发展核能是实现中国碳中和目标的主要方法之一,而2011年的福岛核事故证明冷却剂泄露事故(LOCA)严重威胁核电安全,其原因在于结构材料腐蚀、氧化产氢带来巨大安全隐患。现有研究提出燃料组件结构材料表面涂层保护技术,以避免传统燃料组件材料氧化产氢带来的核燃料泄露威胁。金属氮化物涂层(例如TiN, CrN)具有出色的热稳定性和良好耐腐蚀性被认为是保护涂层,其中最关键的抗辐照性能则有待进一步加强以保证防护涂层的耐候性。现有增强材料抗辐照性能主要思路在于提升材料内部界面密度,以界面作为尾闾,促进辐照所产生缺陷之间复合与湮灭,其内在机制则是界面无序原子在辐照过程中形成“吸引-释放间隙原子”,其促进效果与界面特征相关。
对于结构材料抗辐照性能强化技术路径则主要有细晶强化增加晶界与第二相强化增加相界面两种,涂层材料抗辐照性能提升策略则包含细晶强化、多层复合以及晶体内部空位设计,而细晶强化使得整体自由能升高,使得材料热稳定性与辐照稳定性在一定范围出现明显下降,晶体内部空位设计则会牺牲材料力学性能,因而多层复合结构在能有效强化涂层力学性能,同时界面可有效阻碍腐蚀介质扩散,因而对于抗辐照性能强化具有良好的提升效果。此外,多层结构中可形成层间材料外延生长,生成新界面。
在之前的研究中,纳米复合结构TiSiN涂层的纳米晶-非晶界面被证明具有显著的抗辐照性能提升效果,基于以上理论与前期研究结果,华中农业大学万强副教授与武汉大学杨兵教授采用多弧离子镀技术制备CrN/TiSiN纳米复合多层涂层,调整工艺,通过分层结构与外延生长,设计出层界面与共格界面共同构筑的3维界面网络,对涂层进行He+辐照,表征涂层结构与硬度变化,验证层界面在吸收缺陷、阻碍涂层非晶化的作用,同时提出3维界面网络有效促进辐照所产生氦泡的扩散的策略。相关研究成果以题“Enhancing irradiation tolerance via building 3D diffusion paths for He+ in multilayers by epitaxial growth”发表在《Materials & Design》上。
论文链接:https://www.sciencedirect.com/science/article/pii/S0264127522006426
图1 -70 V 偏压制备的CrN/Ti75Si25N纳米复合多层涂层截面TEM结构与元素分布
图2 -70 V 偏压制备的CrN/Ti75Si25N纳米复合多层涂层显微结构
所制备CrN/ TiSiN涂层为纳米复合多层结构,其中TiSiN涂层较薄,而CrN涂层生长快单层较厚,层周期为16 nm左右,TiSiN为纳米复合结构,CrN与TiN均为纳米晶,同时成功在层间通过外延生长形成所设计的共格界面,与层界面一起构筑3维界面网络。
图3 辐照前后涂层硬度及其变化比例
辐照使得涂层硬度出现变化,其中高偏压下涂层硬度均出现下降趋势而低偏压下涂层硬度升高,偏压增大能有效降低涂层辐照后的硬度变化比例,但其影响并非单纯线性关系,150V下,涂层展现出最小硬度变化,约为7%。可见,晶粒细化对于抗辐照性能强化存在临界效应。
图4 CrN/ TiSiN涂层辐照后结构损伤
图5 M4损伤层的HAADF分析
在辐照后涂层表面出现明显非晶层,非晶化会导致涂层硬度下降,非晶层深度在不同涂层中并不相同,其中在高Si样品中,涂层非晶层厚度随偏压升高而逐渐增大,高偏压下制备样品则在Si含量升高之后,非晶层厚度逐步减小;HAADF的mapping分析表明,这一非晶层主要集中于CrN涂层,而TiSiN涂层相对完整,非晶化的CrN涂层出现明显的晶体分解现象,使得层间界面在互扩散下消失,导致硬度进一步下降。
图 6 辐照后不同涂层氦泡分布显微显微分析
涂层层间界面出现大量氦泡,明显的长大现象,氦泡长大聚集之后,在层界面形成线分布模式,从而在层界面观察到大量的氦泡线排列,导致涂层出现硬化现象。涂层内部垂直与涂层界面方向也有部分的线排列氦泡,这些垂直方向界面为多层涂层共格生长界面(CI),这些界面可有效吸收He+,从而降低氦泡在层界面聚集,减少多层涂层的脆化倾向。CI界面附近发现一些无氦泡区域,这些区域为层界面与CI界面周围,再次验证CI界面可有效传导He+,当CI界面延伸至表面,则可减少内部He浓度,降低辐照失效风险。
图7 3维界面网络对于涂层氦泡扩散以及辐照力学性能变化的影响机制示意图
由层界面与共格界面所构成的三维界面可有效的实现涂层抗辐照性能提升,其中层界面能有效吸收缺陷,降低辐照非晶化倾向,而共格界面有效提升氦泡扩散,降低涂层肿胀与脆化风险。
免责声明:本网站所转载的文字、图片与视频资料版权归原创作者所有,如果涉及侵权,请第一时间联系本网删除。
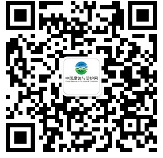
官方微信
《腐蚀与防护网电子期刊》征订启事
- 投稿联系:编辑部
- 电话:010-62316606-806
- 邮箱:fsfhzy666@163.com
- 腐蚀与防护网官方QQ群:140808414