高端装备的轻量化是一个永恒的发展主题,是提高服役性能、降低能耗的必要手段。提高零部件的轻量化水平有3种途径。一种是将多种不同的结构和功能集成到一个新的轻量化结构中。第二,尽可能选择力学性能高的新型轻质材料。第三,采用新技术提高零部件的服役性能,实现低成本制造。值得注意的是,形状复杂的镁合金构件不断向大尺寸、多功能方向发展。此外,作为最轻的金属结构材料,镁合金是在高端设备中实现极端轻量化的最佳候选材料。
镁合金优异的性能引起了人们的关注。研究人员对高性能材料的制备和镁合金的形变强韧化机制进行了广泛的研究,开发出了许多具有高力学性能的镁合金。大型镁合金结构件不仅要求具有较高的强度和韧性,还要求具有较高的抗冲击载荷能力。
塑性成形是提高镁合金结构件综合性能的重要手段。研究人员通过设计和优化塑性成形过程中的工艺参数,实现了关键构件中金属的有序流动、晶粒细化和纤维结构的合理分布。解决了镁合金构件应用中的一些难题,在实现设备轻量化方面表现出突出的优势。
在此,中北大学材料科学与工程学院于建民教授团队研究了具有高力学性能的大型镁合金构件成形的研究与发展现状。本文通过对变形强韧化机制、大规格铸锭坯制备和典型构件整体塑性成形工艺的分析,总结了目前高性能大型镁合金的成形进展和成形技术特点。针对大尺寸镁合金构件性能均匀性差、成形精度低、生产成本高等关键问题,提出了大尺寸高性能镁合金构件塑性成形发展趋势及重点研究方向。
相关研究成果以题“Recent research and development on forming for large magnesium alloy components with high mechanical properties”发表在金属顶刊Journal of Magnesium and Alloys上。
链接:https://www.sciencedirect.com/science/article/pii/S2213956723002207
图1 .
变形参数对镁合金抗拉强度的影响。( a ) Az80和( b ) Az91D。镁合金的力学性能对变形温度高度敏感,一般认为较低的温度会产生较好的强韧化效果。然而,过低的变形温度导致镁合金塑性较差,变形能力降低。另一方面,可以通过降低成形温度来提高强化能力。因此,实现这些因素之间的最佳匹配是镁合金塑性成形需要突破的关键技术之一。研究发现,提高变形温度虽然可以通过促进动态再结晶( DRXed )晶粒的形核来改善晶粒细化,但也会导致再结晶晶粒的长大此外,一些合金在一定的变形温度下会诱发异常织构的形成,这也会改变k值和后续的强韧化效果以及变形机制
图2 .
( a ) UTS和TYS随变形道次的变化,( b-e )不同晶粒随变形道次的变化变形程度:提高变形程度可以有效细化组织,提高镁合金的韧性。通常,构件力学性能的提高通常是通过改变挤压比、轧制压下量和变形道次来增强晶粒细化效果。例如,Dong等研究了Mg - 13Gd - 4Y - 2Zn - 0.5 Zr ( wt . % )合金在多向锻造( MDF )过程中的微观组织、织构演变和力学性能。结果表明,随着MDF道次的增加,合金的平均晶粒尺寸逐渐减小。4道次后,合金平均晶粒尺寸细化至2.7 μ m,组织分布均匀。极限抗拉强度( UTS )和拉伸屈服强度( TYS )分别为385 MPa和360 MPa
图3 .
( a )普通冷却和( b )强制风冷的间接挤压过程示意图,( c-d )电子背散射衍射 ( EBSD )图像极图( IPF )和对应的( 0001 )极图( PF ),( c )对应( a ),( d )对应( b )。变形后冷却速度:快速冷却可以提高强韧化效果。变形后不同的冷却速度导致了组织分布的差异,从而改变了镁合金的强韧化效果。例如,Xu等通过对挤压后的Mg - Gd - Y - Zn - Zr合金施加强制空冷,实现了优异的强韧化协同效应,获得了具有较小再结晶晶粒的双峰组织(图3 )。
图4 .
不同MDF道次,( a , e , i) 3道次,( b , f , j) 5道次,( c , g , k) 7道次,( d、h、l) 9道次后样品的( a-d )的IPF图,( e-h )的极图和( i-l )分布的基面( 0001 ) Schmid因子。变形道次:多道次变形可以增加累积变形程度,有利于镁合金的强韧化。但变形前不同的加热温度和时间对后续的晶粒细化和强韧化效果有显著影响。加热次数过多或加热温度过高都会导致晶粒长大。例如,Li等采用MDF方法研究了变形道次对Mg - Gd - Y - Zn - Zr合金显微组织和力学性能的影响。发现7道次后平均晶粒尺寸由初始的76μm细化至2.24μm。然而,平均晶粒尺寸在9道次后增加到7.12μm,这归因于道次中部加热过程中的动态回复(图4 )
图5 .
大型镁合金构件示意图。大型高性能镁合金构件的典型结构如图5所示。这些构件具有大尺寸、薄壁、截面变化剧烈、局部孔洞或突起以及纵向或横向高筋等几何特征。随着构件的大型化和复杂化,其变形过程中的传力路径和变形状态存在较强的不确定性。成形过程中力的传递路径和变形状态的强不确定性伴随着构件的大型化和复杂化,其结构演化、性能和残余应力也表现出随机性。尺寸效应对大型构件有以下两个方面的突出影响:( i )不同区域变形程度、温度和冷却速率的不均匀性导致构件各区域之间的性能存在显著差异;( ii )大型构件的成形精度难以控制,尤其是局部特征的成形。
图6 .
锻后应变分布,( a )预锻主轴颈,( b )终锻主轴颈,( c )预锻连杆颈,( d )终锻连杆。颈加热和冷却速率以及成形温度的不均匀分布。这导致大尺度构件不同区域的应变和性能差异显著。大型构件具有复杂的截面结构,较高的高厚比导致坯料与模具之间的摩擦副性能存在显著差异。这些导致强烈的不均匀变形,不同区域的金属流动和温度变化。甚至会导致湍流流动,造成构件流变行为的不稳定。这些现象会导致金属块、扭曲、起皱、屈曲和断裂等挤压缺陷的形成,严重影响构件的成形性能。此外,由于复杂构件的微观组织形貌、尺寸和分布具有较高的应变速率/温度敏感性,导致其性能参差不齐(图6 )。
图7 .
大型结构构件的变形过程。大尺寸构件截面变化剧烈,不同区域的升温、降温速率和变形程度存在显著差异。因此,成形件性能的均匀性必然较差(图7 )。此外,镁合金成形性差,不易填充复杂模具型腔,导致大型镁合金构件多采用频繁加热的多工步成形工艺。形状复杂性和大尺寸的耦合往往导致严重的局部软化和变形的不均匀性。
总之,高性能镁合金主要依靠变形强化和韧化,而塑性成形是提高镁合金结构件的力学性能的重要手段。目前,研究者们在强韧化机制以及变形参数如变形程度、变形温度、冷却速率和加热次数对变形行为和强化效果的影响等方面取得了显著的进展。镁合金构件的形状和性能的综合调控是一个发展趋势。对于大尺寸的塑性成形镁合金结构件,如何在关键区域实现金属的有序流动、组织细化和纤维结构的规则分布是难点。因此,通过合理设计、优化和调控塑性成形过程中的变形参数,提高镁合金构件的综合性能和承载能力,已成为该领域众多学者研究的热点问题。各种构件在塑性成形过程中具有一些共同的特点,如:各区域的结构特点不同,变形极不均匀;大型构件(凸台、凹槽、环筋等。)成形困难或充不满的局部特点;大型构件需要较高的成形力等。基于上述问题,提出了关键技术:
(1)针对大尺寸构件成形不均匀的问题,采用MDF或镦挤复合等成形技术实现高性能坯料的均匀制备,并根据大尺寸构件的形状特征和要素反向设计坯料形状,减少各向异性,为大尺寸构件的均匀成形奠定了基础。
(2)对于具有大投影面积和高成形力的大型构件,通过主动抵消摩擦阻力的结构设计、拉深辅助挤压和局部加载技术可有效降低成形力,并通过合理设计局部加载顺序和无缝集成各加载道次实现成形缺陷的消除。
(3)对于大型构件难以形成(凸板、凹槽、环筋等。)的局部特征,可基于分流分流成形原理,通过修改活动镶块、阻尼块等模具结构,调控金属流动的合理分布,使箱体内部的凸板、凹槽等特征充分成形。此外,内筋结构可以通过旋转挤压或强力旋压整体成形。
(4)针对大型构件成形一致性差、质量不稳定的问题,可采用复合成形工艺来减少成形工序,如膨胀挤压复合成形、等温超塑性挤压-模锻成形、复合挤压-胀形、模锻-胀形-旋压等。
免责声明:本网站所转载的文字、图片与视频资料版权归原创作者所有,如果涉及侵权,请第一时间联系本网删除。
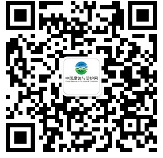
官方微信
《腐蚀与防护网电子期刊》征订启事
- 投稿联系:编辑部
- 电话:010-62316606
- 邮箱:fsfhzy666@163.com
- 腐蚀与防护网官方QQ群:140808414