结构钢,如AISI 321奥氏体不锈钢(321钢),广泛用于各种海上动力和机械设备。在服役期间,这些海上结构,如风力涡轮机塔架、导管架平台和桥梁,将不可避免地受到海水和盐雾环境的腐蚀,同时还会面临海浪、强风暴甚至海上地震导致的高周疲劳风险。因此,这些海上钢的耐腐蚀性和抗疲劳性都需要提高,以延长其使用寿命。
图2显示了部分钢基材HEA涂层的初始微观结构。在图2a中,显示了FeCrCoMnNi HEA粉末和涂层的XRD图谱,两条曲线分别呈现了对应于晶平面(111)(200)(220)(311)和(222)的五个衍射峰。此外,粉末和涂层的晶体结构都是面心立方(FCC)。这些结果表明,在SLM过程中,FeCoNiCrMn HEA粉末中的原始催化裂化单相得以保留。这种单相催化裂化微观结构与激光熔覆或激光定向能量沉积的对应物一致。然而,与粉末相比,涂层试样的位移(111)和(200)峰角度更高,显示出平面间距和晶格参数的增加。在以前的工作中也报告了类似的结果。
图3描述了预腐蚀前后涂层和未涂层321钢沿深度的显微硬度变化。显然,321钢基体在预腐蚀前不同深度的显微硬度大致保持不变(180~190 MPa)。相比之下,未腐蚀涂层钢顶面的显微硬度估计约为 260 MPa,然后随着深度增加到120 μm,显微硬度呈明显下降趋势。例如,未腐蚀涂层钢在120 μm深度处的显微硬度约为210 MPa。这种显微硬度下降趋势的深度范围与粗柱状晶粒分布的深度明显一致(图2c),因此该深度范围内显微硬度的降低应该是由于固溶溶解度不同。
实际上,腐蚀损伤的特征一般是试样表面存在一些大小不一的腐蚀坑,这些腐蚀坑会破坏表面光滑度,从而增加表面粗糙度,如图4所示。此外,在被腐蚀性溶液侵蚀后,涂层表面变得松动,这将降低试样表面的显微硬度,正如以前的工作所报道的那样。此外,预腐蚀后涂层样品显微硬度的突然增加点位于120 μm的深度,低于未腐蚀样品的微观硬度(140 μm)。因此可以推断,涂层深度约为20 μm的表面积被预腐蚀损伤去除。
施加的应力幅度与失效循环次数(S-N)曲线的关系以及未涂层钢和涂层钢的相应定量统计结果如图6所示。在图6a中,可以清楚地观察到HEA涂层和预腐蚀对抗疲劳性的影响。具体而言,在相同的应力幅值下,疲劳寿命(Nf)的涂层钢高于未涂层的钢。图6c和d显示了腐蚀引起的疲劳寿命下降的定量幅度,清楚地表明了防腐对抗疲劳性的负面影响。将相同应力幅下未腐蚀样品和腐蚀样品的疲劳寿命之差除以未腐蚀样品的疲劳寿命,得到红色数结果。因此,图6c和d也表明,高熵合金涂层对疲劳寿命的预腐蚀损伤的保护作用非常显著。
图7显示了未涂层和涂层钢试件的宏观断裂形态。显然,预腐蚀后样品表面不如未腐蚀样品光亮,并且在腐蚀样品表面也观察到腐蚀坑。经过后续的疲劳试验,涂层的疲劳区占断裂总长度的9/10,而未涂层钢的疲劳区占断裂总长度的4/5。此外,一旦试样表面出现腐蚀坑,涂层钢和未涂层钢的疲劳区分别减小到断裂总长度的4/5和1/2,而瞬时裂纹面积增加,表明预腐蚀后的疲劳寿命降低。
图8显示了预腐蚀前后未涂层和涂层试样疲劳断裂形态的SEM图像。总体而言,腐蚀试样的断裂形态与未腐蚀试样相似。这是因为钢通常不透气和不透水,腐蚀只发生在试样表面,试样内部不会发生化学反应或物理反应。因此,腐蚀后试样内部的机械性能将大致保持不变。换言之,除了表面几何形状外,预腐蚀对试样内部材料特性的影响可以忽略不计。
图9显示了应力幅值为110 MPa的预腐蚀疲劳试验前后涂层钢的反极数(IPF)和相应的内核平均取向误数(KAM)图。显然,涂层试样外层的晶粒尺寸明显高于近基材的晶粒尺寸,预腐蚀疲劳试验前后晶粒尺寸没有明显变化。这是因为预腐蚀和疲劳对试样的损伤以及疲劳加载过程中累积的应变主要积聚在试样表面,因此对整体晶粒微观结构影响不大。然而,预腐蚀前后的涂层宽度从164.2 μm减小到149.1 μm,表明预腐蚀对样品的破坏主要类型是积聚在涂层表面。
具体而言,在预腐蚀之前,HEA涂层表面的显微硬度远高于钢基体(图3),表现出更好的抗变形性。这也是涂层试样的疲劳寿命高于未涂层试样的原因。在这种情况下,疲劳载荷会使钢基体在未腐蚀样品中的涂层之前变形,导致钢基体中严重的应变积累。相反,预腐蚀后,涂层的显微硬度和深度显着降低(图3),表明抗变形能力显着降低。因此,由于直接施加的部位是疲劳载荷,被腐蚀样品中的涂层会在钢基体之前变形,从而导致疲劳寿命的降低。
结语 Conclusions 在这项工作中,对未涂层的321钢和激光增材制造的FeCrCoMnNi高熵合金(HEA)的对应材料进行了盐雾环境中的预腐蚀和随后的高周疲劳试验。对不同阶段的钢试件进行微观结构表征,揭示高熵合金涂层和预腐蚀对321钢抗疲劳性能的影响。 (1) SLM是一种在钢基体上制备HEA涂层的有效技术,涂层的相应晶粒微观结构主要表现为基体附近有细小的柱状枝晶,试样表面附近有较粗的柱状枝晶,导致涂层强度高于钢基体。 (2) 涂层后321钢基体的腐蚀和疲劳性能显著增强,这应该是高熵合金涂层强度更高、位错动能更高、腐蚀膜形成速率更高耦合作用的结果。 (3) 预腐蚀会降低高熵合金涂层的机械性能和深度,导致主要累积应变分布从钢基体过渡到涂层。因此,预腐蚀可能会对涂层钢的抗疲劳性造成重大损害。 (4) 预腐蚀后,不同应力幅值下,无涂层钢和涂层钢的疲劳寿命分别降低了18.2%~38.8%和34.4%~42.6%。因此,HEA涂层被认为有望成为海上结构钢的有效涂层。
免责声明:本网站所转载的文字、图片与视频资料版权归原创作者所有,如果涉及侵权,请第一时间联系本网删除。
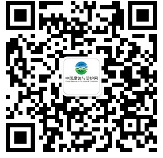
官方微信
《腐蚀与防护网电子期刊》征订启事
- 投稿联系:编辑部
- 电话:010-62316606
- 邮箱:fsfhzy666@163.com
- 腐蚀与防护网官方QQ群:140808414