日前,由东北大学许云波教授团队研发的高强塑积汽车钢在河钢唐钢高强汽车板连退生产线成功下线,力学性能全部达到指标并获得用户订单,标志着我国首次在以“较低冷却速率和一步过时效处理”为特征的传统连续退火生产线上成功研发具有优异力学性能的第三代汽车钢,河钢唐钢也成为国际上首家掌握这项技术并投入工业化应用的企业。
随着能源危机和环境恶化的日益加剧,安全、节能和环保已成为汽车制造业的发展潮流。在保证使用安全的前提下,汽车轻量化是汽车节能减排最有效的方法。因此,近年来全球各大钢铁企业纷纷加大了第三代汽车钢的研发力度,力求通过车身减重实现汽车“更省油、更安全”的目标。作为第三代钢典型代表之一的淬火配分(Q&P,Quenching and Partitioning)钢,因其优异的强塑性能和适合工业化批量生产的技术特点而成为其中最为瞩目的明星。
2003年,美国物理冶金学家Speer教授提出Q&P工艺的概念,之后短短十多年时间,中国宝钢利用其先进的具有“高温均热、高速冷却和淬火再提温”功能的高强专用退火线把Q&P钢从概念变成了商业化产品,鞍钢也采用“快速冷却+两步配分”方法打通了高强Q&P钢的工业化路径,这使得中国在第三代高强钢开发和应用方面走在世界前列。
然而,按照经典的淬火配分理论,为了获得优异的强塑性能,传统连续退火生产线必须拥有高速冷却和淬火后快速提温(“两步配分”)等特殊功能。而配置如此豪华的一条高强钢专用退火生产线投资动辄八、九个亿,有的甚至高达十多亿。国内已有和在建的四十余条大型连续退火产线中,仅有两、三条具备这样的条件。因此,大部分钢企对于具有诱人性能的高强Q&P钢只能望洋兴叹,这极大地限制了新一代高强塑积汽车钢的推广和应用。
在冷却速率不高、不具备淬火再提温功能的传统连续退火生产线上开发第三代高强钢,逐渐成为学界和业界共同追求的目标。为解决这一行业共性技术难题,东北大学轧制技术及连轧自动化国家重点实验室许云波教授团队深入开展淬火配分理论和关键工业化技术的研究,突破单独依赖马氏体向奥氏体碳配分的传统框架,提出“铁素体、贝氏体和马氏体协同碳配分”新概念与新工艺,通过合金成分设计、奥氏体稳定化和多相微结构的精准调控,在国际上首次基于河钢唐钢传统连续退火生产线的较低冷速与一步过时效处理,成功开发出QP980钢。这一钢种成品板屈服强度≥600MPa,抗拉强度≥980MPa,断后延伸率达到21~28%,综合性能表现优异,这使河钢唐钢成为继中国宝钢、鞍钢之后国内又一家具备QP980供货能力的汽车钢制造商。
与同级别“两步配分”商业化Q&P钢相比,新技术温控路径简单,配分窗口灵活,生产衔接顺畅高效,工艺成本降低,仅取消“感应提温”一项就可以节约电费50~100元/吨。而且,新产品典型组织和力学性能表现优异,通卷性能波动小,抗回火稳定性强,显微组织中残奥体积分数提高2%~6%,断后延伸率增加2%~4%,强塑积可达27GPa?%以上。电阻点焊及成形性能与“两步配分”产品典型值基本相当,其中折弯、回弹等性能更优,1.6mm板临界相对弯曲半径降至1.5mm左右,90°折弯回弹角可达到约14°。
此外,与同级别冷轧双相钢(DP)、相变诱发塑性钢(TRIP)相比,不仅合金成本大幅度降低,而且钢材韧塑性、成形性和延伸凸缘性等显著提高,特别是延伸率达到了同级别DP钢的两倍以上。
新型Q&P钢可用于横梁、纵梁、车窗框架、保险杠及地板加强件等汽车结构件,通过减薄零件厚度,减少燃油损耗,有效实现节能降耗。例如,使用QP980替代DP600,工件厚度由1.2mm减薄至1.0mm,可为汽车减重10%~20%。同时,汽车安全性显著提高,在正常碰撞下人员死亡率大幅度下降。新技术的成功开发与应用,将全面打通基于传统连退线的第三代高强塑积汽车用钢的设计、研发、生产与应用产业链,进一步推动我国汽车轻量化钢铁材料研发与应用达到国际领先水平。
— END —
更多关于材料方面、材料腐蚀控制、材料科普等方面的国内外最新动态,我们网站会不断更新。希望大家一直关注中国腐蚀与防护网http://www.ecorr.org
责任编辑:王元
投稿联系:编辑部
电话:010-62313558-806
中国腐蚀与防护网官方 QQ群:140808414
免责声明:本网站所转载的文字、图片与视频资料版权归原创作者所有,如果涉及侵权,请第一时间联系本网删除。
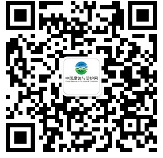
官方微信
《中国腐蚀与防护网电子期刊》征订启事
- 投稿联系:编辑部
- 电话:010-62316606-806
- 邮箱:fsfhzy666@163.com
- 中国腐蚀与防护网官方QQ群:140808414