镁(Mg)合金作为最轻的工程金属材料,被誉为“21世纪的绿色工程材料”,在汽车、轨道交通、航空航天、国防和军事装备等方面有着广阔的应用前景。开发高强度、高延展性镁合金是承载部件应用的热点,也是一个永恒的研究热点。目前,90%以上的镁合金产品是采用古铸造法制备的,镁合金由于其固有的六方密排(HCP)晶体结构,通常表现出较差的变形能力。然而,采用铸造方法制造大型部件时,不可避免地存在以下问题:(1)由于熔体体积大,冷却速度慢,导致晶粒粗大,力学性能差;(ii)不均匀的溶质场和流场导致宏观偏析、缩孔等铸件缺陷频发,因此通常采用后续的塑性变形来改善铸件缺陷,提高力学性能;(三)由于特殊大型模具的要求,研发周期长。此外,铸造工艺存在设计自由度有限、产品合格率低、材料利用率低、能耗高、污染重等缺点。因此,迫切需要开发新的镁合金制造方法来克服上述问题。
铸造工艺属于成型制造,机械加工属于减法制造,是满足产品尺寸和表面精度的必要条件。相比之下,增材制造(AM)工艺是一种年轻而蓬勃发展的先进制造技术,它通过逐点、逐轨道、逐层添加材料来制备部件。因此,增材制造工艺具有以下优点:(1)由于极端的微区冶金凝固条件,冷却速度快,导致微观组织精细,强度高;(ii)通常几百微米大小的小熔池导致成分分布均匀,没有宏观偏析;(三)研发周期短。此外,增材制造工艺由于具有层状切片的特点,理论上可以加工任何大型复杂形状,材料利用率高,制造精度高。采用增材制造技术制造金属部件,具有零件集成化、重量减轻、缩短周期、提高使用性能、近净成形和材料损耗低等明显优势。因此,采用增材制造技术制备镁合金部件具有很好的工程应用前景。
主流的金属增材制造技术主要包括三种工艺:采用粉末床的激光粉末床熔合(LPBF)、采用粉末给料的激光定向能沉积(LDED)和采用送丝的丝弧增材制造(WAAM),其中LPBF具有最高的冷却速度(~ 106 K/s)和制造精度(±0.1 mm)。尽管镁合金粉末具有易燃易爆的特点,但近年来镁合金的LPBF研究受到了广泛的关注。然而,目前对镁合金LPBF的研究主要集中在传统的商业铸造镁合金系列(如纯Mg、AZ91D、AZ61、ZK60、WE43)上,面临着易形成粗柱状晶粒、易开裂、气孔缺陷多、强度和延展性有待进一步提高等挑战。与上述工业镁合金相比,Mg- gd基稀土镁合金具有两大明显优势:高室温抗拉强度(500 MPa比300 MPa)和优异的耐热性(使用温度从150℃提高到300℃)。在前人的工作中,已成功研制出高强度、耐热的变形Mg-Gd-Y-Zn-Mn合金。例如,mg - 12.6 - gd - 1.3 - 0.5 - 0.9 -锌- y - mn (wt. %,整个文本在重量百分比)合金显示超高屈服强度543 MPa (y),极限抗拉强度(ut) 564 MPa的但低伸长(EL)只有1.2%的热挤压后,冷轧10%,2%冷拉伸和老化过程,mg - 12 - gd - 2 - y - 1 -锌- 0.5 - mn (GWZ1221M)合金展览y 427 MPa, UTS 509 MPa,相对较高的EL挤压和peak-aging治疗后的5.1%。
众所周知,由于Zr元素具有较高的凝固生长限制因子(GRF,又称Q值),是铸造Mg-RE合金中常用的晶粒细化元素。Zr元素对LPBF制备的Mg-Gd基合金也有明显的细化作用。Mn元素对铸态Mg-RE合金晶粒细化作用不明显,但固溶热处理过程中α-Mn颗粒析出,使挤压态Mg-RE合金晶粒细化。另一方面,Mn元素可以增强耐蚀性,其成本明显低于Zr元素。更重要的是,与Zr一样,Mn也可以与Mg发生包晶反应,所以Mn的加入也可能产生一定的晶粒细化效果。然而,在Mg-Al-Zn基合金中添加Mn则表现出相反的晶粒细化效果:铸态Mg-8.89Al-0.45Zn-0.19Mn (AZ91D)合金呈现出极其细小均匀的等轴晶粒,平均晶粒尺寸仅为1.2μm,而铸态Mg-10.6Al-0.6Zn-0.3Mn (AZ111)合金呈现出与BD平行的粗柱状晶粒,平均晶粒尺寸为28μm。LPBF工艺的冷却速度明显高于常规铸造工艺,但Mn元素是否能细化铸态镁合金的晶粒尚不清楚。目前还没有关于含锰Mg-Gd基合金LPBF的报道。因此,选择具有良好强度和延展性的GWZ1221M合金制作定制预合金粉末,然后使用LPBF-AM工艺打印样品,以表征成型合金的独特组织和力学性能。析出强化对Mg-Gd基合金的抗拉强度贡献最大,因此后续的固溶和时效热处理可以改善组织,提高力学性能。
在此,上海交通大学材料科学与工程学院邓庆琛教授团队进行了研究,相关研究成果以题为“Developing a novel high-strength Mg-Gd-Y-Zn-Mn alloy for laser powder bed fusion additive manufacturing process”发表在期刊Journal of Magnesium and Alloys上。
链接:https://www.sciencedirect.com/science/article/pii/S2213956723002293
200-300目预合金粉末形貌如图1所示。大多数粉末呈球形,但仍有一些卫星状粉末和不规则形状粉末存在(图1a)。平均粒径约为64μm。由于离心雾化过程的高冷却速率,粉末呈现出精细的等轴晶粒形貌(图1b)。共晶相主要沿晶界分布,粉末晶粒尺寸约为2 ~ 4μm。此外,粉末表面还会出现一些细小的球形氧化物,这些氧化物是在惰性化过程中形成的,以保证储存、运输和人类搬运过程中的安全。
GWZ1221M合金粉末态、成品态和LPBF-T4态下的XRD图谱如图2所示。GWZ1221M粉末由α-Mg基体、β-(Mg,Zn)3(Gd,Y)次级相和少量Y2O3氧化物组成。与含Mg、Gd或Zn的氧化物形成相比,Y2O3氧化物的形成焓最低,有利于Y2O3氧化物的形成。由于Y2O3氧化物的熔点高达2410℃,因此在LPBF及后续热处理过程中始终存在Y2O3氧化物。LPBF工艺与离心雾化工艺一样,只是将预合金粉末重新熔化形成熔池,并进行快速凝固,因此铸态合金的相组成与粉末相组成相同。经过适当的固溶热处理后,β-(Mg,Zn)3(Gd,Y)二次相溶入α-Mg基体或转变为长周期有序堆积(LPSO)结构。Mg-RE-Zn基合金中普遍存在LPSO结构,可以提高合金的综合力学性能。结果表明,LPBF-T4合金由α-Mg基体、LPSO组织和Y2O3氧化物组成。时效热处理在LPBF-T6合金中产生了大量棱柱状时效析出物,但纳米级的析出物难以通过XRD检测到,需要通过TEM识别。
图1所示。200-300目预合金粉末的形貌。
图2所示。GWZ1221M合金粉末态、铸态和LPBF-T4态下的XRD谱图。
图3为构建高度分别为6 mm和10 mm的GWZ1221M立方体样品的宏观OM图像。低建高为6 mm的建方样品内部无裂缝,高建高为10 mm的建方样品内部有明显裂缝。建筑高度越高,热应力积累越大,导致开裂敏感性越高。仅通过调整激光能量密度是无法避免开裂的,需要通过改进3D打印机或改变合金成分来避免。特殊的镁合金3D打印机应该有更高的预热温度,如400℃的构建平台,或有两个激光与另一个激光加热,以原位热应力消除。此外,应选用G10K合金等本征延展性较高的合金,以避免产生不良裂纹。铸态GWZ1221M合金由于锁孔不稳定而不可避免地存在一些小的孔洞缺陷,并被凝固前沿捕获。值得注意的是,构建样品边缘的孔缺陷直径明显大于内部的孔缺陷,这主要是由于双向扫描降低了样品边缘的扫描速度,导致激光能量密度增加。通过激光离焦和优化工艺参数,制备的GWZ1221M合金的相对密度高达99.85%。对于低沸点、高饱和蒸汽压的镁合金,由于Mg元素不可避免的汽化,在构建样品中不可避免地存在少量孔隙缺陷,但优化激光能量密度可以消除大部分孔隙缺陷。优化造腔风场,及时去除汽化产物,或提高粉床和造平台的预热温度,都有利于减少气孔缺陷。值得注意的是,由于过多的激光能量输入而产生的少量孔隙缺陷(< 1%)不会大大降低拉伸性能,但可能对疲劳性能有害。
GWZ1221M合金的SEM图像如图4所示,可以看到合金的晶粒和二次相的形貌。熔池边界用黄色虚线表示。熔池的深度一般大于宽度(图4a),为锁孔熔化模式。由于冷却速率最高,熔池边界呈现出最细的等轴晶粒(图4b)。除了凝固过程沿晶界形成网状的β-(Mg,Zn)3(Gd,Y)次相外,固相转变形成的一些细小点状的β-(Mg,Zn)3(Gd,Y)次相也分布在晶粒内部(图4b-d)。在熔池边界附近的晶粒内部出现了一些平行的片层(图4c, d),这是由于枝晶臂在给定方向上优先生长造成的。此外,少量大小为几微米的不规则片状相(如图4c中白色箭头所示)均匀分布在合金内部,这被确定为不需要的Y2O3氧化物。Y2O3氧化物会降低材料的力学性能,减弱时效析出电位,在今后的工作中应加以避免。
通过EBSD观察进一步揭示了铸态GWZ1221M合金内部晶粒的形貌和取向,如图5所示。合金由随机取向的细小等轴晶粒组成,平均晶粒尺寸为4.3±2.2 μm(图5a)。在铸态GWZ1221M合金中未观察到大柱状晶粒,而在铸态WE43合金中却经常观察到大柱状晶粒。由{0001}极图可知,构建后的合金几乎不存在织构,最大织构强度仅为2.95泥(多重均匀分布,图5b)。
根据参考文献,将铸态GWZ1221M合金在515℃固溶12 h,即可得到铸态t4合金。铸态t4合金的枝晶晶粒仍然粗大,平均晶粒尺寸略有增大,达到182.4±57.2μm。β-(Mg,Zn)3(Gd,Y)相消失,出现大量的X相(又称块状LPSO)和片层状LPSO结构以及少量立方相。X相从晶界开始形核,向晶粒内部生长,而晶粒内部的片层状LPSO结构的生长方向与晶粒基面平行。固溶处理的Mg-RE基合金中经常发现立方相,确定为REH2而不是MgH2。热力学上,RE的电负性比Mg低,因此对h的结合倾向更高。尽管立方相对力学性能不利,但该相的数量相对较少,难以完全消除。
铸态GWZ1221M合金与铸态GWZ1221M合金的显微组织存在显著差异,因此铸态GWZ1221M合金的最佳固溶热处理条件应与铸态GWZ1221M合金不同。通过对铸态Mg-Gd基合金固溶热处理条件的优化,铸态Mg-Gd基合金固溶热处理温度低于铸态Mg-Gd基合金,因为铸态Mg-Gd基合金晶粒更小,二次相更少。因此,构建的GWZ1221M合金的最佳固溶热处理条件为450℃×12 h (LPBF-T4态),与构建的GWZ1031K合金相同。
为了得到LPBF-T4 GWZ1221M合金的峰时效条件,测量了175℃和200℃下的时效硬化曲线,如图8所示。175℃和200℃时效硬化曲线特征参数如表2所示。铸态GWZ1221M合金的硬度为112.9±0.9 HV,硬度下降至96.7±0.4 HV,主要是由于硬脆相β-(Mg,Zn)3(Gd,Y)析出和残余应力释放所致。随着时效时间的延长,硬度持续稳定上升,达到峰值后逐渐降低。与200℃相比,175℃时效可以产生更强的析出电位和较大的硬度增量(34.0 HV vs . 30.2 HV),但原子扩散速度变慢,达到硬度峰值的时间变长(256 h vs . 32 h),硬度增量与挤压态GWZ1221M合金的硬度增量(33.3 HV)相当,表明Mg-Gd基合金具有优异的时效硬化能力。为了追求优异的力学性能,LPBF-T4合金的时效条件选择为175℃×256 h (LPBF-T6态)。在未来的实际工程应用中,200℃×32 h作为时效热处理条件较为合适,可以节约成本和能耗。
不同热处理状态下LPBF和铸造工艺制备的GWZ1221M合金室温拉伸性能对比如图10所示。显然,在不同热处理状态下,LPBF工艺制备的GWZ1221M合金的抗拉强度(YS和UTS)均明显高于铸造工艺制备的合金。以GWZ1221M合金为例,铸态合金的YS、UTS和EL分别为315±8 MPa、340±7 MPa和2.7±0.5%,而铸态合金的YS、UTS和EL分别为155±2 MPa、222±6 MPa和3.4±0.5%。固溶热处理能显著提高铸态和铸态合金的拉伸延展性。在LPBF-T4状态下,EL从构建状态的2.7±0.5%增加到6.9±0.6%。固溶热处理降低了铸态合金的YS和UTS,但降低了铸态合金的YS,提高了铸态合金的UTS。正如预期的那样,时效热处理可以显著提高YS,同时大大降低EL。将铸造t4合金在200℃下人工时效128 h,得到铸造t6合金。LPBF-T6合金的YS为320±3 MPa, UTS为395±4 MPa, EL为2.1±0.4%,与铸态t6合金相比,其抗拉强度和延展性都有了意想不到的提高。LPBF-T5合金为225℃直接时效32 h的铸态合金,铸态合金中含有大量消耗大量RE原子的β-(Mg,Zn)3(Gd,Y)相,因此从铸态到LPBF-T5状态的YS增量仅为27 MPa,明显低于LPBF-T4到LPBF-T6状态的YS增量(73 MPa)。
图4所示。GWZ1221M合金的SEM图像。
图5所示。GWZ1221M合金的EBSD晶粒取向图(a)和{0001}极形图(b)。
图6所示。LPBF-T4 GWZ1221M合金175℃和200℃时效硬化曲线。
图7所示。不同热处理状态下LPBF和铸造法制备GWZ1221M合金的室温拉伸性能:(a)典型拉伸曲线和(b) YS、UTS和EL的平均值。
总之,铸态GWZ1221M合金在LPBF过程中表现出细小的等轴晶(4.3±2.2μm)和薄的β-(Mg,Zn)3(Gd,Y)相,而铸态合金则表现出典型的粗枝晶(178.2±73.6 μm)和粗的片层共晶化合物,表明在Mg-Gd基合金的LPBF过程中,相对便宜的Mn可以取代昂贵的Zr作为晶粒细化剂。固溶热处理使硬脆的β-(Mg,Zn)3(Gd,Y)相转变为基基X相和具有较好塑性变形能力的片层状LPSO,然后峰时效处理引入大量棱柱状β′析出。铸态合金的YS、UTS和EL分别为315±8 MPa、340±7 MPa和2.7±0.5%,而LPBF-T6合金的YS、UTS和EL分别为320±3 MPa、395±4 MPa和2.1±0.4%。铸态和LPBF-T6 GWZ1221M合金的抗拉强度(YS和UTS)均明显高于铸态和成品镁合金。
免责声明:本网站所转载的文字、图片与视频资料版权归原创作者所有,如果涉及侵权,请第一时间联系本网删除。
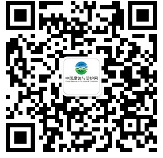
官方微信
《腐蚀与防护网电子期刊》征订启事
- 投稿联系:编辑部
- 电话:010-62316606
- 邮箱:fsfhzy666@163.com
- 腐蚀与防护网官方QQ群:140808414