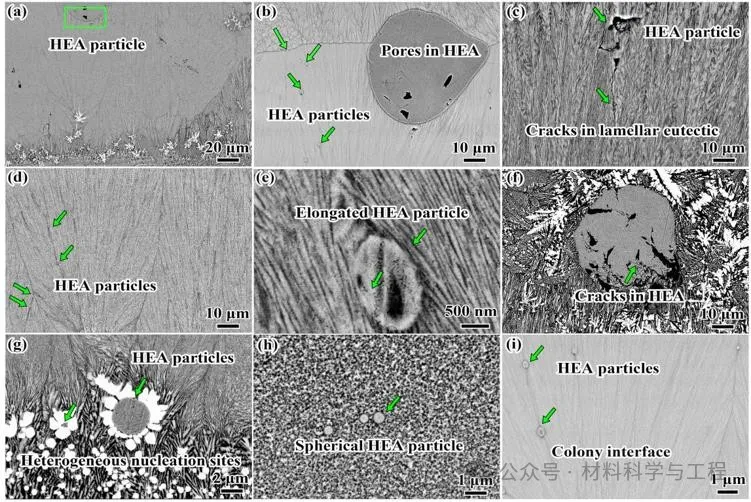
图4 含量为6 wt.% HEA粉末掺杂的共晶陶瓷微观组织及裂纹形貌: (a) 250 W,250 mm/s共晶复合陶瓷的微观组织, (b) 团聚合并的大尺寸HEA颗粒, (c) HEA颗粒附近裂纹偏转, (d-e) 小尺寸HEA颗粒弥散分布在具有超细层片组织的共晶团界面处, (f) 内部有裂纹扩展的HEA颗粒, (g) HEA颗粒作为共晶陶瓷初生相的异质形核质点, (h) 共晶陶瓷中等轴共晶组织间分布的微小球形HEA颗粒, (i) 椭球形HEA颗粒弥散分布于层片共晶微观组织中。沉积层顶部出现不规则的HEA粉末,体积较大,直径约48.2 μm,远大于原始粉末颗粒(1-20 μm)尺寸。同时,直径约为1.1 μm的更细小的粉末分散在共晶晶团界面处。界面处的HEA粉末颗粒能够阻碍裂纹的传播。另一方面,在共晶陶瓷复合材料凝固过程中,部分未熔的HEA颗粒内部呈现裂纹、不规则孔洞缺陷,该颗粒内部缺陷的形成,吸收了界面应变能及裂纹扩展能,有效抑制凝固陶瓷内部的裂纹缺陷。由于HEA颗粒良好的热导率,掺杂的未熔化HEA颗粒在减少陶瓷复合材料内部的热累积、降低热应力集中进而减轻裂纹缺陷方面有显著效果。一部分HEA颗粒可以在等轴晶团中弥散分布,形成规则的球形形貌特征。一些更细小的颗粒则呈现沿着层片组织,随熔池内部的热流方向,呈拉长的椭球状形貌特征,沿着热流方向向熔覆层顶部延伸。颗粒变形过程中能够有效释放陶瓷组织内部的各组成相生长过程界面不匹配造成的应力应变。
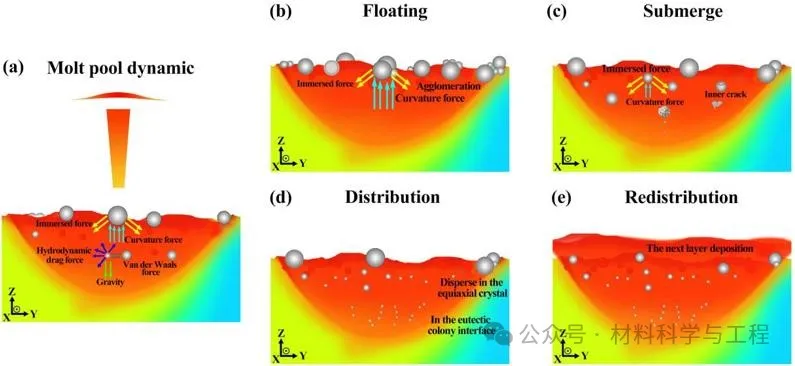
图5 熔池动力学示意图:(a) 熔池中的主要力, (b) 熔池表面的大尺寸HEA颗粒运动, (c) 浸入熔池中的小尺寸HEA颗粒, (d) 熔池不同区域的小尺寸颗粒分布, (e) 下一层熔覆后熔池表面的HEA颗粒的再分配采用激光粉末床熔融技术制备氧化物共晶陶瓷复合材料的过程中发现,较大的球形或近球形HEA颗粒主要集中在熔覆层顶部,而更细小的HEA颗粒则弥散分布在熔覆层中。较大的颗粒需要更多的动能来超越这个表面的“能量障碍”,因此它们更有可能漂浮在熔池表面。较小的颗粒由于有效浸没力和熔池表面的能量障碍而被保留在熔池内。颗粒团聚现象是不理想的。在逐层增材制造共晶陶瓷复合材料过程中,先前熔覆层表面的颗粒大多会被当前熔覆层的熔体完全包裹并重熔。通过快速激光扫描熔化过程,这些粉末颗粒融入熔池,并防止了颗粒的进一步团聚,HEA颗粒得以在熔覆层中再分配并重新弥散分布。因此,适当的激光扫描速率和激光重熔工艺可以显著减少熔池表面HEA颗粒的团聚现象。该研究综合分析了激光粉末床熔融增材制造氧化物共晶复合陶瓷中HEA粉末对成形质量及凝固组织的影响规律,为激光增材制造大尺寸复杂形状熔体生长共晶陶瓷提供了一种创新思路。利用HEA颗粒掺杂技术实现了复杂结构凝固共晶陶瓷的高效率高质量成形,为激光增材制造在凝固陶瓷领域的应用提供了更多数据及理论支持。苏海军,西北工业大学长聘二级教授、博士生导师。国家级领军人才,国家优秀青年科学基金获得者,中国有色金属创新争先计划获得者,入选国家首批“香江学者”计划,陕西省“青年科技新星”、陕西高校青年创新团队学术带头人和陕西重点科技创新团队带头人。长期从事先进定向凝固技术与理论及新材料研究,涉及高温合金、高熵合金、超高温复合陶瓷、生物陶瓷、钙钛矿太阳能电池、结构功能一体化复合材料以及定向凝固与增材制造技术等。主持包括国家自然基金重点、优青等7项国家基金在内的30余项国家及省部级重要科研项目,在Nano Energy,Advanced Functional Materials,Nano Letters,Composites part B: engineering,Additive manufacturing等知名期刊发表论文160余篇。获授权中国发明专利50余项以及3项美国发明专利。参编专著3部。获陕西省科学技术一等奖、二等奖,中国交通运输协会科学技术二等奖,陕西高校科学技术研究优秀成果特等奖,陕西省冶金科学技术一等奖,全国有色金属优秀青年科技奖和陕西青年科技奖各1项