近年来,热成形钢在汽车轻量化与结构安全性方面发挥了至关重要的作用。以白车身为例,部分车型上的热成形钢应用比例接近50%。国内的热成形钢生产线也从2011年的11条增长至2020年的180条以上。在热成形过程中,为避免钢材表面的氧化、脱碳,通常会在热成形钢表面预涂镀Al-Si镀层。Al-Si镀层由ArcelorMittal公司在2007年首次实现商业化,在避免氧化、脱碳的同时,又具有提高耐蚀性、可直接涂装、保护模具等优点,极大地推动了热成形钢和热成形技术的发展。
然而,在实际应用中,传统Al-Si镀层热成形钢对比同等强度的裸板,其弯曲韧性大幅降低,这限制了车身安全结构件的进一步轻量化。最近,东北大学易红亮教授等人开发出了新型薄铝硅镀层(专利授权公告号CN 108588612B),通过减薄铝硅镀层厚度,改善热成形钢的弯曲韧性,并也兼具了传统Al-Si镀层避免氧化、脱碳的、提高耐蚀性、可直接涂装、保护模具等优点。但目前,该新型薄铝硅镀层改善韧性的具体机制仍不完全清晰。
香港大学机械工程系黄明欣教授团队的最新研究,通过分析Al-Si镀层热成形钢的裂纹扩展与断裂机制,解释了薄镀层改善热成形钢弯曲韧性的具体原因,有望推动传统厚Al-Si镀层向新型薄Al-Si镀层的转变。相关论文于近日以题“Improving the bending toughness of Al-Si coated press-hardened steel by tailoring coating thickness”发表在Scripta Materialia 上。
论文链接:https://doi.org/10.1016/j.scriptamat.2020.10.008
本研究首先对Al-Si镀层的微观组织与裂纹扩展进行了分析。研究发现,Al-Si镀层热成形钢在热成形后的微观组织主要由金属间化合物层、铁素体层、马氏体基底构成。其中,金属间化合物呈脆性,在热成形后就已经存在裂纹,是镀层裂纹的源头,尽管铁素体层韧性相对较好,但仍然无法阻止裂纹向基底扩展。其主要原因可能在于两方面:高Al/Si含量的铁素体,由于Al/Si固溶造成大量晶格畸变,其本身呈脆性;低Al/Si含量的铁素体,厚度仅为1-2μm,不足以有效阻碍裂纹扩展。同时,在厚镀层与薄镀层热成形钢中靠近镀层的区域,均未发现高碳片状马氏体。
通过对比厚镀层与薄镀层热成形钢的力学性能,发现两种热成形钢的拉伸性能与显微硬度非常接近,但是按照VDA238-100标准测得的弯曲韧性却存在明显差异,薄镀层热成形钢的弯曲韧性明显更好。研究分析了弯曲试验后的微观组织与断口形貌,发现在弯曲变形过程中,断裂总是从样品表面开始,因而弯曲韧性对镀层裂纹更加敏感,镀层裂纹在扩展至马氏体基体后,在裂纹尖端会形成高应力集中,可以诱发局部剪切变形,最终导致断裂。通过建立裂纹扩展模型发现,薄镀层由于镀层厚度更小,镀层裂纹长度更短,裂纹尖端的应力集中也更小,因而薄镀层热成形钢的弯曲韧性也更好。
同时,该论文附件也给出了薄镀层热成形钢涂装性能与耐蚀性能的评价。这些评价是在通用汽车公司认证的第三方实验室进行的,包括了附着性能、落石冲击性能、循环腐蚀性能等。评价发现,薄镀层热成形钢的涂装性能和耐蚀性能与厚镀层热成形钢没有明显差异。
总而言之,本研究解释了薄镀层改善Al-Si镀层热成形钢弯曲韧性的微观机制。在改善弯曲韧性的同时,薄Al-Si镀层热成形钢具备出色的涂装性能与耐蚀性能,又能够节约镀层原材料成本、提升热浸镀效率,有望在未来替代传统厚Al-Si镀层,影响全球热成形钢产业。
图1 两种Al-Si镀层热成形钢的微观组织。
图2 Al-Si镀层中铁素体层的TEM表征。
图3 两种Al-Si镀层热成形钢的力学性能。(AlSi13为薄镀层、AlSi35为厚镀层)
图4 Al-Si镀层热成形钢在变形后的微观组织。在弯曲变形后,可以观察到Al-Si镀层裂纹诱发的剪切带。
图5 两种Al-Si镀层热成形钢的断口形貌。
图6 两种Al-Si镀层热成形钢的附着性能试验。
图7 两种Al-Si镀层热成形钢的落石冲击试验。
图8 两种Al-Si镀层热成形钢的循环腐蚀试验。
免责声明:本网站所转载的文字、图片与视频资料版权归原创作者所有,如果涉及侵权,请第一时间联系本网删除。
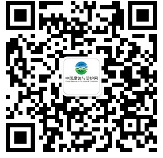
官方微信
《中国腐蚀与防护网电子期刊》征订启事
- 投稿联系:编辑部
- 电话:010-62316606-806
- 邮箱:fsfhzy666@163.com
- 中国腐蚀与防护网官方QQ群:140808414